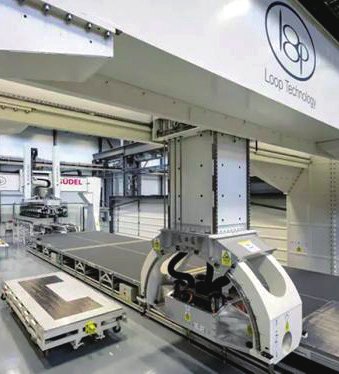
超高速复合沉积系统(UHRCD)演示器。
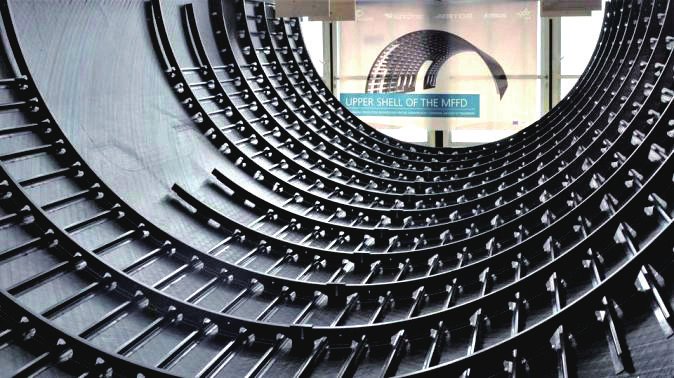
空客“多功能机身验证件”。
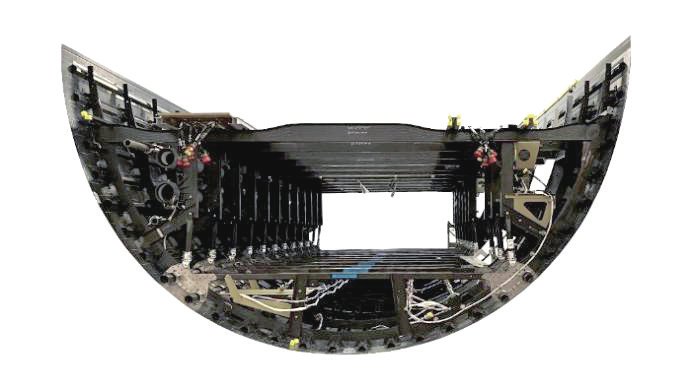
热固性复合材料部件。
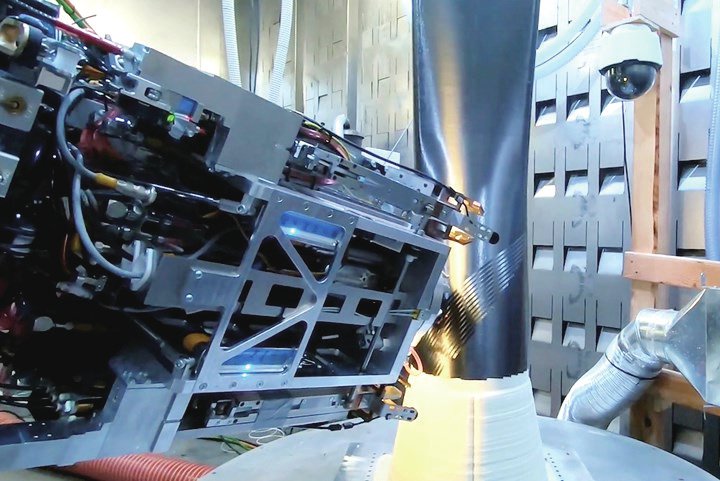
诺格公司正在寻求,可扩展复合机器人增材制造。
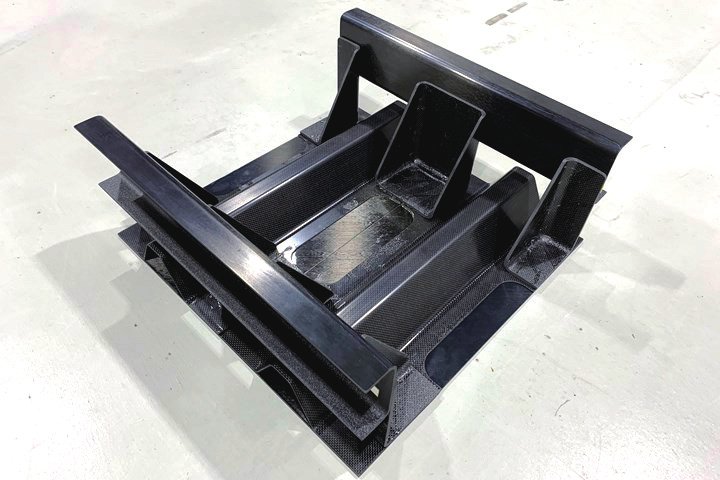
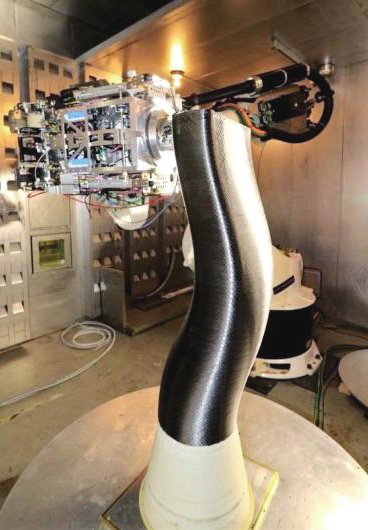
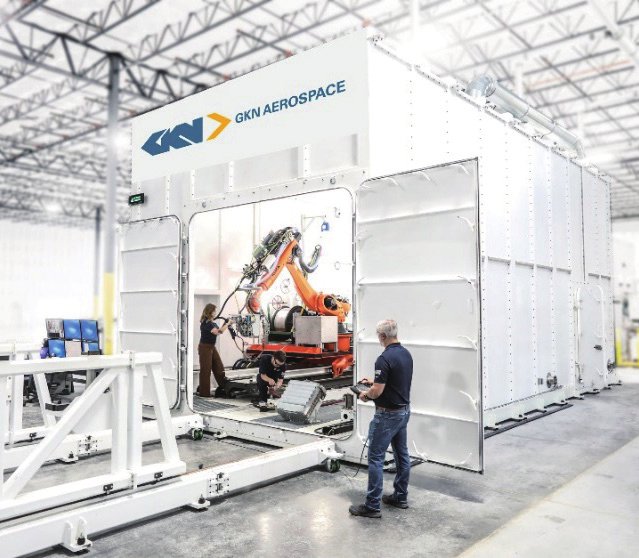
激光定向能量沉积增材制造单元。

洛马公司投资先进机器人钣金成形技术。
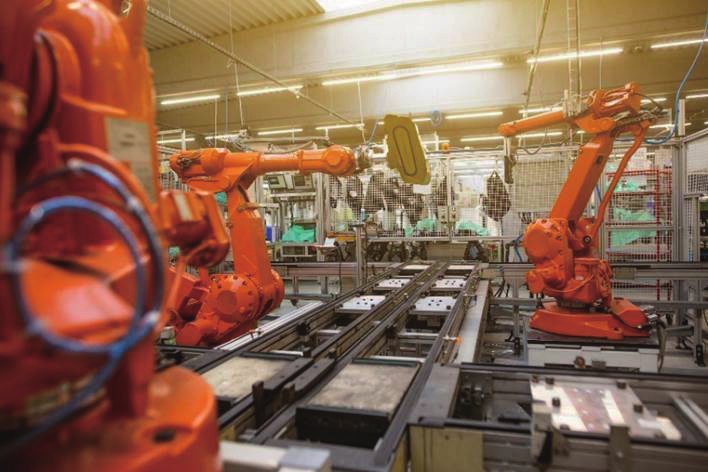
洛马公司开发用于机身制造的自主认知机器人。
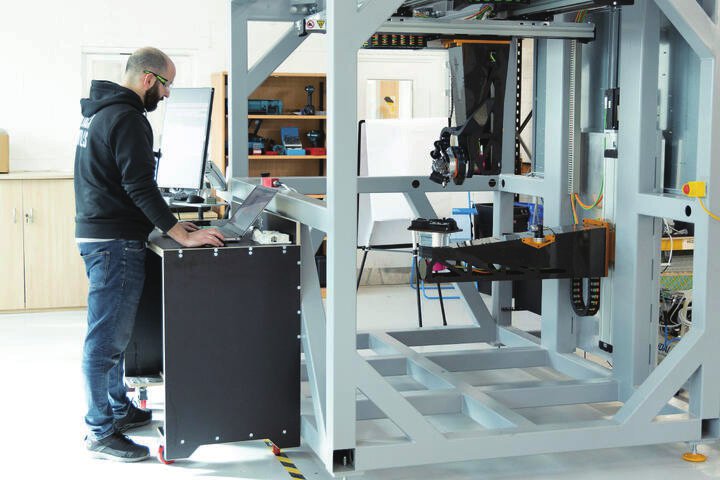
英国先进制造中心开发机器人布线。

美军使用移动式、自主冷喷涂系统进行H-1直升机维修。阴鹏艳 等 2023年,美欧航空工业强国大力推动航空制造技术创新发展。复合材料成形、增材制造、金属加工、装配与维修等领域的数字化、智能化转型进程加速,高精度、高效率特征愈发突出,先进技术不断涌现,有力推动了航空产品高质量研制生产和保障。 作者以技术重大性、前沿突破性、推广应用性、绿色环保性等为参考依据,经系统梳理和专家评议,遴选出航空制造技术领域十大进展(排序不分先后),供业内参考。英国采用超高速沉积技术实现17米长机翼蒙皮预制件成形 11月,英国国家复合材料中心利用其开发的全球首个复合材料超高速自动沉积系统,制造并交付了17米长的全尺寸机翼原型。该系统包含两座高7米、宽13米的龙门架,龙门架可沿26米的轨道延伸,能够自动定位末端执行器、切割干纤维材料并沉积到复杂双曲率模具上,整个过程无需人工干预。在开发测试中,该系统能够提供超过350千克/时的干纤维沉积率,远超当前大型航空结构纤维自动铺放量50千克/时的水平。机翼原型自动化成形涉及大约170层单独的干纤维铺层,在生产过程中最大沉积速率接近0.8米/秒,完成一层17米的铺层只需大约30秒。此外,团队还实现了世界上首次大规模、高度复杂的一体化结构树脂灌注。 【述析】面对未来广阔的民机市场,“大(部件)且快(成形)”是下一代大飞机的发展焦点和竞争高地,高速、低成本航空复合材料制造技术已成为核心关切。该机翼原型为空客“明日之翼”项目的研究成果,“明日之翼”项目于2016年启动,旨在通过改进制造工艺、开发自动化程度更高的新装配方法等完成机翼集成,从而提高未来单通道飞机产量。英国国家复合材料中心牵头的系列研究成果实现了纤维沉积速率提升6倍,并探索了高度复杂的一体化结构树脂灌注,在复合材料主结构高速成形和非热压罐制造领域取得了重大突破,有望大幅释放复合材料结构制造产能,持续提升未来航空产品生产效率。 欧盟“多功能机身验证件”项目交付热塑性上、下机身段 2月,在空客公司牵头的“多功能机身验证件”项目下,吉凯恩福克团队完成了热塑性下机身段的制造,该部件尺寸8米×4米,由400多个热塑性纤维增强零件、数千个焊点和数百米的连续焊缝组成,是世界上最大的热塑性复合材料部件之一;7月,德国航空航天中心团队完成了热塑性上机身段的制造,该部件采用激光原位加热辅助丝束铺放、机器人连续超声焊和协作机器人电阻焊技术,这些技术将使完整的机身段总重减少1吨(10%),月产量达到至少60架(最多100架),并且机身经常性总成本减少100万欧元(20%)。 【述析】欧盟通过“框架计划”和“洁净天空”系列计划等,为高效、低碳的航空制造技术提供了持久、稳定的预研支持,是下一代大飞机研发的重要基础。作为“洁净天空2”下的研究项目,“多功能机身验证件”的成果是欧盟实施热塑性复合材料航空主结构发展路线图的关键里程碑。项目将高强轻质、可回收热塑性复合材料作为实现未来可持续航空的抓手,成功制造出了世界上最大的热塑性部件单件,在线检测、机器人焊接等先进技术的成功应用使得庞大的机身结构高效成形并充分减重,可以说是热塑性复合材料进军航空大型结构件应用的标杆实践。 东丽公司开发可用于热固性复合材料的高速热焊接技术 2月,日本东丽工业公司开发了一种可以高速热焊接碳纤维增强热固性复合材料部件的技术,该技术通过在部件表面形成热焊接层,通过瞬间加热表面以实现部件粘合,无需粘合剂粘合或螺栓紧固。东丽公司使用热焊接的热固性复合材料部件组装了一个模拟飞机基本结构的演示验证机,验证了其力学性能和连接强度与目前机型的共固化复合材料结构相当。该技术预期在2030年后实现机身商业化应用,有望实现与铝合金机身相当或超过铝合金机身的生产速度,同时还可减少复合材料机身寿命周期内的碳排放并减轻重量。 【述析】复合材料结构的焊接连接是减少紧固重量、提高成形速度和可靠性的有效手段,这一连接手段过去只能在热塑性复材结构上实现。东丽公司开发的高速热焊接技术另辟蹊径,通过在热固性复合材料的表面形成热焊接层并加热实现了结构粘合,且性能和强度符合要求,同时避免了整体更换和鉴定热塑性材料的复杂环节,是一项具有快速高效、绿色环保和推广应用潜力的突破性创新。诺格公司开发应用于高超声速武器的机器人增材制造系统 1月,诺格公司使用增材制造技术开发了“超声速吸气式武器概念”项目的高超声速燃烧冲压发动机,并与电冲击公司一同完善可扩展碳-碳复合材料机器人增材制造系统,以实现航空级集成复合材料结构的无模具快速制造。利用基于增材制造的快速成形工艺,该系统能够制造在暴露于极端温度时不会腐蚀、熔化或改变形状的碳-碳耐高温结构,成本和进度缩减可高达50%。项目团队制造了一个以圆形横截面开始、S形弯曲并以矩形横截面结束的零件,此类复杂几何形状的零件过去只能手工制作,且可能需要长达一年的时间,利用该增材制造系统则可以在几周内完成。 【述析】耐高温复杂结构的快速试制与生产是支撑高超声速武器快速发展的重要环节。该成果体现了诺格公司在高超声速武器耐高温碳-碳结构制造中对复合材料增材制造技术应用的领先探索,电冲击公司给出了基于六轴机器人的可扩展连续纤维增材制造解决方案,提升了成形过程的灵活性,例如可定制每层内的纤维取向以提供最佳的强度和刚度分布。从初步成效看,增材制造技术在快速实现设计意图、按需整体生成复杂零件方面具有显著优势,更重要的是能够打破设计壁垒,为高超声速武器结构的“天马行空”创新研制提供了条件保障。吉凯恩公司推出全球最大激光定向能量沉积增材制造单元 6月,吉凯恩航宇公司推出目前世界上最大的Cell 3激光定向能量沉积增材制造单元,是突破大尺寸钛合金飞机结构增材制造界限的新一代设备。该制造单元配备20千瓦激光器,具有多达10个运动轴,最大构建尺寸为5.6米×2.5米,采用双面或旋转沉积方式,能够使用线材激光金属沉积工艺制造5米长的钛合金部件。该制造单元不仅可以满足对安全把控极其严苛的航空结构所需尺寸要求,而且可以显著加快生产速度,缩短交付时间。 【述析】当前,金属增材制造的沉积效率和尺寸限制制约了其规模化应用,高速率、大幅面增材制造成为重点攻关方向。与其他金属沉积工艺相比,线材激光金属沉积工艺具有可调节激光能量和金属丝进给速率等优点,进而可以有效控制沉积速率和产品性能。2022年,吉凯恩公司利用Cell 2单元研制出了尺寸达2.5米级的钛金属构件,一度成为行业里程碑。在此基础上,吉凯恩公司持续发力,新的Cell 3单元将最大钛合金构件尺寸突破至5米级,且成形方式更灵活、效率更高。随着对工艺改进、建模与仿真、无损评估方法、现场监测等的持续研究,该技术有望在更多种类、更大尺寸的高价值难加工飞机和发动机金属结构上发挥应用优势。美英开发下一代可消耗无人机集群批量增材制造解决方案 6月,美国风暴实验室公司与英国绿色推进公司宣布将合作开发全增材制造的无人机机身和发动机批量生产解决方案。风暴实验室公司拥有独特的互联增材制造和可互换机身组件技术,支持无人机搭载通用平台和基于人工智能的飞行计算机执行各种任务集;绿色推进公司专注于研发电推进系统,其专有的增材制造方法可支持快速修改产品以适应不同的飞机、任务和要求。通过将两家公司的技术集成到模块化无人机系统中,有望实现增材制造无人机机身和发动机的100%快速低成本大规模增材生产,并支持多种有效载荷,确保能够在最具挑战性的环境中执行任务。 【述析】聚焦实战化能力,各国正在加速无人集群作战系统全面融入作战体系,对低成本高效批产的需求剧增。该项合作体现了低成本大规模生产无人机的关键要素,即模块化、智能化、增材制造。增材制造无模具整体化成形的优势能够确保满足无人系统的轻量化要求,并为高效制造功能结构提供可能。此外,天生具有数字化属性的增材制造技术,能够在批量生产过程中与自动化、网络化技术结合形成分布式生产能力,进一步提升对生产过程的高效洞察与柔性管控,是实现低成本、可消耗无人系统快速生产的优质选择。洛马公司投资先进机器人钣金成形技术 1月,洛马公司风投部门向美国Machina实验室公司投资,支持其开发无模机器人板材成形工艺,替代依赖定制模具的传统钣金成形方法,以大幅缩短交付周期并降低制造成本。该方案使用双机械臂成形金属板材,无需设计制造模具,灵活性强,可将零件生产周期从50周缩短到数小时,节省成本达百万美元。制造平台通过软件驱动,结合了机器人和人工智能技术,可将CAD文件转换为机器人运行路径,并利用大量人工智能驱动的传感器收集数据,逐步使板材成形为最终零件。系统在零件成形过程中会创建包含所有制造过程信息的数字孪生,以确保工艺特性和零件鉴定信息的准确性。 【述析】除复材成形、增材制造和装配等应用外,先进信息技术和自动化技术也在为劳动密集型的传统制造技术带来转型升级契机。初创公司Machina实验室正在探索使用人工智能和机器人技术从根本上改变金属板材成型行业,其双7轴机器人协作的钣金成形解决方案简化了切割和弯曲金属板的过程,人工智能则能够进一步赋能路径优化、缺陷识别和系统预测性维护等,优于依赖定制模具或冲模的传统成型方法。洛马公司对该技术的青睐,凸显了航空装备制造商对高精度、短周期、柔性制造技术的密切关注,也是其在先进制造领域实施数字化转型战略的重要投资。洛马公司开发用于机身制造的自主认知机器人 6月,洛马公司将其工业机器人与Xaba公司专有的物理信息深度人工神经网络模型xCognition集成,测试了xCognition的“合成大脑”如何赋予机器人更强大的智能功能,以及对其机体和即将执行的任务的理解,同时确保达到所需的质量和误差要求。测试包括两个阶段,一是评估机器人在使用和不使用xCognition系统时保持准确和一致的轨迹定位的性能;二是在具有指定位置公差的铝制试验板上进行一组钻孔试验。结果表明,xCognition将机器人的准确性和一致性提高了10倍,使得工业机器人能够高效执行当前必须更昂贵、不灵活的数控机床完成的关键制造操作。 【述析】ChatGPT、Sora等工具的横空出世切实展现了人工智能的巨大能量,工业制造中的人工智能应用也在不断扩展,典型代表之一的初创公司Xaba正专注于使用工业人工智能将任意工业机器人变身“生成式机器人”,使其在生成程序和执行焊接、钻孔、组装和增材制造等任务时变得更加智能和自主。这一解决方案颠覆了当前的自动化制造业务模式,使传统工业机器人和协作机器人能够实现成本更高的高精度机床的性能。可以想象下,未来的航空制造是否会是:操作员口述一个简单的需求指令,然后机器人总动员——自主生成零部件并完成整架飞机的完美建造?英国先进制造中心开发机器人布线与缺陷检测解决方案 5月,英国谢菲尔德大学先进制造研究中心与Q5D技术机器人公司合作,开发了可计算工件的位置和旋转角度以及实时嵌入式布线缺陷检测解决方案,支持5轴机器人自动完成复杂飞机部件布线和质量检测。该解决方案利用基于立体视觉技术的深度相机和Halcon计算机视觉开发工具,构建点云表面模型,准确计算工件位置和旋转角度,并将缺陷检测算法与二维高分辨率灰度图像结合,检测电线断裂、电线压碎、电线绝缘层剥落等质量问题。经验证,实现了工件位置计算精度在0.5毫米,旋转角度误差小于0.6度,不同角度工件的裸线缺陷检出率达到100%。 【述析】飞机中的复杂管路和长达数百公里的电线安装,是智能视觉系统发挥作用的主战场。该研究成果是Q5D公司牵头的名为LiveWire的研发项目的一部分,该项目受“创新英国”机构资助,旨在实现航空工业线束生产和检测的自动化。经验证,机器人平台与视觉系统的集成为布线检测带来了更高的可靠性和灵活性,未来,这一技术概念有望嵌入任意机器人作业系统,将人从大量繁琐低效的肉眼检测和离线检测工作中解放出来,助力工厂形成数字化、自动化的质量管控能力。美军使用移动式、自主冷喷涂系统进行H-1直升机维修 3月,美海军陆战队使用新型移动式、自主冷喷涂系统对H-1直升机的组合齿轮箱和滑管进行维修,以缩短飞机维修时间,降低成本。与传统维修方式相比,该系统的优势包括消除待维修零部件尺寸限制,提升飞机现场维修能力;无需拆卸和搬运零部件,可维修磨损零部件并重新使用,节省维修时间和成本;可以通过编程自动运行或者由专业技术人员手动操作,操作更加灵活。该系统在各飞机平台均具有应用潜力,有望推广至整个海军航空维修部门。 【述析】快速维修保障是保持、恢复和提高作战部队战斗力的重要因素。面对依赖海外供应链导致的锻件交货期长等问题,美军换道将增材制造作为强化供应链韧性、快速抢修作战装备的重要抓手。冷喷涂技术通过将粉末以超声速冲击受损零件表面,能够在基体表面形成牢固附着的致密材料从而恢复零件尺寸。美陆海空三军均已利用冷喷涂技术开展高价值航空部件修复,并持续研究提升冷喷涂平台的可移动性、自主性,以期为维修基地和作战部队提供更快速、灵活便捷且低成本的再制造能力,提升作战装备经济性和战备完好性。
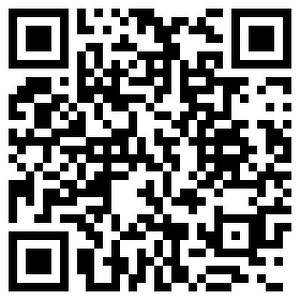
VIP课程推荐
APP专享直播
热门推荐
收起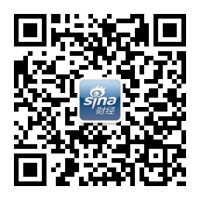
24小时滚动播报最新的财经资讯和视频,更多粉丝福利扫描二维码关注(sinafinance)