废轮胎橡胶是重要的可再生资源,将废轮胎制备成再生材料,再循环应用于新轮胎中,对于消除废轮胎黑色污染、降低橡胶资源对外依存度意义重大。但现有的轮胎循环再利用技术存在高污染、低效率、质量差的问题,开发绿色化、资源化、高值化的轮胎循环再利用技术非常迫切。由中策橡胶集团股份有限公司、南京绿金人橡塑高科有限公司、北京化工大学等合作开发的“万吨级废轮胎橡胶材料绿色自循环再生及应用技术示范”项目突破了废轮胎绿色高值化再利用技术,建成了轮胎绿色自循环应用示范,并于近日荣获2023年度中国石油和化学工业联合会科学技术奖科技进步一等奖。
目前,我国废轮胎形成了以制备再生橡胶为主,制备胶粉、轮胎翻新、热裂解协同发展的再利用格局。其中,废载重轮胎橡胶一般采用高温高压动态脱硫罐技术制备固体再生橡胶。该技术存在解交联不可控、长时间高温高压导致能耗高和生产过程中废气、废水难处理等问题。解决这些问题的核心是实现废橡胶的可控解交联再生。
“轮胎橡胶的分子结构本是线型的,为达到其使用性能通常需在其中加入硫黄进行硫化,使其形成三维立体网络结构的热固性材料。该结构导致废橡胶材料不溶,难以通过简单加工后再应用到新轮胎中,所以废轮胎橡胶回收的第一步就是将橡胶中的硫交联键解交联,破坏其三维网络结构,使其具有可再加工性能。”南京绿金人橡塑高科有限公司总经理史金炜博士解释道,可控选择性解交联并不容易,废载重轮胎橡胶中的交联键只有不到2%、又有多种交联键类型。在课题研究之初,优异、稳定再生性能的解交联机理和绿色化再生废橡胶的装备均尚无先例。
另外,废乘用胎通过热裂解技术回收制备裂解油、裂解炭黑,一般采用的“土法炼油”因污染大被国家禁止,而通过环保高温热裂解技术回收废乘用胎,存在设备投资大、产品收率低、产品品质差等问题。
“这是因为废乘用车轮胎的补强体系复杂,特别是因‘绿色轮胎’的要求,配方中白炭黑补强剂的用量越来越高,而经过高于450℃高温热裂解后,炭黑、白炭黑等补强剂失活,性能差,且难分离、难改性,产品经济附加值低。”史金炜解释道,因此急需原创一种新的再生橡胶材料,既可实现解交联又不破坏补强体系,实现高收率、高附加值。
“除此之外,所得再生材料在轮胎中的应用因缺乏系统理论研究而脱节,应用后轮胎高性能不能保持、不能稳定,只能少量掺用,严重阻碍了行业发展。”史金炜补充道,如何精准结合轮胎不同部位性能要求,实现再生材料的高性能稳定再应用,科学的配方设计也是一大难题。
研究团队历时十几年的攻关,研发出废轮胎橡胶材料绿色自循环再生技术,终于解决了上述难题。该技术有以下创新点:第一,阐明了废橡胶解交联再生机理及再生材料结构、性能演变,指导了满足必要再生条件的专用设备设计和制造。第二,首创建立了废胶粉摩擦传递机理,研制了脱硫、精炼、中度裂解、冷却排气等不同功能的系列双螺杆挤出机核心装备,目前已实现单条线回收1万吨废载重轮胎和5000吨废乘用胎。第三,结合双螺杆挤出机内的剪切场和温度场的模拟设计,开发了螺杆组合结构和工艺控制技术。第四,设计了固/液体再生橡胶在轮胎胎面、胎侧、胎体等部件上的应用配方和工艺,实现了对树脂、油、炭黑、合成橡胶等石化产品和天然橡胶的替代应用,在保证性能的同时,降低了材料成本。
该项目已经形成了轮胎生产—销售—回收处置—再利用的全周期自循环模式,为国内废轮胎规范回收和体系健全提供了示范,为废载重轮胎和废乘用车胎的回收再利用提供了绿色化、资源化、高值化的中国解决方案,降低了我国橡胶资源对外依存度,有利于橡胶行业的可持续发展。
目前,该技术成果已落地应用,产生了良好的经济效益。中策橡胶循环科技有限公司初步构建了废轮胎循环利用体系,形成了年处理5万吨废轮胎的规模,近3年累计处理废轮胎约8万吨,碳减排约2.3万吨,应用再生橡胶材料的轮胎销售收入达208.4亿元,节省成本约6000万元。
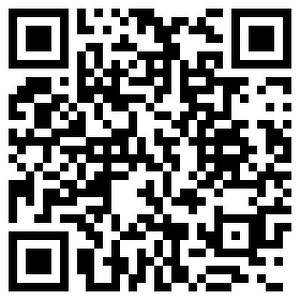
VIP课程推荐
APP专享直播
热门推荐
收起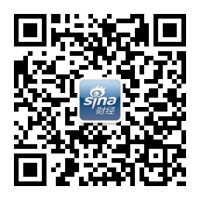
24小时滚动播报最新的财经资讯和视频,更多粉丝福利扫描二维码关注(sinafinance)