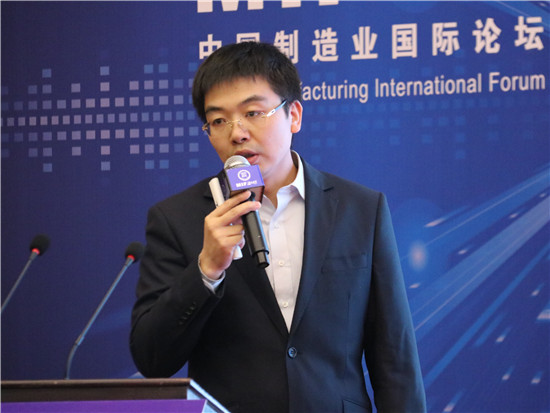
新浪财经讯 “第十五届中国制造业国际论坛”于2018年10月23日在天津举办,主题为:中国制造+互联网下的新模式与新路径,西安西电高压开关有限责任公司精益办主任陈丰辉出席并演讲。
陈丰辉介绍,西安西电高压开关有限责任公司在推行4年精益之后,把绘制了企业整体的价值流图,在价值流图所有的节点都提出了要求,在生产计划方面,往准时交付过渡,在精益供应链供应商品质的管理,以及精益物流、精益仓储和精益研发多个方面提出了不同程度的要求,对后期实施数字化做一个基础。
数字化项目的实施分为几个模块,以智能自动产线作为基础,在产线的三维模拟上对于工艺布局及物流进行优化,并对相关的工序进行了重组分解,减少了人工作业。同时信息化系统的导入也提升了产线管控的颗粒度。
以下为演讲实录:
陈丰辉:非常感谢大会给这次机会做主题分享。我分享的主题是《西开有限数字化制造规划及实践》。其主要内容是我们自2015年推行精益管理以来,在这个过程中,从精益往数字化迈进的过程的一些总结和展望。
首先我们对于企业做一个简单的介绍,西开有限是西安西电高压开关有限责任公司,始建于1955年,是第一个五年计划期间国家156项重点项目之一,是中国西电集团公司核心子公司,是我国输配电行业高压、超高压、特高压开关设计生产的公司。
今天汇报分为五部分:一是精益化制造规划,二是数字化项目背景,三是数字化项目架构,四是数字化项目实施,五是项目成果预期。
首先看一下精益管理推进策略(精益为基),我们有精益屋,构架是我们以全员参与、持续改善为基础,以精益管理和精益信息化为两大支柱,紧密围绕我们的价值链和基础管理,打造工艺水平和生产化模式,构筑了精益制造、生产管理打造了高品质、短交期、低成本、高效率的转型目标。
西开项目转型路径把转型人员分为三类,先行者作为示范引领,跟随者是普及推广,落后者进行考核普及培训。第一阶段是精益转型阶段,第二是精益数字化阶段,第三个阶段是推进智能制造阶段。
在第一阶段,在制造过程中,在制造、工艺、质量、销售环节全面导入精益管理,打下了坚实的基础和持续的文化。在精益数字化阶段我们以精益化支撑,实施融合了精益思想的集成,实施了精益全价值链体系。到《智能制造2025》国家级目标,采用了3D打印、大数据等等路径实施了数字化实施架构路径。
同样我们也有数字化制造的整体架构,时间上分为四个阶段,基础平台扩建、精益加信息化的试点建设,全面信息化扩展落地,整体的扩展。从销售到产品链条、销售、运营管控、设备、人员、售后服务、管理维护每一块都有自己的特点,销售端是移动端的产品管控,供应商管理方面我们实施的是采购执行反馈,在车间生产执行过程控制中,我们精细化的生产计划分解下来的执行反馈。同样在设备能源方面进行数字化的控制,在售后运营维护是移动终端的运维服务。每个点都有一个到多个信息系统进行支撑,来支撑我们的数字化落地。
我们看一下数字化的项目背景,看一下现有数字化制造的一个核心系统,在上系统之前,我们有一些系统,我们有了西门子的设计与制造协同平台,还有SAP、ERP,SAP、ERP里面涉及到的模块比较多,涉及到了SBSM、PP等相关重要的模块以及WMS的仓储物流管理。同样把刀具与模具进行了三维化设计管理,还有设备的智能控制中心,以及BVC终端,这些都比较零散,没有办法作为企业对于数字化做进一步的支撑。
因此我们在推行4年精益之后,我们把绘制了企业整体的价值流图,在价值流图所有的节点都提出了要求,我们在生产计划方面从原来的七套交付往准时交付过渡,在精益供应链供应商品质的管理,以及精益物流、精益仓储和精益研发多个方面提出了不同程度的要求,对后期实施数字化做一个基础。
这也就是在精益管理改善的基础上,智能制造支撑型,同时固化提升,实现精益管理的落地,完成这次的试点项目,也就是精益全价值链的建设,从而提高车间精益管理的水平,提升生产效率、提升产品质量,降低我们的成本,最终达到智能化车间样板,为我们全面的智能制造提供基础。这是信息化高度融合,在信息化高度融合方面,在原来的ERP系统实现了一体联动化集成管理,同时在WMS里面针对原有的WMS系统开展了三个阶段的持续优化,在PRM项目,借助整个平台协助精益思想的导入和支撑,从研发源头进行精益思想的导入。今年借助精益生产系统的实施,最终实现精益化数字系统的管理。
说完数字化项目的背景,我们看一下数字化项目的整体架构。这个就是我们数字化项目整体架构的一个业务流图,也就是说最终在业务端实现数字化的一个情况。从左边来看,我们的集成交互,也就是把我们现有的系统我们的PRM系统跟SAP、WMS系统进行一个有效的集成、进行交互。我们借助推行了4年的生产体系,四级联动计划,销售交付、一体联动、物量销售计划和工业生产计划,所有的计划都推送到现场终端进行一个现场执行,协同我们的物料配送跟设备管理,最终达到有效落地。
最终所有的数据都反馈给我们的数据应用层,数据应用层包括系统管理、判断管理、追溯管理和绩效管理,整个构成了精益数字化业务落地的模式。
我们的业务范围包含了实物模块,涵盖了MES的所有模块,生产管理、业务管理、质量管理、数据管理、数据监控以及一体集成,关注了生产数据,在生产计划主要是工业计划的一些排查,在生产管理进行全过程的一个执行监控,物流管理重点关注了工位节拍的监测,异常检测、质量管理对质量进行追溯,工艺管理优化了工艺现状,设备管理关注了故障率等等,在数据监控对于数据进行了采集监控,所有的东西是把现有的系统以及实施的系统进行了全方位的有效集成。
我们的车间是护板漆车间的一个全覆盖,AGV配送,工装全面改造,同时把原来的设备都加在PSE终端进行了互联互通,可以看到分为四个区域,有浇铸区、电压互感区以及原材料库,所有的设备都进行了有效联网,同时在电流互感器方面进行了一个装配线,同时还有四台控制系统。
上面说了我们的规划、背景以及架构,最后重点说一下数字化项目的实施,分为几个模块。首先我们作为数字化项目实施,我们的智能自动产线也是我们的一个基础,这是我们产线的三维模拟,在产线的三维模拟上对于工艺布局及物流进行一个优化,打通了相关的断点,我们对相关的工序进行了重组分解,减少了人工作业。同时信息化系统的导入也提升了产线管控的颗粒度。
这个是我们智能产线围绕的几个核心:
首先智能产线是智造一流产品服务一流客户。一是生产管控颗粒物的提升。二是车间物流能力的提升。三是生产过程信息化的提升。四是生产过程透明度的提升。五是产品质量管控能力的提升。以上五个提升,最终展现在车间生产效率,最终车间生产效率要进行一个大幅度提升,即有效的自动化和MES系统迅速有效地收集各个工位的时间,有效地对产线瓶颈进行一个优化。
在系统集成方面,有很多数据要进行相互的交换,我们有原来的PRM、ERP以及WMS,在整个数据上都通过MES系统进行有效地集成,同时MES也接受产线上PSC终端以及装备的信息,同时对物流进行相关的管控,最终实现智能产线。有了产线最终还要看计划,看一下高级排程,来源是SAP的销售订单导入,SAP的销售订单导入进系统之后,根据一体联动计划,一体联动计划的颗粒度是比较细的,分到每一道工序,每一道工序的开工和完工时间,同时依据交期、生产能力以及生产需求,进行分析,分析之后分出分配装配线以及PT装配线的计划。
数字化项目实施-计划下发。包括标准作业、图纸、测量标准以及人员的资质,什么人在这个工位上去执行。数字化项目实施-生产工艺管理,工艺文件可以直达现场,工艺过程可以进行全过程一个引导,同时提高了标准化,提高了工艺设计的柔性化。可以查到动态C3D结构化的初始,丰富了现场工人的装配,可以进行现场数据的收集,丰富了在线参数以及检验设备的参数可以自动在线收集。
数字化项目实施-生产任务管理,生产任务管理是我们按生产计划进行任务推送,首先把我们的资源设置进行了一些整合,我们所有的资源都围绕着人机料法环,都输入我们的后台,进行同时信息推送,作业指导、工艺路线以及检验指导的相关文件。在开工之前这些参数和文件进行审核,审核过后可以进行工序,达到装配和现场的实时交互。
数字化项目实施-生产任务执行,操作者由手持终端和工控机,按数分配给自己的任务,按实时作业和引导作业执行。可以确保产品质量,同时生产质量制定和下达,工艺测定和质量实施,生产工艺结果的估值化和信息化,进行相关作业的展示。
数字化项目实施-生产统计报表。对于生产过程中以及历史结果数据的结果进行统计分析,工位作业运行图,可以看到工位是否处于异常状态,包括任务计划兑现图,任务是否负荷,负荷有多大,是否超负荷。在生产过程中,我们整个计划变动量比较大,在这里所有的变动都可以在系统上有效得到体现,变动次数以及变动的情况,现有的某个工程在所有工程中占比情况,这样可以确保我们锁定重大的工程,所有的报表也是进行一个现场的实时交互。
数字化项目实施-质量管理,在质量管理方面,我们订单管理开始到检验测化、检验任务、检验结果管理,包括到输出管理。整个的过程由智能装配产线进行全过程智能监控,所有的异常都反馈到异常管理模块。不合格品处理以及设备参数、实验室这些相关数据,一旦发生异常,我们也会反馈给我们的异常管理的模块。异常管理模块接收到这些信息以后,进行统计分析以后发回现场看板,都可以实时舰空导我们的异常,能够包括到异常得以解决。
数字化项目实施-物流管理,从被动式到主动式的生产,包括信息共享、通畅,条码管理以及仓储规划,最终实现订单的达成率达到百分之百。优化仓储能力,提高的物流管理,作业信息化、可追溯管理、数字化管理、超强预警最终实现实物流与信息流的同步。
数字化项目实施-设备管理方面,设备管理信息化可以系统地接收到终端,将故障推送给服务器,最终接收到实施方案,自动接收到需要保养和维护的时间,同时这些数据经过我们的智能分析平台推送给相关人员,包括可以在现场进行一个综合管理。在设备管理方面,还有一点建立维修知识库,也就是说在设备故障后,工人在设备终端选择故障现象,系统根据故障现象查询维修工艺,有的话自动创建维修工单,排查和采集数据,自动进行作业,弱没有的话人工创建维修工单,在系统内针对此类故障现象,供下次同类故障时调用,从而实现我们的知识库管理,这是整个设备维修的知识库。
数字化项目实施-异常管理,采用手机终端对于现场发生的异常进行实时开放,这样通过所有的交互平台,我们的移动终端、异常管理、工业终端把所有的异常发布给各个平台,在第一时间得到问题的解决,对于不同层级规定了不同的时间,提升了我们的响应速度,做到异常的在第一时间被相应的人去看到。
同样在生产中控方面,多维度统计分析以及定向推送,通过了几个维度,也就是经常说的决策层、管理层等,包括产线质量的统计,在运营层,关注的一些缺陷类的统计,包括设备故障类的统计,能源费用的统计。决策层包括生产成本、准时交付的分析,这些所有的统计报表都会给不同的决策层提供支撑的依据。
最后这是我们未来要建成的一个中控指挥中心,我们这个项目还在实施过程中,今年年底到明年年初我们的项目正式完结了,展示的结果也就是我们预期规划的样子。
时间的原因,我们的数字化项目实施只能简单介绍这么多,最后看一下项目成果的预期。项目成果的预期,精益数字化实施要做哪些事情?精益数字化实施首先要做的是实施获取数字,结构化工艺设计,产品质量追溯,资源配置优化,实施任务分配,异常管理,过程数据采集、分析,最终要做到缩短我们的制造周期。
给项目定了两个目标,一个是定量目标一个是定性目标,定量目标产线生产周期缩短20以上,产线生产效率提升10%以上。定性目标,固化精益全价值链连续流产线规则。减少人工动作,降低人员劳动负荷。
效果描述,计划兑现更准确,信息时时反馈,计划制定更合理。计划调整更灵活,使用信息化手段自动排产。系统集成联动,减少在制品、物料库存。提高管理效率,产能提升。异常管理项目目视化。
最终是整个数字工厂自展示,内部有智能产线、智能仓储、智能物流,外部有智慧能源、决策支持,安全与环境,更外一层有供应商的协同以及客户服务。总体构成了未来数字化工厂的一个场景。
我的分享就到这里,谢谢大家!
新浪声明:所有会议实录均为现场速记整理,未经演讲者审阅,新浪网登载此文出于传递更多信息之目的,并不意味着赞同其观点或证实其描述。
责任编辑:谢长杉
热门推荐
收起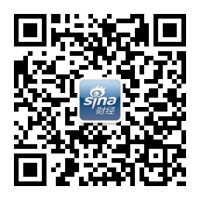
24小时滚动播报最新的财经资讯和视频,更多粉丝福利扫描二维码关注(sinafinance)