本文选自中国工程院院刊《Engineering》2022年第7期
作者: 崔青汝, 赵瑞, 王天堃, 张帅, 黄艳, 顾永正, 徐冬
来源:Robots Tackle DARPA Underground Challenge[J].Engineering,2022,13(6):2-4.
作为实现化石能源大规模低碳化利用的减排技术,CCUS是我国实现2060年碳中和目标技术组合的重要构成部分。主流的碳捕集工艺可分为三类:燃烧前、燃烧中(富氧燃烧捕集)和燃烧后捕集。与燃烧前捕集和富氧燃烧捕集相比,燃烧后捕集技术的捕集效率高、适应性好、应用广泛、技术较为成熟,是现阶段实现CO2大规模捕集的重要途径。
中国工程院院刊《Engineering》2022年第7期刊发国家能源投资集团有限责任公司赵瑞研究团队的《15万吨/年燃煤电厂燃烧后二氧化碳捕集示范工程》一文。文章介绍了15万吨/年燃煤电厂燃烧后二氧化碳捕集示范工程的总体概况及工程技术解读。文章指出,该项目采用新一代低能耗的化学吸收CO2捕集技术,捕集效率高、运行可靠,为燃煤电厂CO2大规模减排提供技术支撑。碳捕集装置自运行以来,展现出良好的技术先进性、运行可靠性和低能耗特性,引起了社会广泛关注和强烈反响,起到了良好的示范引领作用。碳捕集示范装置为燃煤电厂量身定制的减碳路径、设计的技术路线和研制的成套设备,为规模化捕集提供系统方案。
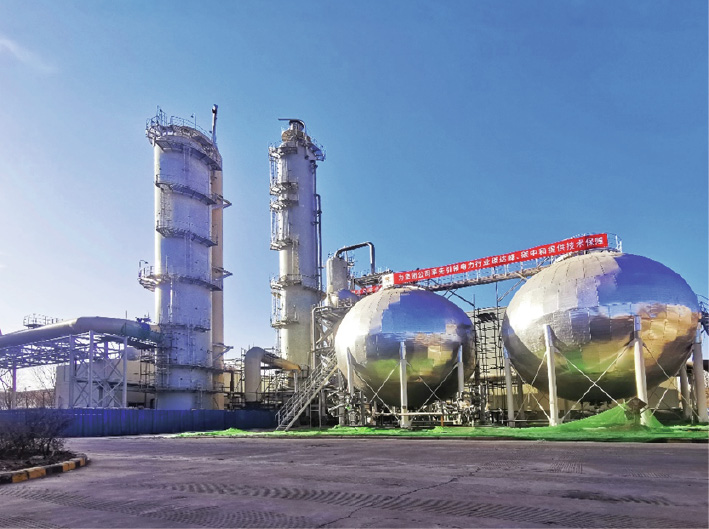
一、引言
气候变化是当今世界面临的最严峻挑战之一,目前我国年二氧化碳(CO2)排放总量达100多亿吨,占全球第一。燃煤在为我国经济发展提供助力的同时,也渐渐成为我国实现“碳达峰”和“碳中和”目标的主要挑战。在此背景下,煤炭低碳利用是未来发展的必然趋势,探索在煤炭利用尤其是燃煤发电过程中CO2的大规模减排新途径对我国实现碳中和目标至关重要。
碳捕集、利用与封存(CCUS)是将CO2从排放源中分离后直接加以利用或封存,以实现CO2减排的技术过程。作为目前唯一能够实现化石能源大规模低碳化利用的减排技术,CCUS是我国实现2060年碳中和目标技术组合的重要构成部分。主流的碳捕集工艺可分为三类:燃烧前、燃烧中(富氧燃烧捕集)和燃烧后捕集。与燃烧前捕集和富氧燃烧捕集相比,燃烧后捕集技术的捕集效率高、适应性好、应用广泛、技术较为成熟,是现阶段实现CO2大规模捕集的重要途径。
在燃烧后CO2捕集技术中,化学吸收法主要采用碱性胺基吸收剂吸收分离烟气中的CO2,因其烟气适应性好、捕集效率高、技术相对成熟,是最具大规模捕集CO2潜力的技术路线之一。加拿大边界大坝(Boundary Dam)项目是燃煤电厂百万吨/年CO2捕集示范工程(2014年投入运行),采用SO2-CO2联合捕集工艺,高浓度CO2用于70 km外油田驱油,每吨CO2的捕集成本约105美元。美国Petra Nova项目设计碳捕集能力为每年140万吨(2017年投入运行),采用化学吸收法进行捕集,高浓度CO2用于驱油,每吨CO2的捕集成本约为55~60美元。其受疫情影响已停运,且整体运行成本偏高,难以大规模推广。
年15万吨规模燃煤电厂燃烧后碳捕集示范工程从吸收剂选择、工艺优化、设备强化等多方面开展研究,创新集成了低能耗高效节能工艺,研制了针对燃煤电厂的低能耗成套碳捕集装置,并实现工业化运行。
二、总体概况
为加快CCUS技术的商业推广应用,仍需持续降低CO2捕集能耗。如何控制和减少碳排放已成为制约燃煤发电,乃至整个电力行业可持续发展的瓶颈之一。针对燃煤电厂烟气流量大、烟气中CO2低分压、烟气成分复杂、含有SO2和NOx酸性气体等特点,结合碳捕集高效率、低能耗、低成本的设计理念,创新性地开展了对燃煤电厂燃烧后碳捕集工艺的优化研究,建设了年捕集能力高达15万吨CO2的燃煤电厂燃烧后碳捕集示范工程(图1),这是目前已经建成的国内最大规模的燃煤电厂燃烧后CO2捕集与封存/驱油全流程示范工程。
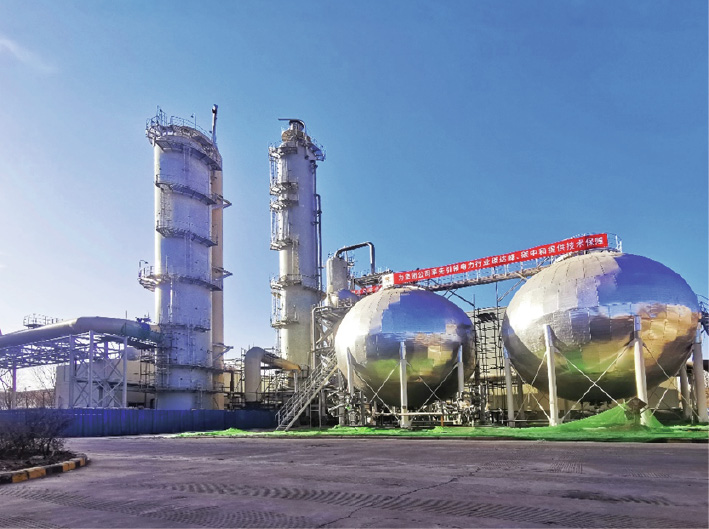
该碳捕集工程建设在国能锦界能源有限责任公司,依托1号600 MW亚临界机组,烟气取自经过超低排放改造的脱硫后尾气,每小时可捕集CO2 18.75 t,运行调节稳定,碳捕集工程在50%~110%范围内平稳运行。该工程是国家能源集团联合国内有关企业、高校、科研单位等优势力量,以项目为依托、协同创新、产学研用的重大碳减排示范工程。项目从2016年开始,历经方案论证、技术条件编制、小型试验验证、新型设备研制、工艺包开发和示范工程建设,实现整体装置的95%自主化。开发并研制出适应于燃煤电厂烟气特点的低能耗成套碳捕集装置;结合当地实际情况,开展基于CO2捕集、运输、销售、利用、封存/驱油全产业链的综合性整体分析,构建面向大型热力发电厂的碳减排综合解决方案。
三、工程技术解读
(一)集成高效节能工艺
针对燃煤烟气CO2浓度低,烟气总量大、湿度高、成分复杂等特点,为降低能耗,提高系统的经济性,本项目创新开发了“级间冷却+分级解吸+MVR(机械蒸汽再压缩工艺)闪蒸”的高效节能工艺(图2),从吸收-再生-节能三个维度同步提高整体系统的技术经济性。吸收塔内部的级间冷却工艺充分考虑吸收剂的最佳吸收温度,控制吸收塔温度分布提高吸收效率;再生塔分流解吸工艺通过能量匹配及梯级利用,确定合适分流比例,降低再生能耗;MVR真空闪蒸回收热贫液蒸汽,进一步耦合燃煤电厂应用场景,形成集成化节能工艺,充分利用成套装置系统内部再生气余热以及电厂余热,有效降低系统再生能耗。通过新型低能耗吸收剂和节能工艺的共同作用,相比乙二醇(MEA)的吸收体系,可降低能耗40%,形成了适用于我国燃煤电厂烟气CO2高效、低能耗捕集的新技术体系。
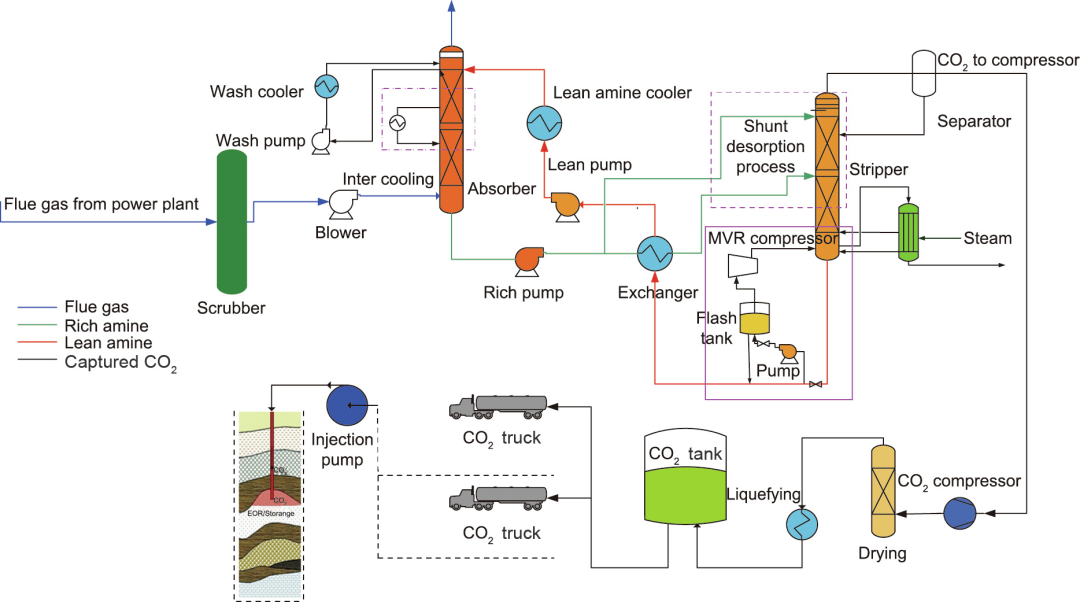
烟气自国能锦界能源有限责任公司1号机脱硫后出口烟道抽取,进入水洗塔内洗涤降温和深度脱硫,而后进入吸收塔,塔内设置级间冷却工艺。新型吸收剂吸收烟气中的CO2后成为富液,富液从吸收塔塔底流出后分为两股,一股进入贫富液换热器,热量回收后进入解吸塔,一股直接进入解吸塔,在再沸器的加热作用下解吸出CO2,解吸后的富液变为贫液,从解吸塔塔底流出,解吸后的贫液进入闪蒸罐进行闪蒸。解吸出的CO2经气液分离器后得到纯度99.5%(干气)以上的CO2产品气,进入压缩等后序工段进一步处理。压缩机出口CO2压力为2.5 MPa(表压),温度为40 ℃。缩后的CO2气体进入提纯塔进行脱水干燥。经干燥处理后的CO2气体进入CO2冷凝器和过冷器,液化降温制冷至-20℃以下,完全液化后送至CO2球罐进行储存。
(二)新型吸收剂及回收
本工程采用新型有机复合胺吸收剂。与常规MEA吸收剂相比,增加了多氨基胺及空间位阻胺,形成吸收容量大的复合胺(图3)。通过分子设计和功能基团匹配保证复合胺的吸收能力、解吸效果和运行稳定性,同时针对性开展吸收剂回收及再生技术。吸收剂的挥发特性直接影响运行成本,通过吸收剂复配和精细化调控实现吸收剂的低损耗运行。由于燃煤烟气中含有的少量杂质气体(NOx、SOx、O2等)会同有机胺发生副反应,长周期运行后导致胺溶液中热稳定性盐(HSS)的生成和富集,进一步引起溶液吸收能力的下降,为了使系统高效运行,胺溶液中的HSS水平应控制在胺浓度的3%以下。
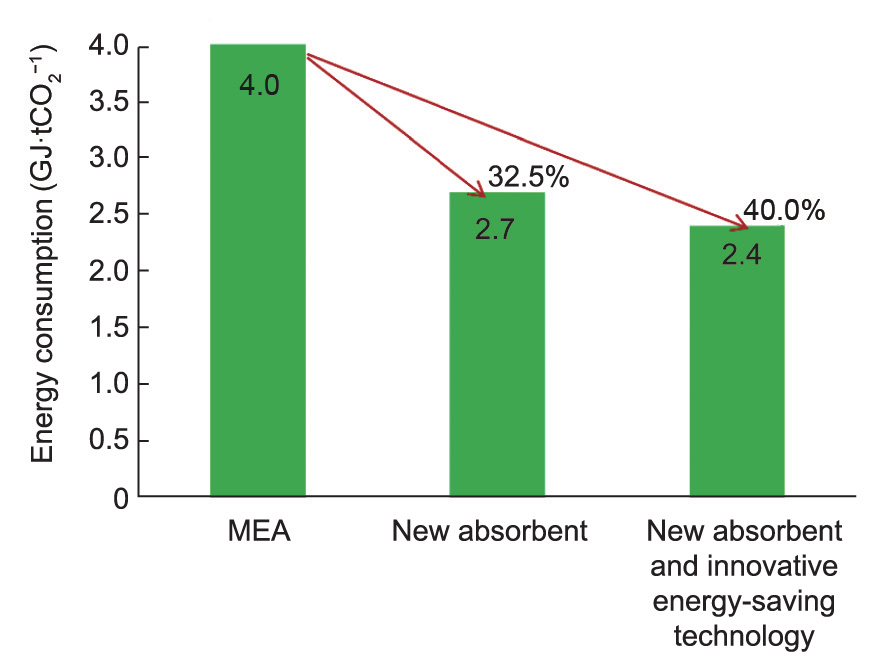
图3. 捕集装置能耗变化情况。
(三)碳捕集成套装备研制
本工程中成功研制了以塔器、换热设备、动力装置、压缩液化装置、干燥净化为主体的碳捕集成套装备,并成功应用到目前国内最大的燃煤电厂CO2捕集示范工程中,实现了低浓度CO2的高效率捕集,获得了纯度达到99.97%以上的液态CO2。碳捕集成套装备充分结合燃煤电厂的特点,系统性考虑上下游的匹配,提升了整套装置的性能。
1. 高效率塔器
针对燃煤烟气中CO2浓度低、分压低的实际条件,采用特殊型式的分离元件及塔内件,成功研制适用于燃煤烟气碳捕集的新型高效水洗塔、吸收塔和再生塔三塔设备,塔内主要由规整填料、支撑板、支撑梁、液体初始分布器、液体收集器、液体两级再分布器和气体分布器等组成。通过高效分离塔内件,构建均布系统,提升气液接触面积和停留时间,降低压降,提高吸收效率,降低能耗。塔内首次采用改性聚丙烯塑料填料(图4),通过化学改性提升塑料填料的吸收容量和亲水性能,在满足塔器要求的前提下,降低塔体总重量和总投资。通过再收集-再分布的设计,提高化学吸收溶剂的吸收效率和装置大型化的操作稳定性,降低能耗和溶剂损耗量。
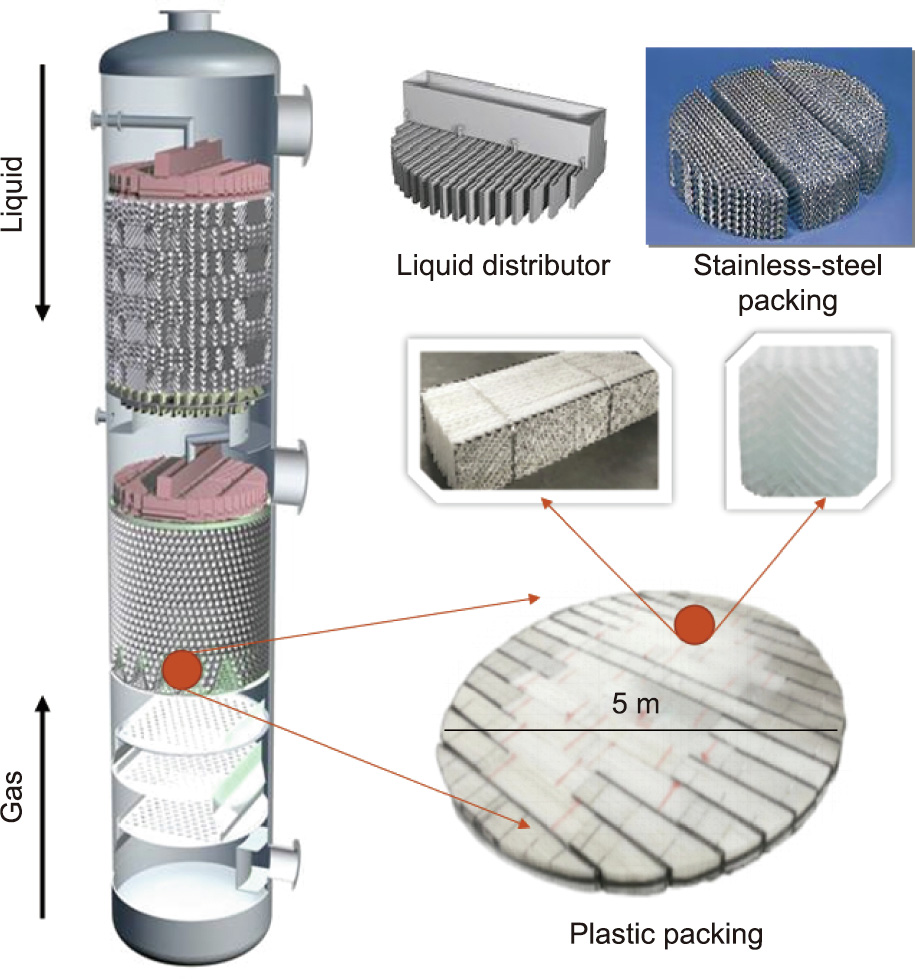
2. 节能换热装置
针对化学吸收系统低品位热难以利用的问题,自主研制高效低端差全焊接板式换热器。该换热器主要由换热芯体、上盖板、下盖板、折流板、密封垫及支座等组成,构成错流通道(图5),具有设备紧凑、可快速拆卸、安装空间小且安装方式灵活等特点。板式换热器传热面积大且传热效果好,在化工领域应用广范,与传统列管式换热器相比,有效降低了设备换热端差,平均可下降10 ℃,使整体热能回收效率提升0.5%,同时换热器材料消耗可降低约50%。
采用新型降膜再沸器(图6),吸收剂在降膜再沸器中停留时间短,有利于缓解吸收剂的热降解,传热系数大,蒸发过程在再沸器内部完成,无需塔釜空间完成气液分离。操作弹性大,单程蒸发强度大,50%流量负荷运行时仍可以保持较高换热系数。设备结构紧凑,一次蒸发量可达30%,相比常规的卧式再沸器效率更高。
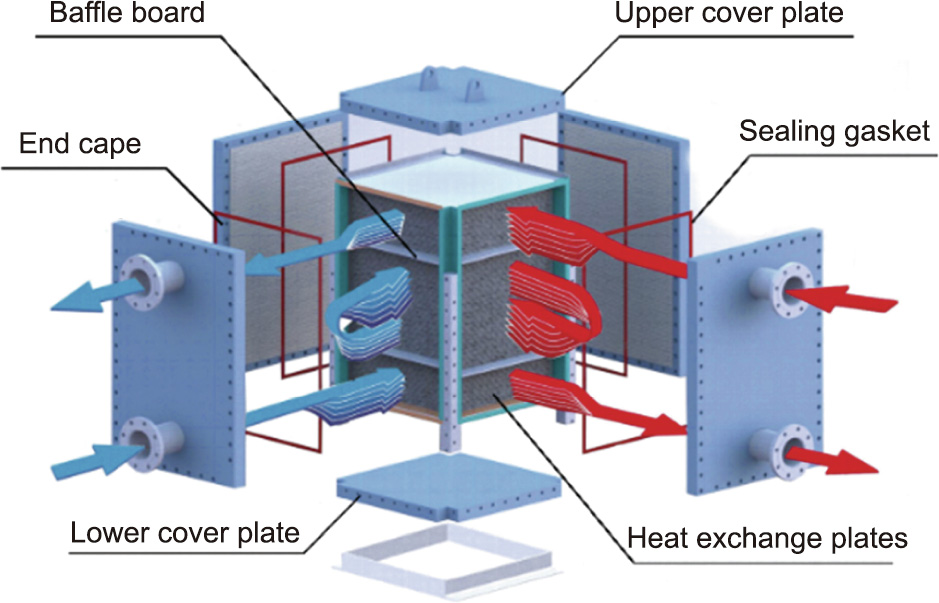
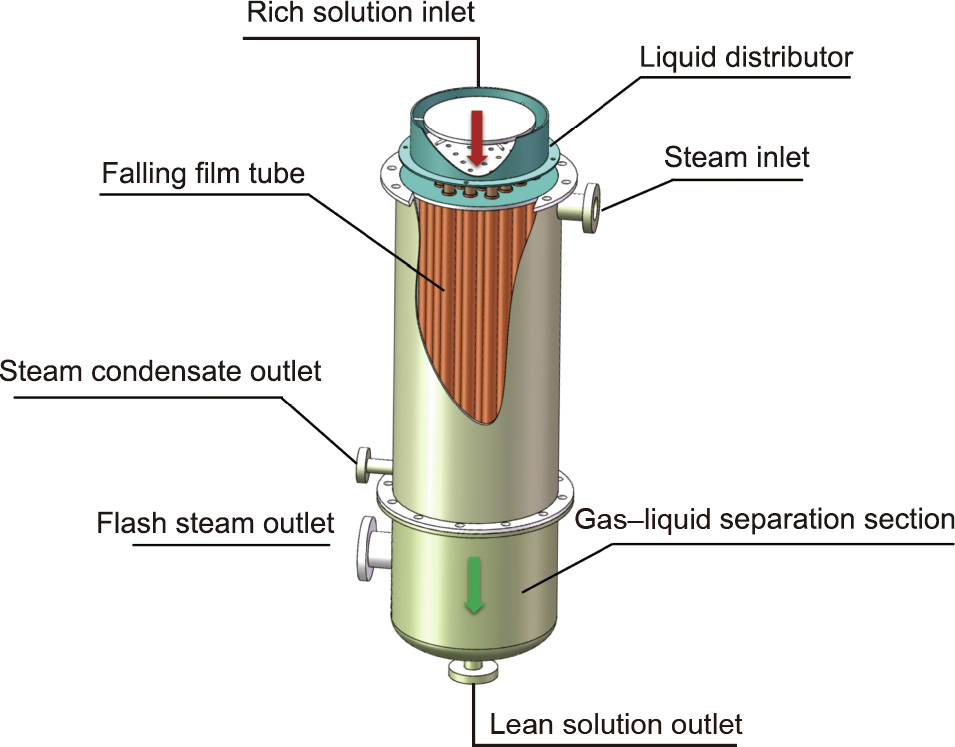
3. 压缩装置
本工程采用调节灵活的螺杆式CO2压缩装置,是目前为止单列最大的CO2压缩机。充分结合CO2工质的热力特性及碳捕集示范工程的运行工况,开发了非对称圆弧型线[图7(a)]。CO2型线采用5:7齿。阴、阳转子直径相当,承载能力高,适合CO2压差大的工况。压缩装置分为低压级和高压级,提高了阴转子的承载能力,解决了CO2压缩机大压差工况转子的刚性问题。该压缩装置因具有接触线短、啮合平稳、密封性好、效率高的优点,从而解决了自然工质的效率问题。采用滑阀调节,调节范围为15%~100%且能耗较低,通过设置两列50%的压缩机[图7(b)],做到节能高效灵活稳定。
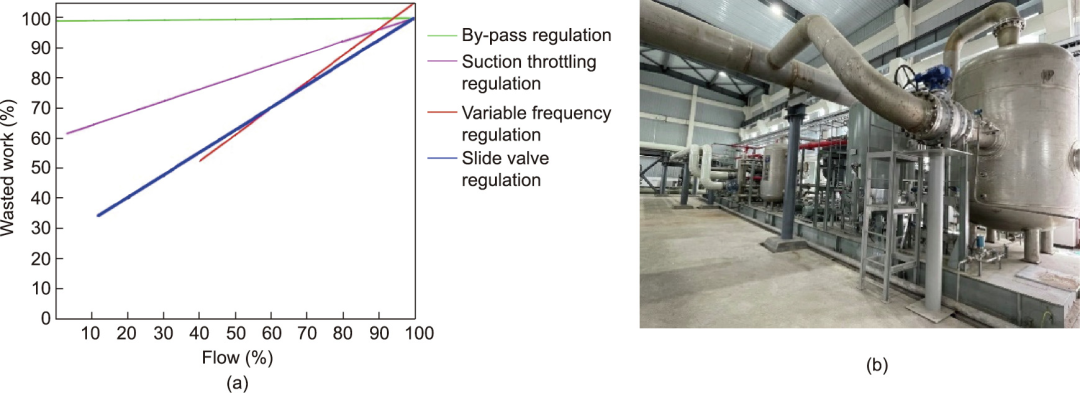
4. 干燥系统
本工程采用闭式循环脱水等压干燥系统(图8),干燥系统的外供再生气可反复利用,不外排蒸汽,大幅减少了蒸汽消耗。干燥系统分为CO2气体的干燥脱水、干燥剂加热再生、干燥剂冷却等过程,经过系统优化及程序化控制,干燥单元系统采用等压变温流程(TSA),可实现干燥剂在线干燥-在线再生,并连续稳定运行。干燥单元采用先进智能化控制,自动化程度高,对流量、温度、压力都进行检测。在设计和制造阶段,充分考虑设备材质、结构特性、仪表安全等方面的因素,实现CO2气体可精确监控,确保测量的准确性。
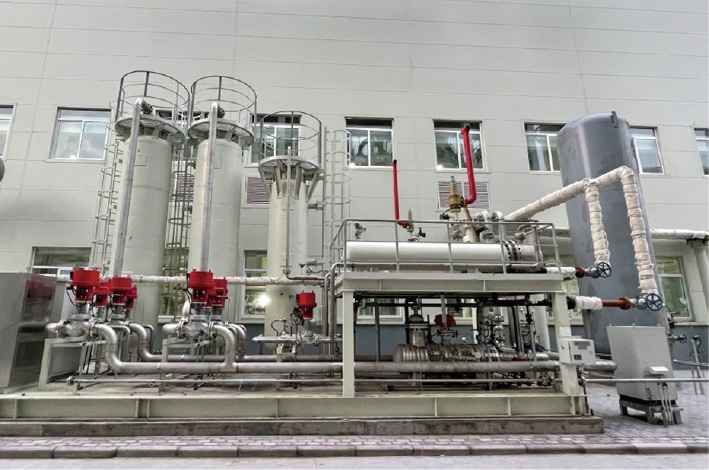
(四)建立了实现CO2捕集、运输、销售、利用、封存/驱油的全产业链模式
本工程实现了燃煤电厂捕集、运输、销售、利用、封存/驱油的全产业链运行。运输采用罐车外送,每车运输20 t。结合当地CO2市场的实际情况,将捕集到的CO2全部消纳利用,利用途径主要包括三部分:一部分用于附近油田驱油,距离约200~300 km;一部分用于化工利用领域,制备小苏打(碳酸氢钠),距离约200 km;还可以用于制备高值化工品(碳酸二甲酯和丙二醇等),距离约50 km。运输距离的远近直接影响CO2的成本,运输成本基本可按照每吨CO2 0.1元⋅km-1,每吨CO2的捕集成本约为250~280元,运输费用充分考虑利用端距离远近,约按每吨CO2 200元。每吨CO2的销售价格大于450~480元时具有可持续运行基础,因此围绕碳捕集装置区域,建立CO2全链条的循环利用途径将具有明显的带动作用。进一步围绕CO2捕集装置区域谋划CO2全链条循环利用的产业布局,是未来CCUS产业发展应该考虑的系统性问题。
四、结论
本项目采用新一代低能耗的化学吸收CO2捕集技术,捕集效率高、运行可靠,为燃煤电厂CO2大规模减排提供技术支撑。碳捕集装置自运行以来,展现出良好的技术先进性、运行可靠性和低能耗特性,引起了社会广泛关注和强烈反响,起到了良好的示范引领作用。碳捕集示范装置为燃煤电厂量身定制的减碳路径、设计的技术路线和研制的成套设备,为规模化捕集提供系统方案。
围绕碳捕集装置中新技术和设备的研究应用,未来碳捕集装置的智能化控制、与燃煤电厂集成化设计、整体低能耗运行等技术仍需进一步的开发及示范。针对燃煤机组,最大限度地降低吸收剂的损耗也是降低运行成本的有效措施。
建立规模化的碳循环体系是未来实现碳中和的重要方向,随着示范工程的长期运行,燃煤电厂碳减排的重点将转移至CO2的运输、利用/封存阶段,运输距离与CO2的成本密切相关,应探索近距离甚至就地消纳利用方式,以提升碳循环整体的经济性。
仍需大力拓展CO2资源化利用、能源化利用方式,进一步与化工行业、建材行业、生物固碳等行业的跨界合作,形成多途径、多产品、多形式且与捕集规模相匹配的利用方式。
注:本文内容呈现略有调整,若需可查看原文。
改编原文:
Qingru Cui, Rui Zhao, Tiankun Wang, Shuai Zhang, Yan Huang, Yongzheng Gu, Dong Xu.A 150 000 t·a−1 Post-Combustion Carbon Capture and Storage Demonstration Project for Coal-Fired Power Plants[J].Engineering,2022,14(7):22-26.
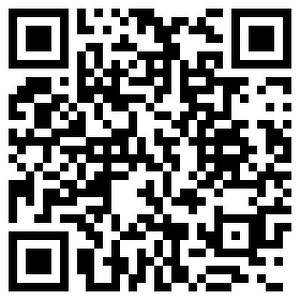
VIP课程推荐
APP专享直播
热门推荐
收起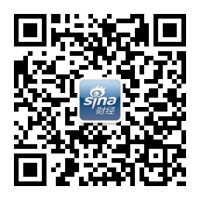
24小时滚动播报最新的财经资讯和视频,更多粉丝福利扫描二维码关注(sinafinance)