近年来,作为重要工业基地的重庆,力促5G、大数据、工业互联网等新一代信息技术赋能传统工业,企业纷纷部署应用云服务等数字化技术,加快实施数字化转型。从行业龙头企业,到海量的中小企业;从传统钢铁、化工等领域,到前沿通信技术行业……如今,山城工业开启“数字变身”,智能制造持续为工业经济赋能助力。
在不少人印象中,钢铁厂高温、高危,且产能落后。不过,随着钢铁企业数字化转型,上述刻板印象正悄然褪去。在重庆钢铁股份有限公司双高棒产线生产车间,昔日人头攒动、环境脏乱的工作场景不复再现,取而代之的是“一条生产线、一个操作室”远程集中控制。只见高清屏幕不停地跳动着实时生产数据,工作人员不仅可远程掌握生产情况,还能利用测温取样机器人等替代人工完成有毒有害、高风险、重复性工作。
重庆钢铁相关负责人介绍,围绕推进数字化转型,近年来重钢上线了经营管控智慧平台系统,这一“产业大脑”融合了经营管理、制造运行等业务需求,实现了运行状态实时监测等功能。
有了“产业大脑”,还要有“智能身躯”。重庆钢铁还围绕多个生产经营环节,积极接入、覆盖多样的应用场景,部署应用机器人等先进设备及技术,力促数字化技术嵌入生产全链条。迄今为止,已累计上线运行30多个智能制造项目,每年带来直接经济效益1800余万元。
重庆钢铁产成品物流系统日前正式上线,系统通过产成品信息自动录入、在制品在线流转等智能化功能,彻底改变了过去存放依赖人力、人工定位位置、产品交叉叠放等效率低下的情况。引入“5G+工业互联网”,煤料管理也实现了智能化。在智能监测系统上,煤仓内库存、物料堆放高度等实时数据一目了然,煤仓达到满仓高度后,系统便自动控制传送带停机,无需人工操作,工人从脏乱的环境中解脱出来。
像重庆钢铁一样,重庆一大批老牌工业企业加速迈向数字化,依托“数据流”加快驱动企业高质量发展。在位于璧山区的重庆青山工业有限责任公司,汽车变速器装配生产线上一派忙碌景象,智能小车穿梭运输物料,工业机器人挥动手臂协同作业,一台台变速器有序生产下线。同一时间,隐形的“数据流”正持续流转,成为贯通企业生产经营的“血液流”。
“我们围绕企业运营流程,打造数字经营能力,构建了运营全景图,着力从技术上打通不同系统间的‘数据孤岛’,管理模式从经验驱动向数据驱动转变。”该公司副总经理潘凯说,公司实时采集生产线153台设备、超1.2万个设备传感器的各类数据,每天产生的数据量超40G;以数据流为牵引,实现对生产管理、质量管理和设备预测性维护等功能的深度分析,生产效率提升30%;还运用智能算法代替传统人工操作,实现智能图形化排产、在线视觉防错等,显著提高工厂管理效率。
据介绍,作为变速器行业的龙头企业,青山工业公司还力促供应链协同,通过打破上下游数据传递壁垒,建立数据共享机制,并联合物流打造生态圈产业链,有力拉动140多家供应链企业迈向“数字化”。“以前与供应商对接主要靠表格表单,现在技术图纸可直接传输到供应商的生产线上,效率大大提升。”潘凯说。
数字化转型的持续推进,离不开新一代信息技术等的“硬核”支撑。近年来,看准重庆雄厚的工业基础和巨大的数字化转型需求,众多工业互联网企业纷纷在渝落子,一批本土工业互联网企业也快速兴起。迄今已有15家国家级跨行业跨领域工业互联网平台在渝布局,中移物联网、忽米网等本地平台也已向众多制造业企业渗透。
记者了解到,在政企协同发力下,近年来重庆已累计推动11.3万家企业“上云上平台”,累计实施4800余个智能化改造项目,示范项目生产效率提升58.9%。锚定工业领域数字化转型,今年重庆计划再建10个智能工厂、100个数字化车间,为更多企业插上“数字化翅膀”。
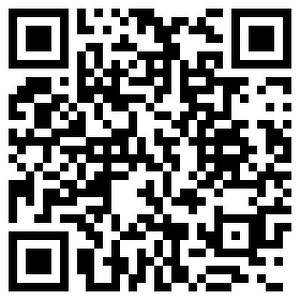
VIP课程推荐
APP专享直播
热门推荐
收起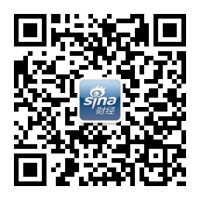
24小时滚动播报最新的财经资讯和视频,更多粉丝福利扫描二维码关注(sinafinance)