炒股就看金麒麟分析师研报,权威,专业,及时,全面,助您挖掘潜力主题机会!
(报告出品方/作者:广发证券,孟祥杰、吴坤其、代川)
一、3D 打印:提高材料利用率、兼顾复杂结构与高性 能的新工艺
3D打印,又称增材制造(Additive Manufacturing,AM),是对于传统工业生产的 一种“变革性”方法。传统的减材制造工艺是指利用已有的几何模型工件,用工具 将材料逐步切削、打磨、雕刻,最终成为所需的零件。而3D打印恰恰相反,通过借 助于3D打印设备,对数字三维模型进行分层处理,将金属粉末、热塑性材料、树脂 等特殊材料一层一层地不断堆积黏结,最终叠加形成一个三维整体。3D打印作为一 项新兴技术,已在航空航天、汽车、生物医疗、电子、建筑等领域有所应用。
与传统制造工艺相比,3D打印具有可成形复杂结构、产品研发和实现周期短、成功 率高、生产成本低、材料利用率高、产品强度高重量轻等优势。根据《西安铂力特增材技术股份有限公司2022年度向特定对象发行股票证券募集说 明书》,3D打印技术的比较优势具体如下:(1)缩短新产品研发及实现周期。3D 打印工艺成形过程由三维模型直接驱动,无 需模具、夹具等辅助工具,可以极大的降低产品的研制周期,并节约昂贵的模具生 产费用,提高产品研发迭代速度。(2)可高效成形更为复杂的结构。3D 打印的原理是将复杂的三维几何体剖分为二 维的截面形状来叠层制造,故可以实现传统精密加工较难实现的复杂构件成形,提 高零件成品率,同时提高产品质量。(3)实现一体化、轻量化设计。金属3D打印技术的应用可以优化复杂零部件的结构, 在保证性能的前提下,将复杂结构经变换重新设计成简单结构,从而起到减轻重量 的效果,3D 打印技术也可实现构件一体化成形,从而提升产品的可靠性。(4)材料利用率较高。与传统精密加工技术相比,金属3D打印技术可节约大量材料, 特别是对较为昂贵的金属材料而言,可节约较大的成本。(5)实现优良的力学性能。基于3D打印快速凝固的工艺特点,成形后的制件内部冶 金质量均匀致密,无其他冶金缺陷;同时快速凝固的特点,使得材料内部组织为细 小亚结构,成形零件可在不损失塑性的情况下使强度得到较大提高。
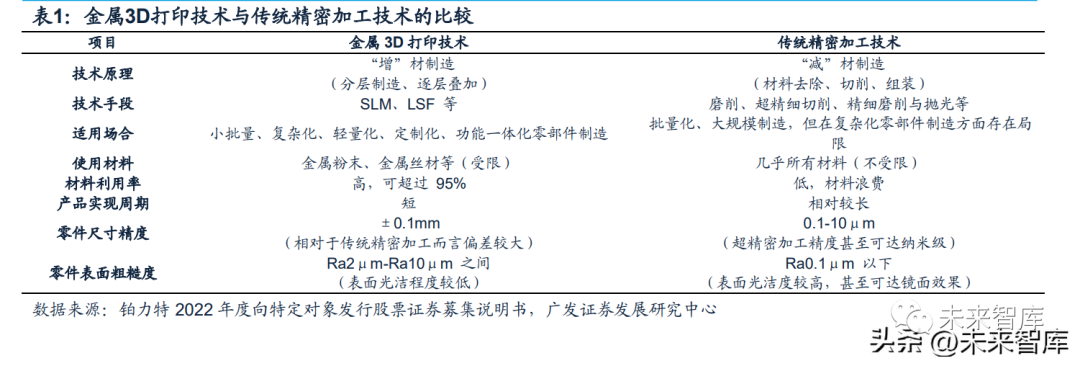
二、为什么开始用:产品升级,牵引新材料、新结构应 用新工艺
我们认为,新工艺应用的背景,在于产品升级周期,牵引对新材料、新结构的要求。
(一)民用伴随产品升级周期,新材料在高端产品领域渗透率逐步提升
例如,伴随消费电子性能和应用升级需求,钛合金凭借强度大、质量轻和耐腐蚀的 优异性能已逐步应用在高端智能产品中。消费电子通常具有小巧轻便、操作简单和 节能设计等优点。随着各类消费电子产品渗透率逐步提升,性能和应用升级成为行 业下一步发展的主要方向,其中新材料的使用是重点方向之一。电子产品金属结构 件一般以不锈钢和铝合金为主,但重量不占优势,铝合金虽有轻量优势,但硬度不 够。而钛合金的强度高于不锈钢,重量却只有同体积不锈钢的一半。因此,钛合金凭 借其强度大、质量轻和耐腐蚀的优异性能,目前已在逐步应用在高端消费电子产品。例如,根据贝哲斯咨询《钛合金未来将在消费电子领域持续渗透,国内抛磨设备厂 商有望受益》,从苹果的专利储备和已经发布的Apple Watch Ultra配备上看,使用 钛合金制作手机中框有可能成为苹果下一代手机的重要创新点之一。钛合金在消费 电子领域的应用有望进一步渗透,截至2022年12月,苹果公司已累计获得钛合金材 料相关专利8项,亚马逊、XLOONG、RokidAir等厂商都推出了使用钛合金的AR设 备。
(二)装备性能升级需求,复杂度提升,新工艺成为传统工艺互补选择
据美国国防部官网2022年10月28日新闻,美国国防部网站发布了一项最新的制造技 术提案,计划使用增材制造技术来设计和制造能够在极端条件下运行的高超音速武 器和车辆系统。据该新闻,美国国防部指出,目前,传统的制造工艺无法满足先进高 超声速武器所需的复杂结构零件的制造要求,GAMMA-H(Growing Additive Manufacturing Maturity for Airbreathing Hypersonic)计划将有助于推动增材制造工 艺的应用与发展,以满足现代高超声速空气助燃系统所需的推进和温度要求。国防 部制造技术项目办公室副主任凯文德弗里斯表示,“我们需要使用增材制造工艺制 造的材料来突破极限,科学已经证明这是可以做到的,但应用还不够广泛。GAMMAH计划将鼓励继续采用这一突破性的技术。”
三、为什么可以用:性能领先,降成本、增效率是规模 应用前提
在追求高性能的航空航天实现规模化应用,或在一定程度上证明3D打印结构件性能 已具有相对优势。2022年11月16日共青团中央公众号发布《战机零部件是3D打印的?“罗阳青年突击队”研制》一文,该文指出航空工业沈飞在新研的机型上3D打印件 已经实现批量装机,我国3D打印制造技术或已实现在飞机上规模化应用。产品升级周期如果是让金属3D打印“开始用”,那么成本降低与效率提升,则是实 现“可以用”的前提。
(一)金属粉末材料价格、设备价格、零部件国产化,为降本关键路径
成本降低路径方面,原材料价格、设备价格下降,以及核心零部件国产化等,是提 高行业渗透率的关键,并且正在发生。原材料价格方面,市场供应量增加、规模优势显现,价格呈快速下降趋势,驱动3D 打印结构件成本降低。① 据铂力特2022年年报,其3D打印定制化产品营业成本结构方面,直接材料占营 业成本比重为27%,占比低于制造费用(60%),高于直接人工(12%)。② 据《SLM打印金属零件成本分析与预测模型》(陈未,浙江大学硕士学位论文, 2019年),在优化SLM打印金属零件可变成本方面,金属粉末的单价及利用率是 主要驱动因素,粉末单价的20%价格下降可节省6.42%的可变成本,金属粉末20% 的利用率上升可以节省5.35%的可变成本。
③据铂力特《向特定对象发行股票申请文件的审核问询函的回复(豁免版)(修订 稿)》,2020年至2022年,公司自制3D打印粉末销售价格呈现下降趋势,但同时毛 利率仍保持增长,同期销售价格由2020年的144.48万元/吨,降低至2022年的78.19 万元/吨,同期该业务毛利率反而从30.81%,提升至38.98%。主要原因为:一方面, 公司自制粉末报价参考国内市场3D打印粉末平均价格水平变动,高品质金属 3D 打印粉末,尤其是航空级、医用级别的高质量粉末市场最初由国外厂商垄断,进口粉 末单价高。公司生产的3D打印粉末性能指标能够满足粉末需求方的要求,因此粉末 售价较高,随着国内3D打印粉末厂商的增加,市场粉末供应量上升,粉末平均价格 水平下降,公司销售的粉末价格随之下降;另一方面,随着公司自制粉末逐步形成 规模成本优势,2022年起,公司通过主动降价进一步开拓市场,提升公司粉末市场 知名度和占有率。
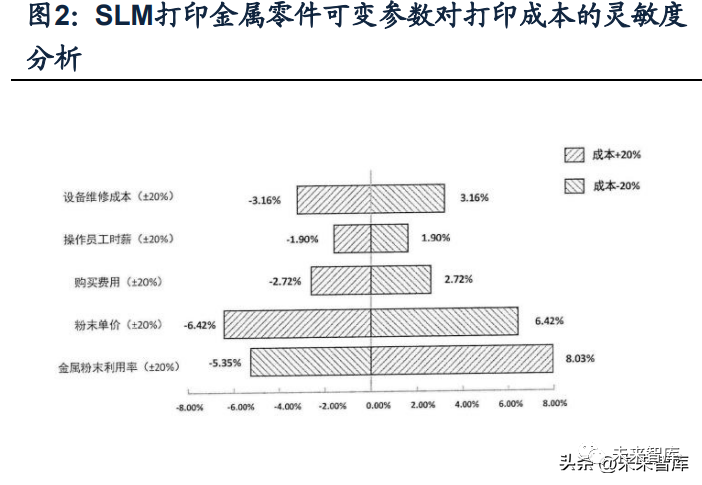
设备价格方面成本下降、性能提升。伴随技术端成熟、规模效应,以及参与者增加, 3D打印工业设备销售价格近年稳中有降,降低下游客户的使用成本;但与此同时, 设备效率不断提升,客户的使用满意度进一步增加,成本下降曲线更为陡峭。据 Wohlers Associates发布的《Wohlers Associates 2022》,2021年全球工业增材制 造系统销售平均单价为93404美金,2020年为100510美金、2019年为98105美金, 呈下降趋势。
工业增材设备一般价格较高,针对价格敏感型下游客户,设备制造商可采用国产零 部件代替进口零部件,从而降低成本以满足其成本效益方面的考虑。据华曙高科《发 行人及保荐机构回复意见》,从性能来看,国产激光器与进口激光器在输出功率、光束质量等方面不存在显著差异,在长期稳定性方面,进口激光器在功率衰减、故障 率等方面表现优于国产激光器;国产振镜在扫描速度和延时时间方面略逊于进口振 镜,在镜片可承受激光功率方面与进口振镜存在一定差距,在控制精度和温漂性能 方面国产和进口振镜表现接近。进口零部件和国产零部件虽然在技术指标方面存在 一定差异,但通常核心零部件在增材制造设备中的使用未达到其极限性能值,据公 司首轮问询披露数据显示,国产振镜和激光器整体成本较低,以主要设备型号D+产 品为例,采用进口和国产激光器的设备每台销售成本分别为53.28万元和50.76万元, 因此国产零部件替代有利于设备厂商降低成本,形成成本和价格优势。
(二)激光器数量增加、扫描速率提高、铺粉方式、工艺规划促效率提升
效率提升方面,激光器数量增加、激光扫描系统速率提高、铺粉方式升级、工艺规 划软件升级等,均是提高金属3D打印设备生产效率的重要路径。
1. 单台设备激光器数量增加是提高打印效率的重要路径之一。激光器数量增加,3D打印设备的生产效率有望实现快速改善,更适合批量化生产。据铂力特公众号2022年9月推送,聚焦制造业对生产效率的高要求,BLT-A450设备 配置六激光,与市面上同体量设备所配置的四激光相比,整机设备的单光投入降低 约30%,打印效率提升约30%。以满版分水器为例,整版可一次性成形40个零件, 成形时间由72小时缩短至了50小时。BLT-A450配置的450mm×450mm幅面使得单 版可以批量产出更多的零件,且单个零件的产出效率和产出成本也会更低;同时更 大的成形幅面可以适配更多工业大尺寸零件,例如大尺寸的注塑模,鞋模等。
激光器数量是反映金属3D打印设备生产效率的指标之一,多激光器设备伴随技术升 级销售占比逐步增加。据华曙高科《发行人及保荐机构回复意见》,公司多激光器设 备销售数量逐步提升,从单激光逐步扩展到八激光,技术升级与单价逐步提升。
2. 硬软件能力提升,振镜扫描速度提高,生产效率提升。振镜最大扫描速度是影响打印效率的核心因素之一,最大扫描速度越快,可有效减 少激光扫描跳转时间,生产效率越高。据华曙高科招股书,与同行业可比公司相比, 其高分子3D打印设备的最大成形尺寸、激光器数量、振镜最大扫描速度和最大激光 功率各项关键技术指标均居于首位,设备的成形效率达到国际领先水平。
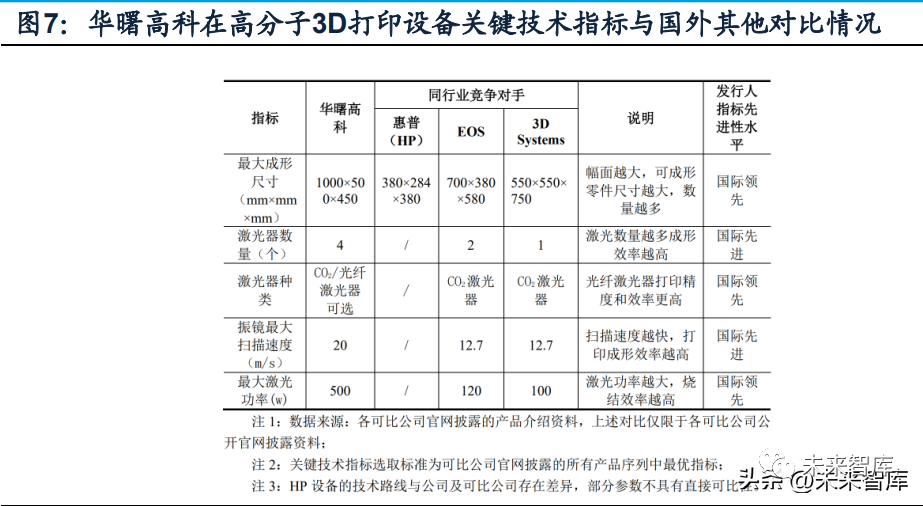
3. 铺粉、添粉方式改善,也是提升设备生产效率的重要路径之一。例如,从单向铺粉到双向铺粉,生产效率得到提升。据华曙高科公众号2023年5月推 送,公司FS350M采用成熟的双向铺粉技术,在保证成品质量的前提下,缩短单层铺 粉时间,缩短打印间隔时间,比传统单向铺粉效率提高38%。具备丰富的扫描策略, 用户可自主选择高效率模式、智能模式、高质量模式,满足其个性化应用场景需求;据铂力特公众号2022年9月推送,针对粉末循环系统,铂力特已推出一套适配于批量 规模化生产的“辅机全家桶”,在设备准备与打印过程中,可使用BLT-GF300供粉 机在不影响打印进程的情况下随时进行粉末添加;在打印结束取件过程中,双工位 的清粉设计配合BLT-WL400物料机可实现快捷地粉末回收。
4. 在设备不变的情况下,软件如工艺规划软件升级,也是提高设备生产效率的重要 途径。例如,据铂力特公众号2023年2月新闻,铂力特对工艺规划软件BLT-Build Planer进 行了版本升级,进一步提高软件的剖分效率、打印效率以及使用便捷性,为用户提 供提效、降本的打印路径规划方案。在早期版本中,BLT-BP主要面向双光以下的设 备,新版本软件不再受设备激光器数量的限制,覆盖了铂力特面市的全部机型。该 新闻还提及,BLT-BP在升级之后,零件制造成本下降与设备激光器数量增长之间几 乎呈线性关系,设备激光器数量越多,节省的成本越大,越能为客户创造可观的利 润价值。
四、为什么需要用:工艺路径优势契合民用部分需求, 性能满足高端需求
(一)3D 打印在高附加值金属如钛合金领域,或更能契合其降本需求
成本是民用规模应用的前提,如批量更大的消费电子行业,新产品使用新材料,而 针对部分新材料,3D打印工艺优势或许更能契合其需求,本质还是综合降本。荣耀折叠屏率先应用钛合金3D打印,3D打印的量产应用渗透入消费电子领域。随着 3D打印技术的发展,成本逐步降低,其批量运用逐步由航空航天发展到民用产品。据荣耀官网《荣耀Magic V2正式发布,折叠屏手机进入毫米时代》,荣耀公司在2023 年7月12日推出的折叠屏荣耀Magic V2中,首次利用了3D打印技术进行批量生产。该手机的轴盖使用了钛合金3D打印工艺,与铝合金材质相比,宽度缩小了27%,强 度提升了150%,从而平衡了轻薄与可靠性,提高了折叠屏手机的竞争力,显示出增 材制造在消费电子行业的生产领域的突破性进展,有利于提高钛供应链的良率。
(1)3D打印为何契合荣耀钛合金零部件需求:结构复杂度高,3D打印的一体化成 形优势更突出,具备轻量化、一体化优势。与传统制造工艺相比,3D打印具有可成 形复杂结构、缩短产品实现周期、产品强度高重量轻、材料利用率高等特点,成本虽 然较高但近期下降趋势明显。3D打印技术的典型特点包括:可制造复杂几何结构的 部件、实现一体化生产、结构的复杂性不会带来额外的成本。设计师不再受到传统 制造工艺的约束,可以更自由地创造零件。相比于传统非一体化成形,减少组装等 成本。除了钛合金材料本身的特性能够带来轻量化及强度提升的优势之外,结合金 属3D打印技术,能通过轻量化、一体化及薄壁结构的设计优化,进一步降低零件的 重量及提高产品集成度。
(2)3D打印为何契合荣耀钛合金零部件需求:钛合金作为难变形金属,低热导率决 定其相比于此前的铝合金、不锈钢等材料,部分构件传统机加工方式的综合成本更 大。据微信公众号“钛之家”《钛合金难加工的四大原因》,钛合金材具有高强度、 高硬度和低密度材料特性,如钛合金Ti-6Al-4V (简称Ti-6-4)抗拉强度达900MPa, 硬度为250-375HB,密度4.42g/cm3,然而和铝合金材等相比,钛合金材属很难加工 金属材,主要表现在导热率低缩短刀具寿命的同时破坏零件完整性,产生加工硬化 现象、钛合金的弹性模量低等导致刀具磨损和刀片沟槽磨损。根据贝哲斯咨询2023 年3月发布的文章钛合金硬度高、加工难度大、良率低的特点,也使得其手机中框整 体良率约为30%-40%,远低于铝合金中框的80%。因此在工艺和设备的选择上也提 出了更高的要求,而3D打印能有效地解决钛合金材料成型问题。
(3)3D打印为何契合荣耀钛合金零部件需求:钛合金作为高附加值金属,相对于传 统铝合金、不锈钢等金属,3D打印可充分发挥其高原材料利用率的优势。传统减材 制造方法的原材料利用率较低,而3D打印技术是在需要的地方堆积材料,由于材料 是逐层叠加的,据铂力特招股说明书,在生产过程中较少产生材料的浪费,材料利 用率最高可超过95%。提高材料利用率,污染也随之减少,使得3D打印的生产更加 绿色环保,因此对于如钛合金等高附加值金属,客户可利用3D打印优势充分发挥其 高原材料利用率。
(二)轻量化、高强度、一体化,有望成为机器人结构件制造路径之一
增材制造提供了结构快速成型、材料结合应用的可能,助力了机器人减重,使机器 人拥有了更高的性能和灵活性。机器人轻量化主要通过几方面实现:
(1)结构优化。据《轻量化复合材料与3D打印技术在服务机器人上的应用与展望》 (陈宏伟等,工程研究-跨学科视野中的工程,2022年),传统的模具制造工艺繁琐, 对于一些复杂的模型零件制造难度大、时间周期长。相对地,3D打印可以实现复合 材料复杂结构的快速一体化成型,利用空心、异形的设计降低密度,同时灵活设置 材料打印路径,制造出达到需求的高强度零件。在机器人的生产制作上,增材制造 比传统制造更具优势。
(2)轻量化材料使用。据《机器人轻量化材料应用的研究进展》(于成涛等,新材 料产业,2019年),制造材料选择的前提是满足机器人的服役条件,所以其主体结 构材料需要满足强度高、弹性大、阻尼强的特征。传统工艺中运用的是高强度、低成 本、易制作的合金钢,牺牲了机器人的轻便度。而3D打印可以实现如钛合金、铝合 金等多种轻型材料的制作,保证主体条件的同时减轻机器人自重。3D打印可选择的 材料更多、适用范围更广,比起传统的合金钢制造更能匹配不同场景下机器人的需 求。
3D打印的独特设计和材料选择,契合机器人的部件制造。(1)传感减震弹性皮肤。据百家号援引3DScienceValley发布文章《工业机器人怎样与人安全、高效协作?3D 打印“皮肤”给出解决方案》,在工业生产过程中,为了避免工业制造机器人与人类 或其他机器人发生碰撞,3D打印厂商巴斯夫Forward AM与裕克施乐运用具有高减震 性和柔韧性的Ultrasint TPU01热塑性聚氨酯粉末进行增材制造,在机器人关节处覆 盖3D打印独有的晶格点阵结构皮肤,提高安全性和工作效率。(2)精密稳定的机械 关节。据百家号援引瑞云智造发布文章《金属3D打印机器人机械臂关节部》,机械 臂关节原来的传统铸造加工具有工艺复杂、周期长的弊端,瑞云智造使用材料铝合 金AlSi10Mg进行3D打印,降低了研发周期,也保证了机械关节的抗腐蚀性、热传导 性、承压性。3D打印技术不仅可以应用于机器人的整体减重,还可以根据原有条件 进行部件改进,在机器人的制造升级领域应用广泛,具有较为广阔的潜在应用前景。
(三)宝马增材制造布局初获成效,赋能设计验证,契合轻量化需求
1. 技术现状:宝马增材制造产业应用初获成效,车企积极布局3D打印技术
宝马公司较早入局3D打印,技术布局与产业应用初获成效。汽车领域是3D打印技术 应用最为广泛的领域之一,在全球的汽车制造商中,宝马汽车公司是当前应用3D打 印技术的代表。据微信公众号“世界先进制造技术论坛”《每年3D打印5万个零件, 宝马汽车宣布“增材制造工业化和数字化”项目成功》,早在30年前,宝马就开始 使用3D打印技术,近几年更是大幅增加投入,开发了M850i夜空特别版的3D打印刹 车卡钳和S58引擎缸盖的3D打印铸造砂芯,在宝马i8、宝马MINI等车型中也都增加 了3D打印的零件。为了实现3D打印的批量生产,宝马与2019年3月启动了“增材制 造工业化和数字化”(IDAM)项目。该项目由德国教育和研究联合部门资助,宝马 公司牵头,吉凯恩、亚琛工业大学、弗朗霍夫激光技术研究所等12家企业和研究机 构共同参与推动,力图引领3D打印技术在汽车批量生产中的整合。2022年5月,宝 马宣布该项目已经取得成功,项目共建成两条数字化的汽车零件3D打印生产线,一 条位于吉凯恩粉末冶金公司的波恩基地,另一条位于德国慕尼黑。这两条生产线独 立运行,每年能够生产约5万个零件。此外,2020年6月,宝马投资1500万欧元(约 1.1亿元人民币)建设的增材制造园区正式开张。园区内安装了EOS、SLM Solutions、 HP等至少8家3D打印厂商的不同技术类型的3D打印机,包括SLM、SLS、MJF、LSPc、 CLIP、FDM等前沿的3D打印技术,共计拥有超过50台工业聚合物和金属3D打印机。
2. 3D打印赋能汽车设计验证与生产制造,契合汽车轻量化与新能源趋势。
(1)3D打印技术缩短汽车设计验证周期
3D打印技术在汽车造型设计领域可实现直接、精确与快速的汽车实体模型制造。据 《3D打印与汽车行业技术发展报告》(中国汽车工程学会等,北京理工大学出版社, 2017年)、《浅谈汽车油泥模型制作的特点和相关技术》(严虎等,时代汽车,2022 年)、《3D打印技术在汽车研发中的应用》(沈卫东等,汽车工程师,2016年), 汽车造型设计通常要经过图纸二维设计、使用软件把概念化的二维汽车造型变成精 确的数据和3D模型、利用相关材料制造汽车实体模型、进行造型与功能评审等流程, 3D打印技术在汽车造型设计领域主要应用于优化汽车实体模型制造。当前汽车实体 造型主要通过油泥模型展现,在油泥模型的制造中,除车身主体部分由油泥铣削完 成外,3D打印技术可大量应用于车身附件模型的制造,如格栅、Logo、门把手及光 亮饰条等零件,替代所需工艺复杂、制作耗时费力的油泥零件模型。同时,在造型设 计阶段,汽车造型更新变化快且需多方案对比展示,3D打印技术可直接、精确、快 速地对零件模型进行制造,在有效缩短模型制造周期同时能够充分展示造型细节。
3D打印早期又被称为“快速原型”技术,在零部件原型试制生产领域应用广泛。据 《3D打印与汽车行业技术发展报告》(中国汽车工程学会等,北京理工大学出版社, 2017年),在汽车零部件原型试制生产过程中,制造商对试验与测试的零部件产品 原型数量要求不高,但对制造时间缩短与制造成本降低的要求较高,同时试制生产 阶段零部件往往需要在测试评估后多次进行设计更新与迭代,直到获得在设计与性 能方面合格达标的产品。3D打印很好地满足了制造商低成本少量制造需求,在获得 新的设计模型后无需经过重复开模等流程即可直接快速打印出新的零部件原型,缩 短从产品测试评估到产品改进迭代周期。据《3D打印在汽车制造中的应用》(崔厚 学,世界制造技术与装备市场,2017年)、《浅谈3D打印技术在汽车领域中的应用》 (李靖,内燃机与配件,2018年),美国Stratasys公司为宾利定制了3D打印汽车轮 胎原型,轮胎与轮毂一次性制造完成,与原车轮胎大小相同,制造时间仅为188h 28min,同时为宾利制造了具有支撑结构的3D打印车垫原型,制造时间仅为11h 49min;该公司还利用3D打印技术为奥迪生产车尾灯灯罩原型,将制作周期缩短50%。据Formlabs,在3D打印技术加持下,福特汽车设计师不再需要提前几周提出原型产 品生产需求,仅需在其技术中心利用3D打印技术即可快速制作设计原型,并能够在 短短几个小时内迭代多个设计,例如在制作福特Puma背面字母的原型时,设计师通 过3D打印出的原型观察字体线条和阴影在不同照明条件下的显示效果,并对设计快 速进行改进。
(2)3D打印技术可应用于各类汽车零部件的直接与间接生产
汽车主要由车身、电子辅助部件、内饰和动力系统四个部分构成,3D打印技术能够 提供各部分零部件的直接生产能力。据《3D打印技术在汽车试制中的应用》(周伟 赵等,企业科技与发展,2022年)、《3D打印技术在汽车行业中的应用与发展趋势》 (李金华等,汽车文摘,2018年),3D直接打印技术具有快速成型与成本节约特性, 同时可以用更大的自由度来实现设计的想法,能生产高度定制的部件,尤其是针对 那些经过拓扑优化的轻量化结构及高强度复杂结构零件,更能突显其技术优势。大 型车企多已在部分零部件领域应用3D打印技术,在车身部件方面,宝马为i8 Roadster车型定制3D打印的窗户导轨(使用HP MJF技术)和顶棚支架(使用金属 PBF技术),电动汽车公司Local Motors已经成功3D打印了整个汽车车身。在电子辅 助部件方面,3D打印部件生产公司Slant3D已经证明了3D打印在生产定制电子部件 时无需开模具,特定场景下具备一定成本效益。在内饰部件方面,2018年通用汽车 和Autodesk利用创成式设计开发了3D打印的座椅支架,该座椅支架由不锈钢材料打 印而成,从8个零件简化为1个零件,重量减轻了40%;HP使用MJF技术生产了具有 复杂晶格结构的3D打印汽车座椅;豪华汽车品牌保时捷于2020年也为旗下跑车设计 了3D打印的座椅。在动力部件方面,保时捷和SLM Solutions公司合作,利用3D打 印技术为其电驱动装置制造外壳;布加迪公司使用3D打印技术制造了部分汽车底盘 部件,包括革命性使用钛合金材料3D打印制动卡钳等。
除直接生产汽车用零部件之外,3D打印还被应用于零部件模具、工装夹具等生产, 间接为汽车制造、工装等流程赋能。据《3D打印技术在汽车行业的应用》(范武等, 内燃机与配件,2023年)、《3D打印技术在汽车行业的应用》(纵荣荣,汽车实用 技术,2022年)、《3D打印技术在汽车行业中的应用与发展趋势》(李金华等,汽 车文摘,2018年),在零部件模具制造方面,部分汽车零部件的生产须通过模具来 制造,而当前汽车零部件外形和结构日趋复杂,增加了相应模具的研制和生产难度, 传统工艺可能难以实现。以轮胎花纹的生产为例,轮胎花纹是重要而又复杂多变的 轮胎加工制造难点,其加工的精密程度直接影响到轮胎的精度和质量,甚至是轮胎 的安全、驾驶的舒适度等等。轮胎花纹具有弧度多、角度多的特点,结构往往呈现出 空间三维扭曲,采用传统的加工手段难以精准完成。为解决这一难题,米其林与法 孚合作,通过金属3D打印设备进行米其林轮胎模具的研发与制造,突破了传统铸造 与机加工技术难以实现的复杂纹理制造。在工装夹具制造方面,据《3D打印与汽车 行业技术发展报告》(中国汽车工程学会等,北京理工大学出版社,2017年)汽车 制造中会用到各种刀具、夹具等工装,其中很多工装属于小批量定制化产品,3D打 印能够低成本、短周期生产小批量定制化产品的优势与工装产品的生产模式十分契 合。以沃尔沃卡车为例,其位于法国里昂的发动机厂正是使用3D打印机来快速制造 工装产品,自引进3D打印技术以来,该工厂已打印了超过30种不同的工装供生产线 上的工人使用,包括耐用、轻巧的钳子、夹具、支架,以及符合人体工程学设计的刀 柄。3D打印团队在收到需求的几个小时内即可简单地改变设计规范并将夹具打印出 来,实现工装需求的快速响应。
(3)3D打印技术在汽车轻量化与新能源汽车领域亦具备较大应用潜力
3D打印技术能够应用轻质材料、具备复杂结构打印能力,契合轻量化实现路径。据 《3D打印与汽车行业技术发展报告》(中国汽车工程学会等,北京理工大学出版社, 2017年),出于环境保护和节约能源的需求,汽车轻量化已经成为全球汽车制造技 术发展的潮流。汽车轻量化指在保证汽车的强度和安全性能的前提下,尽可能地降 低汽车的整备质量,从而提高汽车的动力性,减少燃料消耗,降低排气污染。实验证 明,若汽车整车减重10%,燃油效率可提高6%-8%;汽车整车质量每减少100kg,每 百公里油耗可降低0.3-0.6L。3D打印技术一方面能够使用诸如碳纤维增强复合材料 等轻质材料,另一方面其制造工艺能够实现复杂结构零部件的制造以达到汽车小型 轻量化的要求。例如丰田汽车联合比利时的软件与3D打印服务商Materialise公司, 从拓扑优化和3D打印技术入手,共同设计了一款轻量化的3D打印汽车座椅,该座椅 实现了大量的材料节约,较上一代设计轻了18kg,减重高达72%,座椅中复杂的镂 空结构通过传统制造工艺会面临成本过高甚至是无法制造出来的问题,3D打印技术 在未来的轻量化设计应用中具备较大潜力。
3D打印技术在新能源汽车领域应用潜力广阔。据《3D打印在新能源汽车制造领域的 应用与发展趋势》(王晓燕等,金属加工(热加工) ,2022年),世界上的电动机 研发团队已将大量精力转移到将3D打印系统集成于电动机生产周期中,以实施更强 大、更高效地拓扑优化下一代电动机。预测未来几年内,原型拓扑优化电动机组件 的3D打印将急剧增加,最有可能集中在3D打印电动机绕组、热交换器和同步转子上。在车企中,保时捷与GKN合作推进Connactive项目,其聚焦点是新材料与新设计的 结合;福特携手亚琛工业大学开发灵活而可持续的3D打印电动机零部件,其聚焦点 在于铜金属。据Ford官网,2021年福特、蒂森克虏伯、亚琛工业大学和Engiro组成 的行业联盟启动了下一代电动机的研究项目,旨在开发灵活可持续的生产工艺,3D 打印将在生产线中发挥重要作用。
(四)高端装备领域需求高,3D 打印或成为兼顾性能与成本的较优选择
据《3D打印技术在高超声速技术领域的应用研究》(林旭斌,战术导弹技术,2018 年),“相对于传统的航空航天飞行器,高超声速飞行器在临近空间/大气层内长时 间以超过马赫数5的高速持续飞行,工作环境恶劣,尤其在弹身/机身外形局部的气动 驻点、激波附着点,以及采用吸气式动力形势的发动机进气道、燃烧室等部位,热环 境尤其严酷,对零组件材料的耐高温性能、结构的力学性能等有着很高要求,同时 对零组件空间外形、自身重量等也有着苛刻要求。3D打印技术在高超声速技术相关 领域的应用日渐增多,已经成为解决高超声速飞行器制造瓶颈的关键所在。在传统 制造技术无法满足要求时,3D打印技术以其能够快速制备具有高材料性能、异形结 构、整体特性的零部件特点,在高超声速飞行器相关领域得到了愈发广泛的应用, 甚至成为解决一些高超声速飞行器特殊零部件瓶颈的唯一选择。”
五、投资分析
如何理解钛合金3D打印在荣耀Magic V2的应用:在新推出折叠屏手机荣耀Magic V2 中,首次利用了3D打印技术进行批量生产,该手机的铰链使用钛合金3D打印工艺。我们认为,3D打印在消费电子领域首次量产应用的原因,系在实现轻量化、一体化、 高强度的同时,3D 打印可更好地解决合金传统加工难度大和材料利用率低等问题。①3D打印具有一体化成型优势,利于加快生产周期。②低热导率的钛合金数控加工 成本高,3D打印减少机加工时。和铝合金材、不锈钢等相比,钛合金材属很难加工 金属材,主要表现在导热率低,缩短刀具寿命的同时破坏零件完整性,加工硬化现 象、弹性导致刀具磨损和刀片沟槽磨损。③在相对更贵的钛合金上,3D打印传统的 高原材料利用率优势更为突出。传统减材制造方法的原材料利用率较低,而3D打印技术是在需要的地方堆积材料,由于材料是逐层叠加的,据铂力特招股书,在生产 过程中较少不会产生材料的浪费,材料利用率可超过95%。
为什么开始用:我们认为,新工艺应用的背景,在于产品升级周期,牵引对新材料、 新结构的要求。民用伴随产品升级周期,新材料在高端产品领域渗透率逐步提升, 如去年苹果在高端手表上使用钛合金中框。航空航天等高端装备领域,在客户对于 装备性能升级需求下,复杂度提升,3D打印等新工艺成为传统工艺互补选择。
为什么可以用:性能领先,降成本、增效率是规模应用前提。产品升级周期如果是让 金属3D打印“开始用”,那么成本降低与效率提升,则是实现“可以用”的前提。成本降低路径方面,原材料价格、设备价格下降、核心零部件国产化等,是提高行业 渗透率的关键,并且正在发生。效率提升方面,激光器数量增加、激光扫描系统速率 提高、铺粉方式升级、工艺规划软件升级等,均是提高金属3D打印设备生产效率的 重要路径。
为什么需要用:成本是民用规模应用的前提,如批量更大的消费电子行业,新产品 使用新材料,而针对部分新材料如钛合金,3D打印工艺优势或许更能契合其需求, 本质还是降本。并且,结合现有案例,我们看好3D打印行业基于降本增效路径,有 望在多行业实现规模应用。例如,3D打印提供了结构快速成型、材料结合应用的可 能,助力机器人减重,使其拥有更高性能和灵活性;宝马增材制造产业应用初获成 效,3D打印赋能汽车设计验证与生产制造,契合汽车轻量化等趋势;高端装备领域 需求高,3D打印或成为兼顾性能与成本的较优选择。
(本文仅供参考,不代表我们的任何投资建议。如需使用相关信息,请参阅报告原文。)
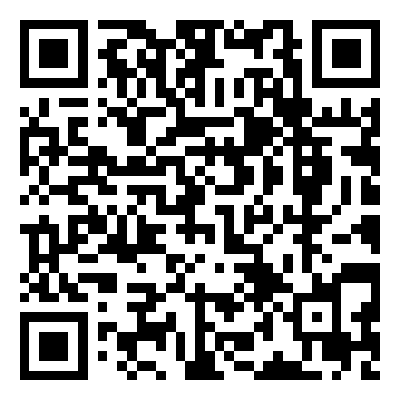
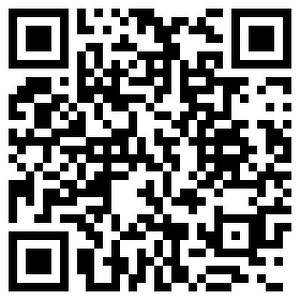
VIP课程推荐
APP专享直播
热门推荐
收起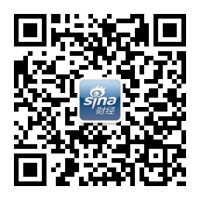
24小时滚动播报最新的财经资讯和视频,更多粉丝福利扫描二维码关注(sinafinance)