转自:中国科技网
科技日报记者 张晔
近日,记者走进江苏苏州明志科技股份有限公司(以下简称“明志科技”)的铝合金热交换器智能生产车间,这里既没有烟尘,也没有工人繁忙的身影。
在智能车间的中控大屏上,实时显示着铝液温度、液面高度、废气温度等参数。工人只需轻触设备,一台台精密的铝合金热交换器就源源不断地从智能铸造流水线产出。
明志科技总经理邱壑告诉记者,这一批热交换器即将出口欧洲,用于冷凝式燃气壁挂炉,目前公司生产的铝合金热交换器已占据全球三分之一市场。
明志科技产品成功打入欧美高端市场,就是源于数字赋能。作为一家传统的铸造企业,明志科技2014年建立国内铸造行业首个智能制造示范车间,实施智能化改造、数字化转型以来,生产效率和质量明显提升,成为国内砂型铸造装备的领军企业。
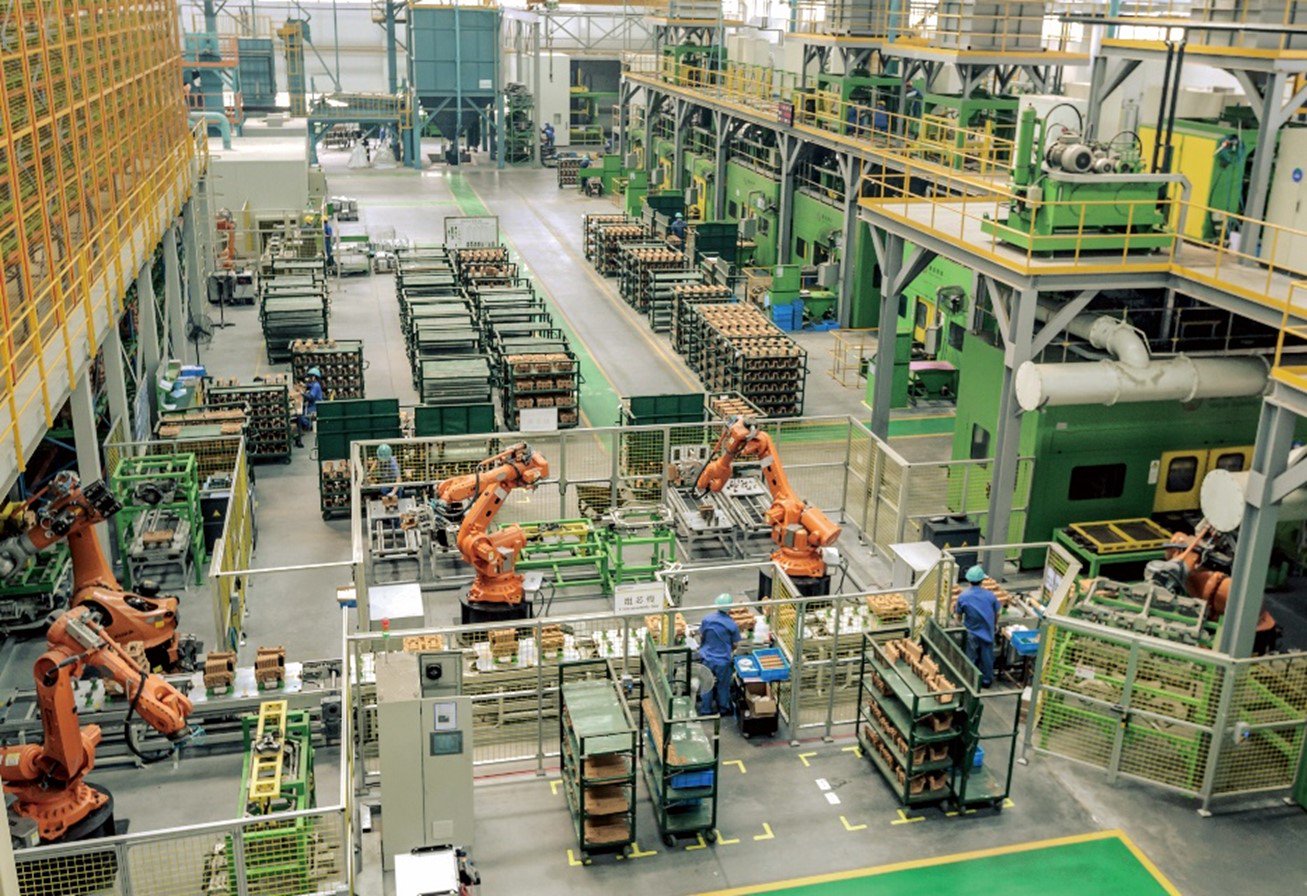
铸型先铸芯 “跟跑者”赶超“领头羊”
早在公元前1700多年,我国就掌握了青铜铸造的技术。进入工业革命后,铸造更是成为制造业的基础领域。
走进明志科技大楼,一眼就看到两个硕大的砂芯。
“这就是用制芯机制造出来的高铁列车整体摇枕及侧架砂芯。”邱壑告诉记者,铸造行业按工艺类别可分为砂型铸造、精密铸造、压铸等,其中砂型铸造是铸件生产的重要方式,钢、铁等大多数金属铸件都可以用砂型铸造的方式获得。
制芯机则是砂型铸造关键核心设备。在这一领域,从最初的“跟跑者”,到如今的赶超“领头羊”,明志科技仅用了20年。
“砂型铸造首先要用各类成型方式完成外形以及内芯的制作与装配成完整的铸型,然后把熔融的金属倒入铸型中,金属凝固后即可完成一个铸件的成型。”邱壑带着记者走进车间,一台3米多高的制芯机正在隆隆工作中,射芯机把砂子快速喷射进模具里,再通过催化剂固化砂子造型,射砂控制、砂芯固化、精密组芯……整套流程一气呵成。
过去,我国的铸造业从材料、工艺到理念等各方面都与世界先进水平有较大差距。为了追赶世界一流水平,明志科技与清华大学合作,开展制芯工艺原理研究,用高速摄影机拍摄射芯过程,搞清楚制芯气相-颗粒双相流射砂充填原理,确保砂芯的紧实度和强度以及一致性达到设计要求。同时,明志科技特地建设了一个铸造车间进行铸件生产,用实践检验新品指导研发。
阀体是火车刹车中枢控制系统,但生产复杂阀体的技术难度非常大,即便是在欧美国家,复杂阀体的废品率也接近50%。但是明志科技总工程师杨林龙坚信能攻下这个难关,他从提升原材料力学性能、采用精密组芯动态坐标系理论两方面入手,改进生产工艺,阀体的废品率降至个位数,从而产品顺利打入美国市场。
明志科技为德国一家采暖锅炉企业生产的热交换器,更是彻底改变了欧洲人对中国铸造业的印象,摘掉低技术含量的“帽子”。热交换器里管道密布,A4纸大小的砂芯像蜂窝板一样布满上千个孔洞,孔洞最小间距只有1.8毫米,这个订单欧洲不敢接,但明志科技仅用3个月就交付,如今,明志科技生产的铝合金热交换器已占据全球三分之一市场。
在完成追赶国际先进铸造装备技术的基础上,2016年,明志科技更以绿色智能为公司装备的发展方向,推出自主研发的MiCC300集成式智能制芯单元,并配置了运行大脑MiCL智能制芯控制系统,装备运行与工艺参数智能控制的完美融合,制芯质量可靠保证同时,制芯单元比传统设备降低能耗近50%,效率提升近30%,占地减少25%。目前已经进入全面推广阶段。
机器换人 让“苦力岗”变身“技术岗”
铸造长期以来一直以来都是苦、脏、累的代名词。但是明志科技的生产车间里则是另一幅景象,机器人上岗承担了繁重复杂的“体力劳动”,工人升岗成为智能系统的操作员。
盛夏时节,记者走进明志科技的铸造车间,这里没有漫天烟尘,也没有刺鼻气味,只有平整光洁的地面与为数不多的工人。
早在2003年成立之初,明志科技就率先将工业机器人用于企业的智能化改造,成为国内第一批尝试“机器人代人”的铸造企业。后来,企业陆续配置了50多台工业机器人,成为企业智能制造不可或缺的一环。
“工人已经告别了‘苦脏累’,机器人和智能设备承担了大部分重复机械的操作工作。”明志科技研发中心副经理陆高春告诉记者,铸造业工作强度大、工作环境差,经常面临“用工荒”难题。明志科技引入智能设备后,再也不为用工发愁。
机器人抓手是车间的“大力士”。砂芯制成后重量超过200公斤,搬运起来不仅费力,还很危险。过去,翻砂工作需要近10人来完成,而现在,这项工作只需一个人、一台机器就可以完成。
在现场,一位工人向记者演示了操作过程:提前给射芯机设定好工作时间,机械手臂按照设定好的程序自动运行,不出40秒,一块砂芯就稳稳地落在了记者的面前。
全自动系统也让铸造工人这个“苦力岗”变成了“技术岗”。“我们不再埋头干‘苦力’,而是转变为技术工人,不仅要对制造工艺了如指掌,还要会操作、保养智能设备,熟悉各项参数设置。”上述工人告诉记者。
记者了解到,明志科技智能铸造示范车间自动化程度高达90%以上。自车间投产以来,产品定制周期从7天减少到半天、员工人数减少70%、人均生产效率提升221%、产品废品率下降70%。
智改数转 让“老师傅”服了“大数据”
一个“傻大粗”铸造件的背后,有着怎样的高新科技?明志科技用“数字化”创新之路不断探寻着答案。
传统的铸造车间总体分为制芯、浇注、加工三大工段。不同工序操作复杂,许多环节对老师傅们的手艺格外依赖。这种以人工为主的方式,不仅效率低,而且在制造过程人为干预,为产品质量带来不稳定因素。
在传统的制造过程中“老师傅的手艺就是标准”,而明志科技通过信息数字化技术,将过去由“老师傅”把关的环节变成了一道道检测点,用大数据代替人为把关。
在明志科技工业互联网平台上,各类数据一目了然,平台可对生产进度、设备状态、加工制作等参数进行精准分析。“车间现场所有的制芯设备上都带有一个明志科技开发的MES(制造执行系统)系统,设备所有的运行数据和生产数据都可以通过智能化平台传输给管理人员,为管理和决策提供了可靠的依据。”陆高春介绍。
截至目前,明志科技铸造车间采用智能化设备79台套,智能化率84%,联网设备40台(套),设备联网率42.55%。通过设备、物料、人之间的数据互联,构建了生产物料精准配送、生产过程实时管控、生产信息跟踪追溯、能源消耗智能管控、安全环保智能管控、车间内外联动协同体系,实现了企业信息化、工厂自动化的深度融合,在降低人员操作要求的同时,大大提升生产效率及产品质量。
“我们的智能铸造车间总投资约1.5亿元,这对我们来说是一笔不菲的支出,好在各级工信部门都给予了很大的资金支持,也授予了我们很多荣誉,坚定了明志科技‘智改数转’的决心。”总经办总助张红亮说道。
作为国民经济的基础产业,铸造为汽车、工程机械、轨道交通、机械装备、热能工程、航空航天等下游产业提供铸件产品。2022年,专注砂型铸造的明志科技成为国家专精特新“小巨人”企业,并入选江苏省智能制造示范车间,也是苏州市高端装备制造和数字化改造标杆企业。
“现在,我们不仅出售高端智能制芯设备,还会输出智能产线的项目策划和工艺,帮助更多铸造企业实现‘智改数转’,创造更多价值。”陆高春表示,明志科技将继续聚焦数字化创新,不断进行智能产线迭代升级,公司正在研制应用新一代MES系统,并启动建设一个新的智能铸造产线。
(受访者供图)
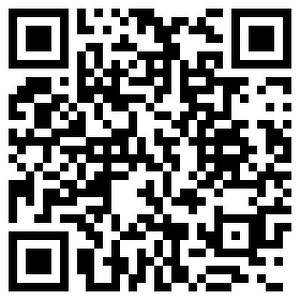
VIP课程推荐
APP专享直播
热门推荐
收起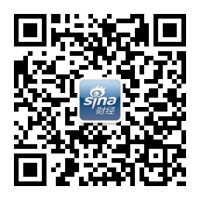
24小时滚动播报最新的财经资讯和视频,更多粉丝福利扫描二维码关注(sinafinance)