(来源:中航证券研究)
商业航天火箭发射频次加速抬升:商业航天作为新一轮科技革命和产业变革的重要代表技术,具备极高的战略意义和商业价值。海外来看,SpaceX“星链”计划快速推进,我国火箭发射频次、有效载荷及其他关键技术指标均有待提升,这背后便需要更强大的产业力量来助推,因此我国商业航天的发展肩负战略性使命,近年来也出台了一系列相关支持政策。由于商业航天产业具备反应快、周期短、性价比高等特点,在火箭发射提速、市场迅速扩张的背景下,火箭制造市场规模有望日益增长,相关的材料及工艺革新有望成为推动火箭制造环节升级迭代的核心;
火箭三大技术趋势推动新材料及工艺应用:我们认为,火箭可复用运载技术的发展、发动机推力的提升以及液体火箭发动机的应用趋势为未来三大重要发展方向,这也会带动火箭制造环节中新材料与新工艺的应用变革:①可复用技术能够降低火箭的综合发射成本,在对应用材料提出较高性能要求的同时提高了整体价值量;②发动机推重比的提升依赖于发动机燃烧效率,从而推动了耐高温、高导热的材料以及相关加工工艺的革新;③液体火箭发动机的应用趋势及推进剂方案会对贮箱材料的选择提出不同的要求;
新材料助力发动机性能提升:推力的递增是火箭载荷提升的先决要素,而热端材料的极限性能高度是发动机能否持续提升燃烧效率和推力的关键。①如今铜铬铌、铬锆铜合金作为新生代的推力室内壁材料,已开始在先进火箭发动机中得到应用。我们预计,2025-2030年期间全球商业航天领域铜合金市场空间规模约为29.0~40.6亿元,国内以铜铬铌合金为代表的推力室内壁产品有望随火箭应用材料需求的推进而迎来从0到1的增长。②热障涂层主要用于提高燃烧室耐温极限,在商业航天可复用技术推进以及大推力火箭的需求牵引下,我们预计2025-2030年期间国内商业航天热障涂层材料市场空间约为20.6~54.7亿元,且具备持续增量空间;
制造需求引领新工艺变迁:商业航天最关键的问题是经济性,可复用技术的出现帮助降低了成本,同时较高的载荷也对更高性能的部件提出了要求,这有利于新工艺的拓展应用:①增材制造目前在航天领域主要应用于卫星结构、火箭箭体以及发动机部件,其中由于再生冷却系统对于火箭有重要作用,而增材制造可以很好的兼顾成本和工艺复杂度,因此成为商业航天不可或缺的关键技术,下个阶段对于低成本、大尺寸增材制造部件的需求有望提升,我们预计2025-2030年期间国内商业航天领域增材制造市场空间约为105~240亿元;②热等静压技术受制于较高的成本,主要应用于航空发动机中,而在战略航天时代应用较少,目前产业呈现出欧美领先,国内追赶的态势,在商业火箭可复用技术和大载荷的趋势下,下游企业对性能更好的部件需求旺盛,我们判断热等静压或将被商业航天火箭公司逐步接受,逐步打开其在航天领域的应用空间;
投资建议:在国内火箭可复用运载技术持续发展、发动机推力持续提升和液体火箭发动机的应用大趋势下,未来液体火箭发动机的升级迭代和火箭制造市场的增长将共同牵动上游新材料和新工艺的应用需求,建议关注:斯瑞新材(铜合金);华秦科技、新劲刚(热障涂层材料);铂力特、华曙高科(增材制造设备及服务);钢研昊普、欧中科技(热等静压设备及服务);超捷股份、光威复材、钢研高纳、盛帮股份(其他相关结构件及零部件)。
风险提示:原材料价格大幅波动、企业募投项目不及预期、下游需求增长不及预期、技术路线迭代风险、股价大幅波动风险等。
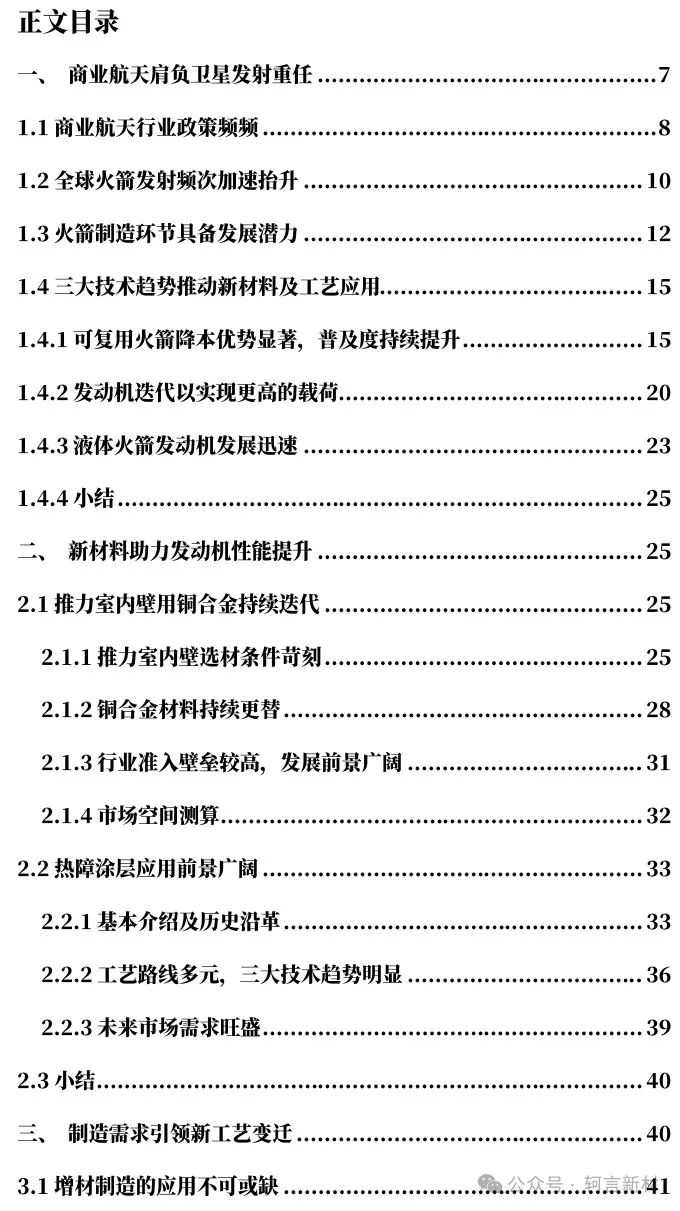

一、商业航天肩负卫星发射重任
自从SpaceX提出“星链”(Starlink)计划以来,人们开始意识到低轨卫星(LEO)资源争夺的重要性,商业卫星的发射频次正在显著提升。由于卫星绕地球运行需要轨道和频段资源,国际电信联盟(ITU)提出在轨道和频段资源获取上遵循“先登先占、先占永得”的原则,因此轨道和频段是有限且不可再生的战略资源。根据ITU数据,地球低轨卫星总容量约6万颗,目前正在运行的近地卫星则有4800颗。SpaceX的星链计划要在2027年前将4.2万颗卫星送入低轨,这使得近地轨道资源变得越来越抢手,也造就了各国竞争趋于白热化。虽然我国在低轨卫星通信领域起步较晚但发展较快,在星链计划的推动下,商业卫星的发射频次愈发密集,这为商业火箭的需求打下了广阔的增量基础,而我国商业航天公司正成为低轨卫星星座建设的中坚力量。
我国商业航天计划当中,最受关注的无疑是对标Starlink的星座组网计划,其中比较大型的包括“GW星座”以及“G60星座”,两者总数约2万余颗:
“GW星座”又名国网星座,是由中国卫星网络集团主导的互联网近地轨道卫星计划,共规划发射12992颗卫星。GW星座包含两个子星座(GW-A59和GW-A2星座),目标为形成覆盖全球的互联网卫星星座,未来将推出手机直连卫星通信模式;
“G60星座”又名千帆星座,项目实施主体是上海垣信卫星,2024年8月发射的18颗卫星为首批组网星。计划在2024年发射108颗卫星形成初步商业服务能力,该项目的第一阶段的目标是在2025年底实现648颗卫星提供区域网络覆盖,第二阶段计划在2027年完成一期1296颗卫星组网建设,实现全球网络覆盖,第三阶段到2030年底实现15000颗卫星提供手机直连多业务融合服务。
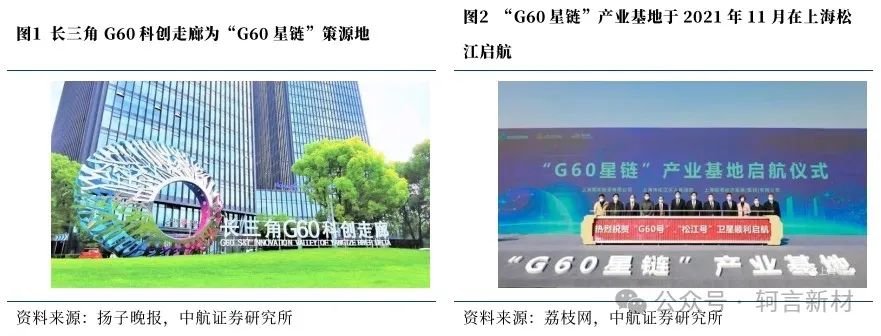
在二十世纪上半叶,“美苏争霸”的背景推动了大国间的军备竞赛,两者都将太空竞赛作为展示自己科技实力和国家威信的重要手段,从而带动了一系列材料、科技的进步。反观当前SpaceX的星链计划和复杂多变的国际形势,低轨卫星的发射和对近地轨道资源的争夺则成为了中美科技角逐的新战场。在ITU的规则之下,当前我国的卫星发射频次和数量亟需提升,以缩小与SpaceX每年高频发射的差距,这背后便需要更强大的产业力量来助推,因此我国商业航天的发展肩负战略性使命。
1.1
商业航天行业政策频频
商业航天是全球新一轮科技革命和产业变革的重要代表技术,由于其具备商业和战略价值,各国纷纷推出了相关规划。欧美等发达国家在航天领域已布局多年,近期美国在《2024年国防部商业航天一体化战略》中提出,需推动商业航天解决方案更有效地融入国家安全太空架构,以协调国防部工作。可见商业航天在国家战略层面具备的地位举足轻重。
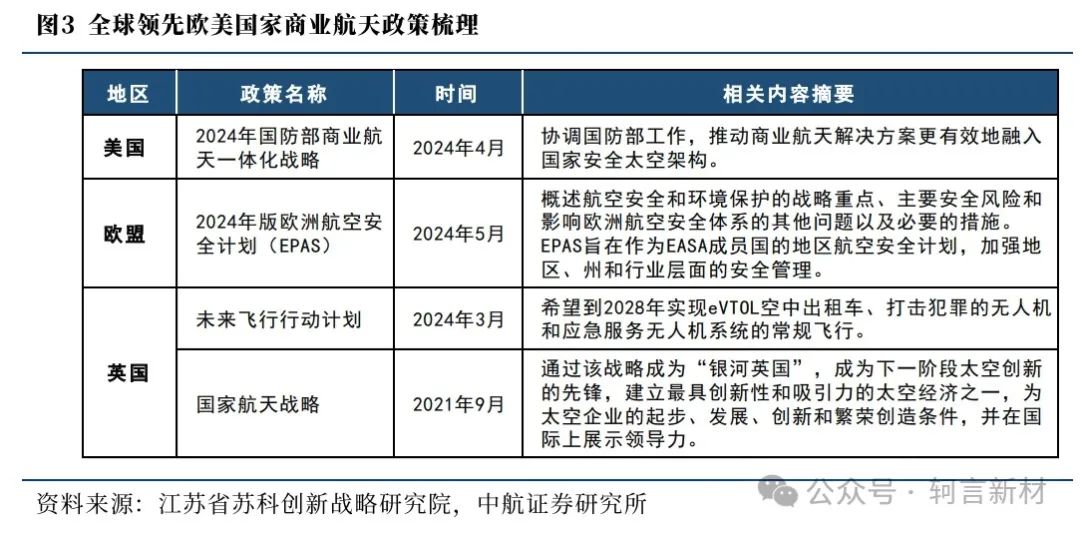
我国对于商业航天发展的政策扶持主要起于“十二五”末。2014年国务院首次提出鼓励民间资本参与国家民用空间基础设施建设,指导意见表明了国家支持社会资本参与商业航天发展的立场,发出了支持鼓励商业航天的强烈信号。该意见普遍被业内认为是我国推动商业航天发展的起点性文件,自此改变了由国家主导航天发展的模式,开启了由政府主导和市场推动相结合的新型商业航天发展路径。2023年12月,中央经济工作会议提出打造商业航天等若干战略性新型产业,商业航天成为我国新质生产力代表。作为新质生产力的重要方向,“商业航天”也首次被写入我国《2024年政府工作任务》,报告提出需大力推进现代化产业体系建设,加快发展新质生产力,积极培育新兴产业和未来产业,积极打造生物制造、商业航天、低空经济等新增长引擎。

随着多份国家政策和中央经济工作会议的战略部署,多个地方政府陆续出台商业航天发展行动规划和配套政策。在国家规划的牵引下,目前我国已有27个省、直辖市和自治区在“十四五”规划和2035年远景目标纲要中布局航天产业发展。从政策意图上看,各地方政府主要采取与传统产业结合的方式发展商业航天,利用地区资源、产业基础和科研条件,因地制宜制定政策。从政策要点来看,地方政府积极扶持低成本、批量化的卫星研制。此外,地方政府自身规划大规模星座组网和运营项目,结合地区优势支持不同类型星座建设,接着成立引导基金,以资招商、以业务带动产业发展的思路较为明确,最后是做好基础配套,发布金融、土地、税收等多方面改善营商环境的政策鼓励商业航天企业落地。
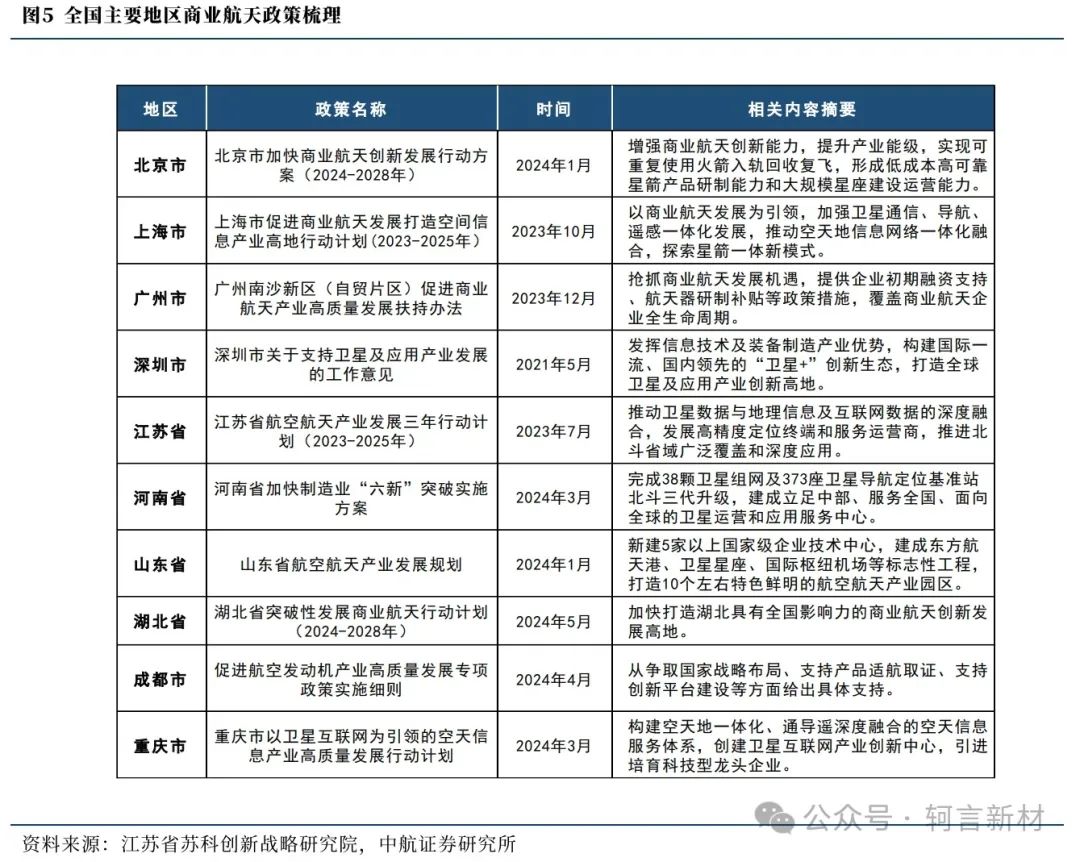
1.2
全球火箭发射频次加速抬升
全球火箭发射数量在近年来呈快速增长态势,2023年商业发射次数占比已过半。据The Space Report发布的《2023年全球太空活动年度报告》,2023年全球共进行了223次航天发射任务(同比增长19.9%),发射载荷2911个,全球航天发射次数和载荷发射数量双双打破了发射记录。据统计,2023年全球轨道发射任务中,政府发射78次(占比35.0%),11次由商业公司根据与政府签订的合同进行(占比4.9%),商业发射120次(占比53.8%),其余发射未提及具体划分情况。当前商业发射次数已占据一半以上,随着以SpaceX为代表的商业航天公司快速推进发射进程,未来该占比仍有持续增加势头。
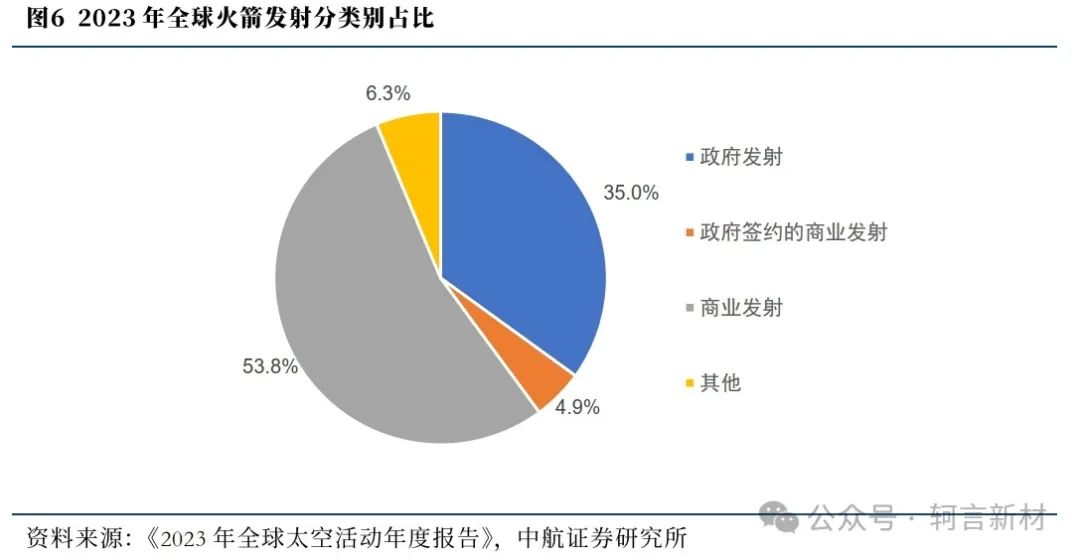
分国家来看,2023年美国以109次发射占据世界第一,我国67次发射排名第二,俄罗斯以19次发射位居第三,其余实现轨道级发射的国家和地区,发射量均为个位数。中美两国火箭发射数量居前,但商业模式有别。美国在航天发射领域中居于领先地位,发射主要以SpaceX等私营企业为主,SpaceX于2023年发射98次(含星舰组合体2次试飞失利),平均每3.7天发射一次,打破了2022年发射87次、平均4.2天发射一次的记录。目前我国航天发射仍然以国家队为主,但随着私营企业的快速发展,未来有望接力国家队,承接更多的发射任务。2023年我国共计发射火箭67次,涉及载荷200余个,其中1个载荷因1次发射失败未能入轨;其中航天科技集团48发,航天科工集团6发,民营火箭企业累计13发。根据斯瑞新材公告,2024年上半年,全球共计火箭发射126次,其中美国73次,中国30次。美国火箭发射数量的背后离不开SpaceX的高频次发射,相比之下,国内商业航天私营企业尚未形成规模化发射,我国在火箭制造规模、火箭可复用技术等多方面均与美国存在一定差距。

从火箭制造国家来看,2023年全球10个国家制造的火箭在13个国家的发射场发射,较2022年相比,更多的国家加入到火箭制造与发射行列。2023年中美两国全球火箭制造产量最高,分别为116枚和67枚(分别同比+33.3%/ +4.7%),全球占比分别为52%和30%,合计占比82%,延续了近年来中美火箭制造产量明显高于其他国家的态势。
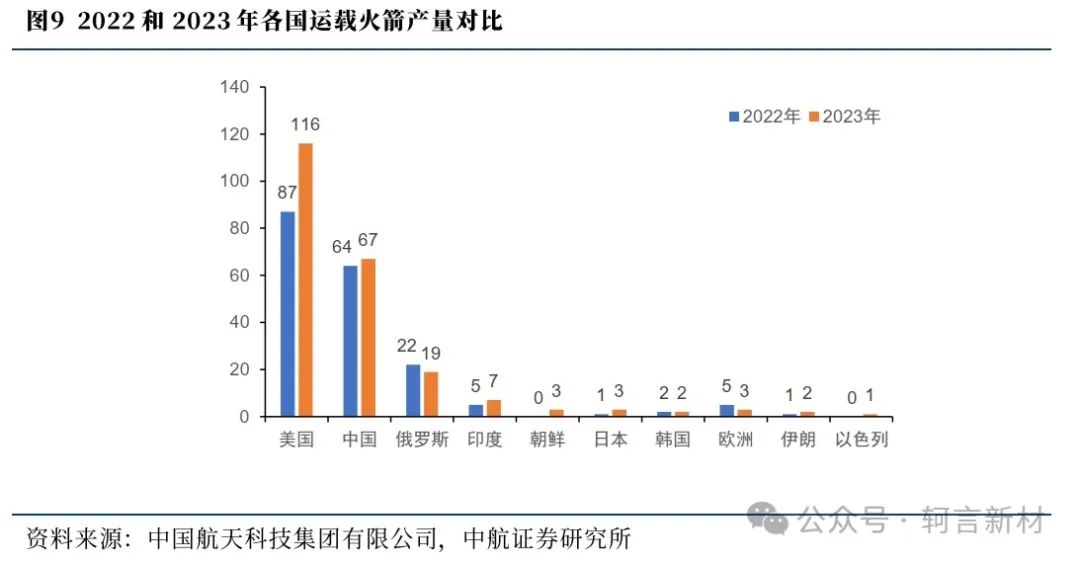
纵观国内火箭发射市场的发展进程,自2014年国家政策放开民营商业航天的限制起,民营火箭制造企业如雨后春笋般涌现,商业航天行业正从单一的国家领导模式,向多元化、市场化的商业模式转变。目前大部分火箭仍然由体制内的航天企业发射,未来中国的商业航天发展模式也将与美国有所区别。我们判断,随着各企业发射任务的压力逐步增大,以及对星网盈利性要求的逐步提高,商业航天反应快、周期短、性价比高的优势有望逐一体现。
1.3
火箭制造环节具备发展潜力
火箭可按照级数分为单级火箭和多级火箭,目前相对成熟的箭型和在研火箭基本为多级火箭。火箭制造环节中,火箭发动机和贮箱的价值量较高,据中国数字科学馆统计,两者在一子级和二子级中的价值量占比之和分别达到77.9%和58.1%,其他成本还包括电气设备、火工品线路管路、燃料等。
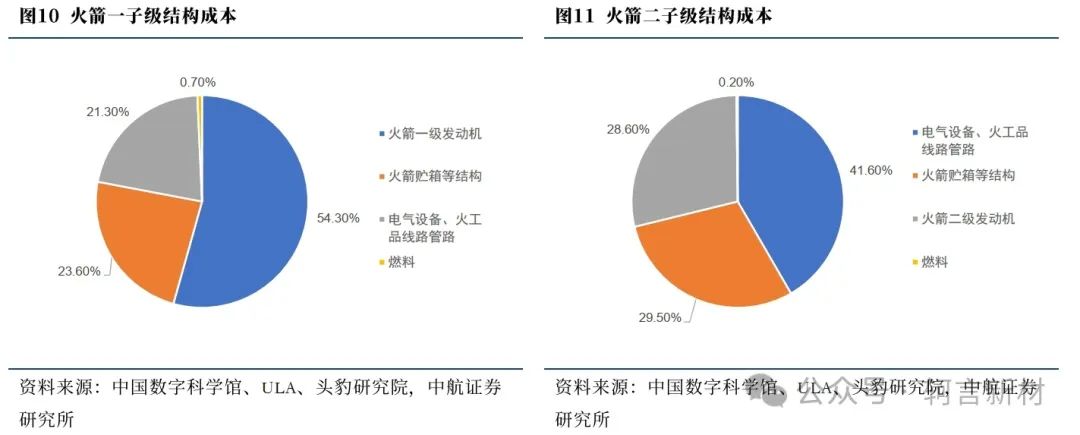
火箭的载荷、经济性、可靠性及使用寿命都取决于生产制造环节,火箭设计参数的不断提升及成本的下降与材料及工艺的应用密不可分。液体火箭中具备高价值量的部分包含①整流罩、②贮箱、③发动机、④其他结构件及零部件等,我们在下图中对国内火箭制造各环节所应用的相关材料、工艺及研发制造企业进行了梳理:
整流罩:整流罩通常位于火箭的顶部,用于保护卫星等有效载荷顺利进入太空,可以为航天器等有效载荷提供良好环境,保护其内部所搭载的载荷在大气层内飞行时免受气流、热环境等有害因素的影响。出于空气动力学方面的考虑,大部分整流罩都由高强度、轻质、耐高温,且无线电透波性强的材料制成,包括碳纤维复合材料、聚甲基丙烯酰亚胺泡沫(PMI)等。国内的火箭整流罩生产参与企业除了航天一院703所、航天八院等院所外,还包括爱思达航天、超捷股份、航天神坤等民营生产企业;
贮箱:火箭贮箱作为推进器关键结构,占据了箭体60%的质量,储存液体推进剂的同时还承担着大部分的结构载荷,是决定运载火箭性能的关键。贮箱材料不仅需要具备一系列优异的力学性能,还要能够在恶劣条件下表现出高可靠性和高耐久性,其发展的趋势主要包括结构轻量化、强度和模量的提高、工作寿命的延长。轻质高强铝合金(包括猎鹰9号采用的铝锂合金)为当前主流的贮箱结构材料,而SpaceX的星舰采用的奥氏体不锈钢贮箱、处于研发阶段的复合材料贮箱也有望成为未来的发展趋势。工艺方面,目前传统热焊接工艺是贮箱加工的主流方案,而电弧增材、搅拌摩擦焊等工艺则可能成为下一代贮箱生产中的重要工艺。我国火箭贮箱生产及加工企业包括九天行歌、寰宇航天、超捷股份、融速科技等;
发动机:运载火箭对主发动机的要求包括大推力、高比冲、高推重比、高可靠、低成本等。这些要求高且相互矛盾的指标,决定了发动机以用尽材料极限性能的极端参数运行,在较小结构空间实现高水平能量剧烈释放与转化的工作特点。①材料方面,可重复使用液体火箭发动机推力室身部一般由高导热的铜合金内壁,以及镍基合金外壁连接而成。此外,在发动机燃烧室及涡轮叶片上应用热障涂层则有助于提高涡轮前温度和延长叶片使用寿命。②工艺方面,可重复使用发动机生产环节涉及的工艺包括高温合金和钛合金的精密铸造成形技术,以及在发动机壳体等精密构件中使用的增材制造技术,在泵叶轮和涡轮盘等旋转关键零件中使用的热等静压技术等。我国液体火箭发动机铜合金推力室内壁生产企业主要包括斯瑞新材,高温合金铸件生产企业主要包括钢研高纳,热障涂层供应企业包括华秦科技、新劲钢等,具备增材制造服务及设备产能的企业包括铂力特、华曙高科等,具备热等静压工艺的企业包括钢研昊普、欧中科技等;
其他结构件及零部件等:除了上述部件外,火箭还包括各类阀门、管路、着陆腿等其他零部件,涉及到的材料包括碳纤维、铝合金、不锈钢、橡胶、碳纤维复合材料等,相关上市企业包括超捷股份、光威复材、盛帮股份等。

在火箭发射提速、商业航天市场迅速扩张的背景下,火箭制造市场规模有望日益增长。随着国内商业航天企业对火箭可复用技术研究的持续推进,火箭发射试验多点开花,相关的材料及工艺革新有望成为推动火箭制造环节升级迭代的核心,上游相关材料生产商及加工企业有望享受终端行业的高速发展红利。
1.4
三大技术趋势推动新材料及工艺应用
通过观察目前Space主流火箭型号“猎鹰系列”和“星舰系列”的运行情况,可以发现,无论是火箭回收次数的不断增加、发动机迭代下载荷提升还是火箭推进剂应用层面,SpaceX的发展路径都可以作为商业航天的榜样来加以学习。下面我们将通过分析火箭技术的发展现状,从火箭的可复用运载技术发展、发动机推力的提升以及液体火箭发动机的应用趋势出发,来讨论未来新材料与新工艺的应用变革趋势。
1.4.1
可复用火箭降本优势显著,普及度持续提升
垂直起降重复使用运载火箭具有降低发射成本、解决落区安全等优势,SpaceX凭借对猎鹰9号第一子级的回收复用,其火箭发射成本优势在世界范围内已大幅领先。2010年首飞的猎鹰9号火箭近地轨道运力约10吨,在研制阶段就把载荷的单位发射价格锚定至3000美元/千克,由此拉开了火箭发射降本的序幕。当前猎鹰9号能将22.8吨载荷送入近地轨道,复用猎鹰9号火箭的单位发射价格可降低至1000美元/千克以下这让其他可复用火箭的单位发射价格难以匹敌。此外,SpaceX设计的具备超大载荷的全复用火箭“星舰”瞄准了更低的单位发射成本,马斯克宣称,星舰的发射成本远低于大多数火箭,单次发射成本未来将降低到200万美元,每公斤有效载荷的发射成本有望降低至20美元内。据航天科工三院306所消息,目前在仅回收第一子级的情况下,重复使用1次,单位载荷发射价格可降低25.9%;重复使用2次可降低36.3%。如果第二子级也可回收并重复使用,单位载荷发射价格在重复使用10次时可降低至初始成本的10%,复用技术对火箭发射成本的节约有着十分可观的前景。
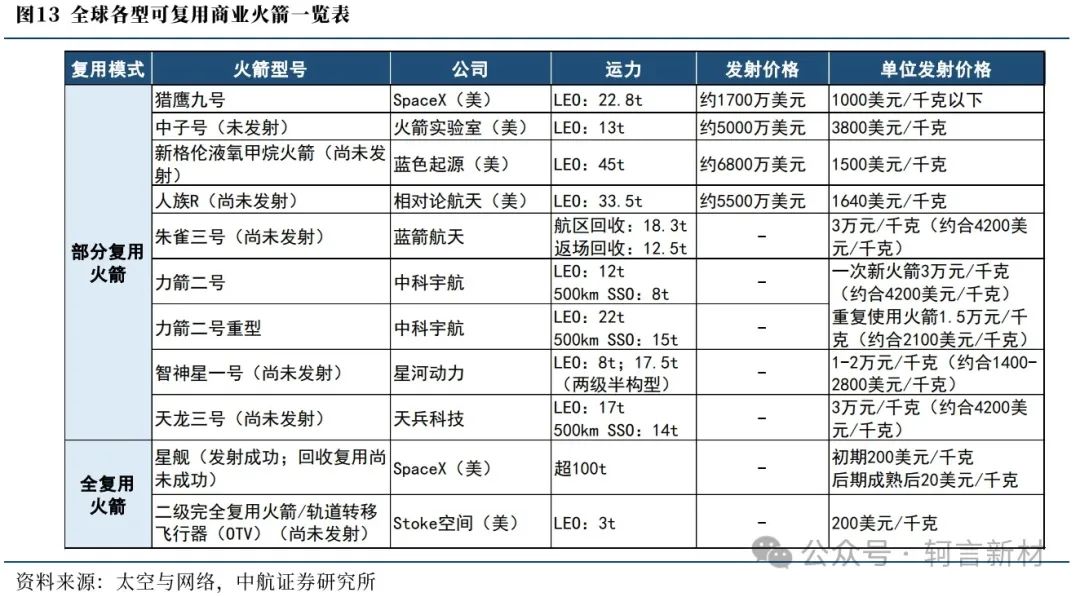
猎鹰9号作为目前最成熟的可回收式中型运载火箭,拥有多发并联、垂直回收、多次使用等优势,是世界上第一款具有轨道运输能力的可重复使用火箭。拆分结构来看,主要由一子级、中间级、二子级和整流罩四个部件组成。在每次回收后往往会对火箭各部位进行一定的升级改进,每次改进的目标都是为了提升火箭的运载能力和重复使用能力,我们可从其中窥见材料升级和工艺改进的端倪。

1) 一级火箭包含9个梅林发动机,其推进剂贮箱以铝锂合金为材料,使用摩擦搅拌焊接的方式制造。一子级的底部装有4个着陆腿,由碳纤维复合材料缠绕的铝制蜂窝吸能结构制成,会在一子级回收降落时打开,以确保箭体的平稳着陆。作为火箭回收的主体部分,由于需要经历极端的再入环境,因此一子级的材料更迭也较为频繁。在猎鹰9构型改进过程中,材料和工艺的升级增强了部件的可复用性:
更新外部涂料:为更好的保护一子级免受极端再入环境的影响,最新火箭采用了新的热防护技术,火箭黑色级间段以及电缆管线和着陆支腿均采用了复用性能更高且无需喷漆的新型热防护材料;
专用热防护罩:加强了位于火箭底部靠近发动机部段的热防护罩,该热防护罩用于保护发动机和推进系统管路,但此前使用的复合材料热防护罩每次发射后都要进行更换,此次的改进将有助于其复用,能提高一子级的生产速度和重复使用率;
强化八角网:猎鹰9号的八角网承载了火箭一级的所有9台梅林发动机,中间通过隔板间隔开。构型迭代后八角网采用了强度更高的铝合金材料,并采用螺栓连接,而非像此前焊接到箭体上,以便缩短检查和维修时间,同时便于从猎鹰9号一子级改作重型猎鹰火箭的助推器。
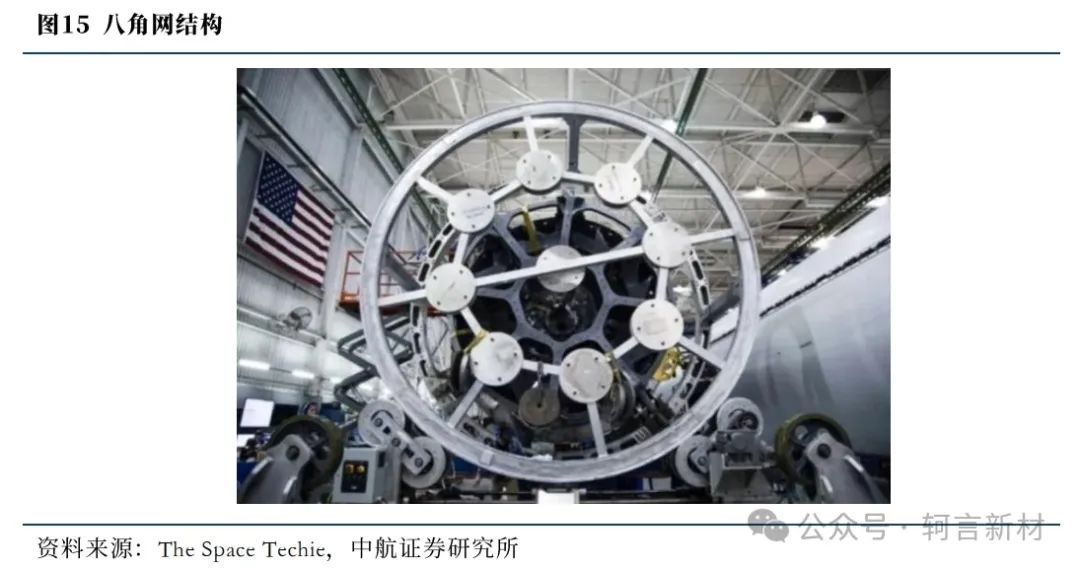
2) 二级火箭装有一台真空版梅林发动机,它在一级火箭的主发动机关闭和分离后启动,将有效载荷送入轨道,并且可以多次点燃以将不同的载荷送入多个轨道。二级火箭推进剂贮箱结构与一级火箭贮箱类似。

3) 中间级处于一子级与二子级之间,由碳纤维面板包夹蜂窝铝芯层的复合材料制造,具有多项功能:一用于分离火箭的一级与二级,二则为二级火箭的大扩张比发动机提供安装空间。火箭一、二级分离时,中间级与二级火箭下部脱开,随一级火箭一并回收。在猎鹰9号版本构型迭代中,位于中间级的栅格翼也经历了材料升级替换:
升级栅格翼:SpaceX火箭回收系统的一个明显特征就是采用了栅格翼,栅格翼的翻滚、俯仰和偏摆的三维度控制动作可以让一子级实现最大20度角的偏转,栅格翼与反推力系统的配合即可实现火箭的姿态控制。由于此前型号中的栅格翼都采用铝合金+白色防热材料的组合,在实践中存在返回后结构损毁严重,无法复用的问题,因此在构型迭代中,被改为无涂层、一体化铸造的钛合金栅格翼,同时尺寸也有所增大。相比之下,钛制栅格翼不仅能经受住高温高压,且回收后不需进行大修就可再次执行飞行任务;
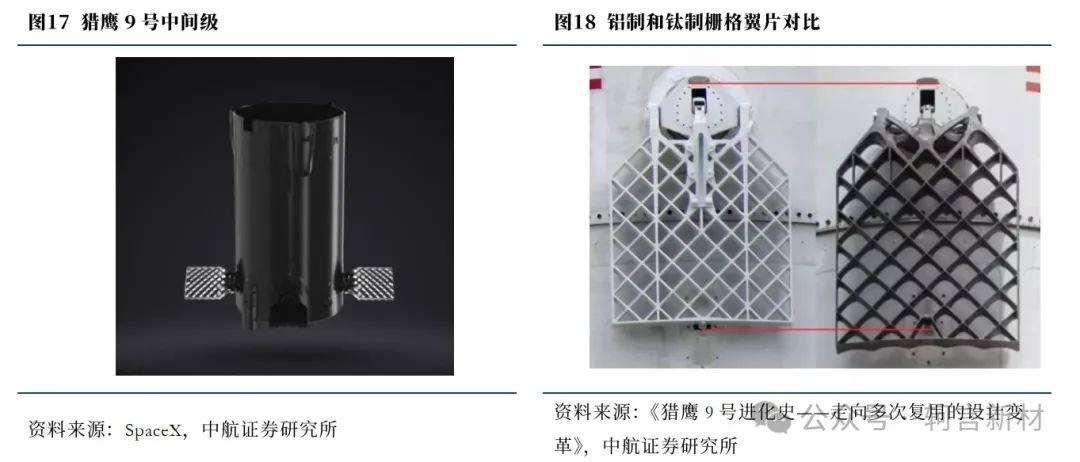
4) 整流罩是由碳纤维复合材料制成的锥形结构,由两个半壳组成,用于减少大气阻力和保护载荷免受温度、振动和电磁干扰等影响,可为卫星及其他载荷提供入轨保护。在火箭飞行约3分钟后,达到大气层外时,整流罩会被抛出,SpaceX已实现了在海上网捕整流罩来达到重复使用和降本的目的。
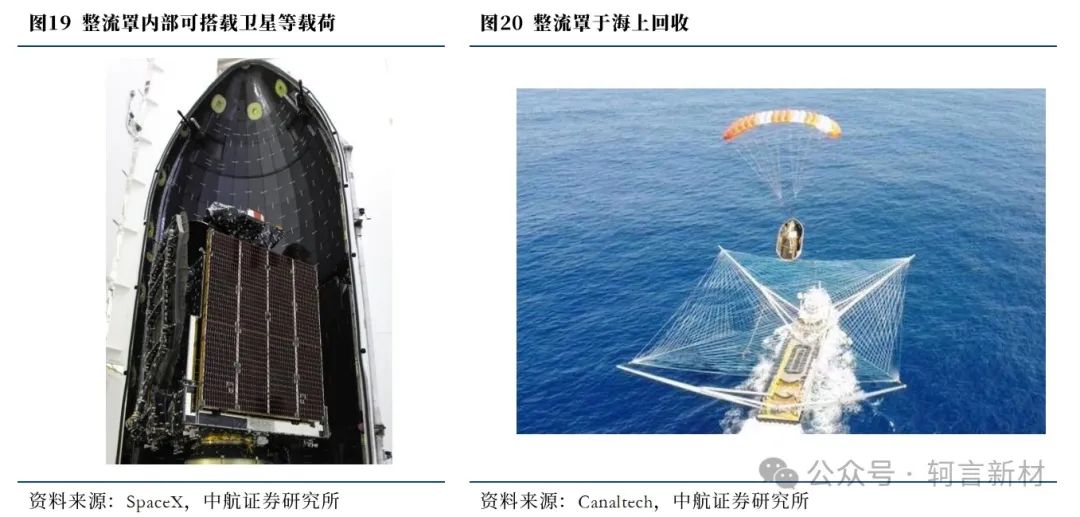
我国在重复使用运载火箭方面的发展进程较美国虽有一定差距,但航天科技集团和民营商业航天公司也都相继提出了垂直起降重复使用运载火箭方案,目前也正在开展相关技术验证和重复使用液体火箭发动机的研制。目前我国在研的可回收火箭处于垂直起降(VTVL)试验阶段,已有多型火箭及验证箭完成了可回收试验。2024年6月23日,航天科技八院进行了我国第一次可回收火箭10公里级VTVL试验,高度达到了12公里的平流层。随后,在2024年9月11日,民营企业蓝箭航天的朱雀三号VTVL-1试验箭圆满完成10公里级VTVL试验。通常火箭在10公里左右的高度会经历最大动压,此时火箭受力情况最为复杂,对姿控系统的考验也最大,是可回收火箭的重要试验。我国民商企业的下一代火箭的研发方向基本为可重复使用,目前国内已有多型可回收火箭在研,近年将陆续发射,推动我国火箭的可复用技术发展进程。

重复使用运载火箭技术作为我国商用火箭科研大方向,材料应用、制造工艺和控制系统的更新迭代将成为提升火箭回收可靠性的核心。我们认为,火箭可复用趋势在对材料提出较高性能要求的同时提高了整体价值量,建议关注以下材料及工艺:①特种铜合金材料的应用解决了发动机推力室内壁对耐高温和高热传导等性能的需求;②热障涂层帮助提高了热端部件的耐温极限;③增材制造、热等静压等工艺的应用实现了部件的一体化成形,在减少工序、提高可靠性的同时实现了轻量化。
1.4.2
发动机迭代以实现更高的载荷
星座发射亟需更大载荷的火箭。近年来,SpaceX发布了雄心勃勃的星链计划,出于商业竞争和发展安全等多方面因素考虑,国内也发布了GW星座和G60星座的低轨卫星集群发射目标。根据ITU的规则,星座需在规定时间内完成组网,这意味着在短时间内需要将大量的卫星发射进入轨道,这就需要更大载荷的火箭。此外,为了实现SpaceX单位载荷成本快速降低的目标,使用超大载荷的火箭来降低平均发射成本也就成为了重要选项。目前世界主流的商业航天火箭的载荷情况如下;

大推力发动机与火箭并联技术两大绝技助力大载荷火箭。从上图可以看出,近年来国内外火箭的载荷均有所提升,国内箭型如蓝箭航天的朱雀一号到朱雀二号,运力提升接近20倍。SpaceX重点打造的猎鹰系列和星舰系列大运载火箭具备较高的运载能力,遥遥领先于其他火箭公司。我们认为主要是因为其主流箭体兼具大推力的发动机以及多并联的宽口径火箭构型——以星舰为例,其使用的猛禽3液氧甲烷发动机推力可达280吨,同时星舰还具备33台猛禽发动机的并联。有了这两项绝技,星舰才得以成为一台真正的推力猛兽。此外,猎鹰系列火箭也多采用大推力发动机及并联火箭形态:

1)发动机的推力进步缓慢,导致火箭载荷提升受限。根据统计,液体火箭发动机的推力提升较为缓慢,SpaceX于2005年推出的Merlin 1A单发海平面推力为33.1吨,而2018年推出的Merlin 1D+为77.2吨。可以看出经过十年的迭代更新,梅林系列发动机的推力仅增长一倍,发动机的推力提升是一个相对艰难和缓慢的过程。

2)在火箭载荷需求提升与火箭发动机推力提升缓慢的矛盾之下,燃烧室温度的提升和更多组发动机并联工作成为了商业航天火箭公司主要考虑的解决方案。这其中便涉及到更多新材料、新工艺和新结构的应用:
燃烧室温度提升:燃烧室核心温度的提升将显著改善发动机的燃烧效率,进而提升发动机推重比。而随着可回收火箭的出现,发动机的单机价值量更高,带来更耐高温、高导热的材料以及更复杂的工艺如增材制造、热等静压等;
宽口径多并联火箭:宽口径火箭的背景下,多台发动机并联成为可能,而宽口径多并联的商业航天火箭势必需要更大口径的贮箱系统,战略航天多采用4450mm的贮箱口径,而随着更宽口径的贮箱要求变多,对焊接工艺有了更高的要求,使用传统熔焊工艺容易形成面外变形甚至出现失稳变形,进而影响后续绝热材料与外壁的贴合和装配,因此目前行业内已经有部分公司采用其他焊接方法来加工贮箱,将立式装焊与搅拌摩擦焊相结合,从而减少了焊接变形,提高了加工效率。
1.4.3
液体火箭发动机发展迅速
火箭的技术路线较为多样化,目前各国火箭技术路线发展仍处于多路线并进的局面。根据推进剂形态的不同,目前主流的火箭可分为液体推进剂火箭、固体推进剂火箭:
固体火箭:采用固态物质作为推进剂,较常用的固体推进剂是由氧化剂、燃料和轻金属等组成的复合推进剂。固体火箭发动机由固体推进剂药柱、燃烧室壳体、喷管和点火装置组成。由于固体推进剂无需贮存和输送,推进剂可贮存在发动机燃烧室内,因此发射响应时间较快且技术简单;但其短板也同样突出,即比冲较小、推力无法调节等;
液体火箭:采用液体推进剂,推进剂主流方案为液氧/煤油与液氧/甲烷。液体火箭发动机由推力室、推进剂输送系统和发动机控制系统等组成。由于液体推进剂活性比较强,不容易存储,一般在使用前才进行加注,这会拉长火箭的发射周期;但由于液体推进剂燃烧时效率更高,因此液体火箭发动机比冲较大,在相同的载荷下,液体火箭较固体火箭具备更强的运载能力。此外,液体火箭发动机也更易进行启动、关机及调节推力,还具备使用寿命长、造价较低等优势,是目前应用最广泛的火箭发动机。
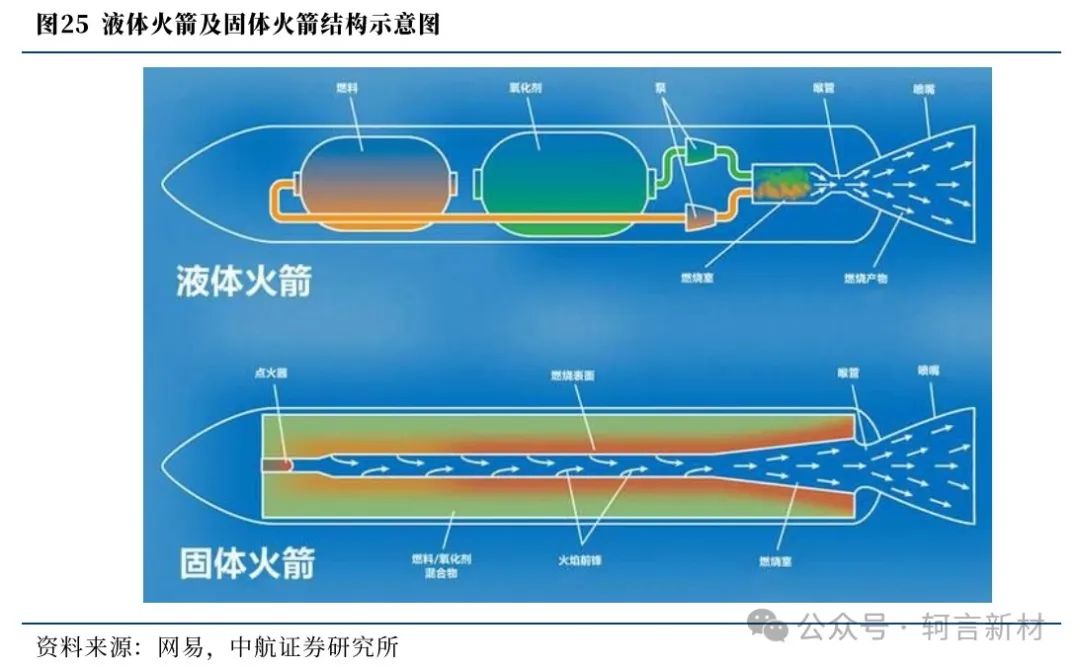
随着可重复使用运载技术的发展,主流的推进剂方案逐渐偏向于液体推进。当前应用最为广泛的三种搭配方案包括“液氧+液氢”、“液氧+煤油”和“液氧+甲烷”:
液氧+液氢:液氢的热值较高,因此该方案是目前人类已知的最大燃料推进方案。理论上来说,发动机可以产生最高463秒的理论真空比冲值。然而,这种推进剂需要低温贮存,加上液氢本身占据的空间较大,从而导致火箭燃料箱和氧化剂箱体的制造变得极为复杂,因此成本较高的液氧液氢方案无法适用于商业航天领域;
液氧+煤油:是目前的主流方案,其最大的优点在于贮存方便、容易获取,燃料成本容易把控。但采用这种方案的发动机最主要的缺陷在于煤油燃烧后会产生大量的积碳,这使得回收发动机的维护成本较高。同时发动机使用寿命偏短,比冲性能偏低,如果商业航天的目标是可重复利用的循环发射,那么液氧煤油发动机存在一定的局限性;
液氧+甲烷:甲烷的制备成本较低,比冲值与液氧煤油相差不多,且液氧甲烷发动机的后端回收维护成本较液氧煤油更低,使得液氧甲烷方案有隐隐赶超液氧煤油之势。同时,采用液氧甲烷方案能省去火箭复杂的结构设计,近年来也被越来越多的专家和企业所重视。目前液氧甲烷发动机的发展主要受制于制造水平、密封性能等技术成熟度限制,亟待新材料、新工艺解决。

不同的推进剂方案需要性能各异的贮箱材料应用来贴合。通过观察SpaceX在猎鹰与星舰系列上的贮箱材料应用情况,可以发现猎鹰9号主要采用铝合金材料,而星舰则采用了不锈钢材料。行业内对此有多种解释,但有一种说法颇具说服力:在使用煤油作为推进剂时,贮箱对温度的需求不高,因此采用液氧煤油发动机的猎鹰9号只需采用铝合金作为贮箱的主要材料即可;而在使用液体甲烷作为主推进剂之后,贮箱的温度最低将低至零下80℃左右,不锈钢材料在低温环境下力学性能等方面较铝合金有较大的优势,加工方式也较为简单,且星舰大推力的特性可以很有效的克服不锈钢密度较大的缺陷,因此星舰的贮箱材料采用了不锈钢。综合考虑发动机推力和贮箱性能等因素,我们判断未来可能会有更多的液体甲烷火箭贮箱采用不锈钢材料。

1.4.4
小结
综上所述,在火箭的可复用运载技术持续发展、发动机推力持续提升和液体火箭发动机的应用趋势下,相关的材料和工艺需求变化值得关注:①可复用火箭的应用在一定程度上降低了材料的易耗属性,但可复用技术对材料应用提出了更高的要求,因此相关材料和工艺也具备了更高的壁垒和价值;②大推力火箭对发动机的燃烧室温度以及宽口径火箭提出了要求,因此传统焊接工艺或将发生变革;③液体火箭中推进剂的不同也会带来贮箱材料的应用区别。在上述背景下,火箭制造环节有望随下游市场天花板的抬升而迎来新的发展契机,以下我们将对商业航天产业所涉及到的部分典型新材料和新工艺展开进一步剖析。
二、新材料助力发动机性能提升
在本文的第一章节中,我们重点提到了火箭需要一颗强大的心脏,航天发动机对于火箭发射的可靠度有着不言而喻的重要性。而发动机燃烧效率最核心的要素就是发动机燃烧室的升温比,燃烧室温度越高,燃烧越充分,推力越大。因此商业航天火箭发动机所需的材料中,最核心的就是耐高温材料,在本节中我们将重点介绍发动机用铜合金材料以及热障涂层材料的应用现况,并对未来市场空间作出展望。
2.1
推力室内壁用铜合金持续迭代
推力室是决定液体火箭发动机工作可靠性的重要核心部件之一。液体火箭发动机一般由推力室、推进剂供应系统、发动机控制系统组成,核心部件包括推力室、涡轮泵、燃气发生器、火药启动器、各种阀门和调节器、机架等。其中,液体火箭推力室由推进剂喷嘴、燃烧室、喷管组件等部件组成,是将液体推进剂的化学能转变成推进力的重要组件,推进剂通过喷注器注入燃烧室,经雾化,蒸发,混合和燃烧产生高温高压燃气,以高速从喷管中冲出而产生推力。
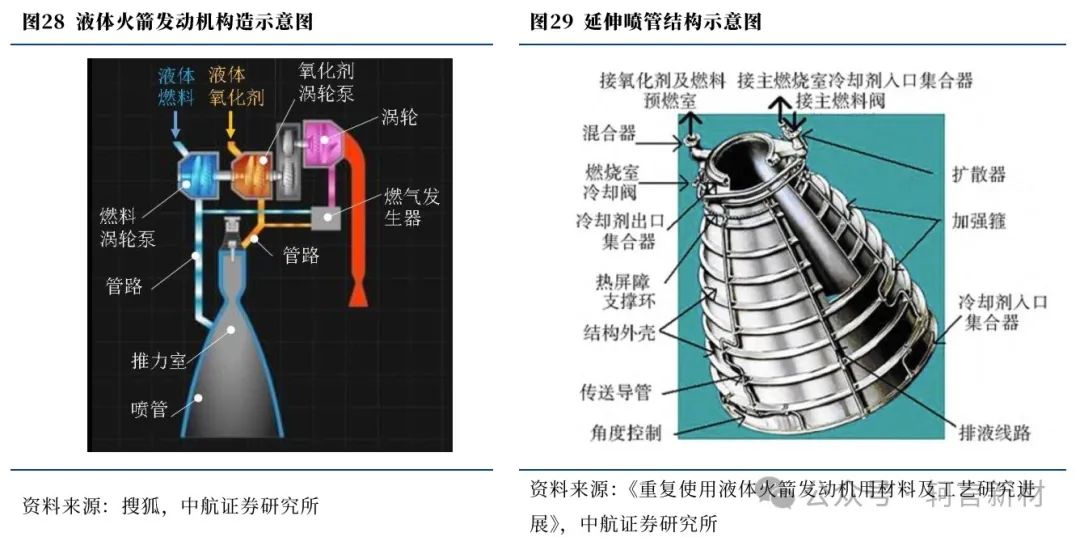
推力室内壁材料需在高温下长期服役,材料内外两侧分别是高温燃气环境和低温冷却环境,且使用的燃料和助燃剂具有腐蚀性,在高温高压及高速燃气冲蚀下对材料的腐蚀极其严重。如此极端的工作环境对材料提出了多方面的要求:①燃烧室内壁温度超过1000℃,喉部燃烧温度高达3500℃,这要求推力室内壁材料具有良好的耐高温性、热导率,将火箭发射过程中燃料燃烧的热量导出,以确保发动机正常工作。若无法将热量导出,则会引起材料过热、过烧,引起材料塑性、冲击韧性、疲劳及耐高温燃气腐蚀性能急剧下降,从而导致部件失效。②燃烧室内压力可达200大气压(约20MPa),故对结构材料的组织稳定性、机械稳定性提出了要求;③液体推进剂具有氧化性或腐蚀性,叠加高温高压及高速燃气的冲蚀也会对材料造成侵蚀,因此材料需具备抗高温氧化、燃气冲蚀性能;④材料的热疲劳极限循环寿命是影响材料重复使用的重要因素,因此材料还需具备较高的低周热疲劳性能。
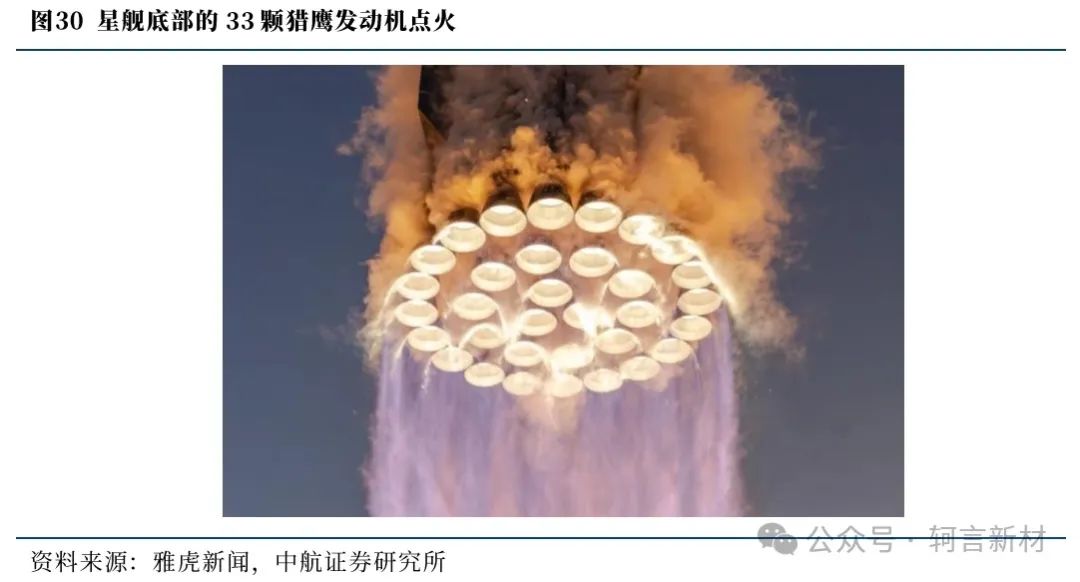
根据上述要求,火箭推力室内壁材料需具备较好的综合性能,而非满足单一条件即可。以下几类材料性能可拿来进行类比:考虑到需在高温下具有较高强度的材料,例如γ″增强的镍基合金,在室温下屈服强度和抗拉强度较高,但较难满足导热条件。纯铜材料在高温下具有较高的电导率、热导率,但是其抗拉强度相对较低。氧化物弥散强化合金(ODS)具有较好的组织稳定性,其强度很高,但塑性很差。钨、钼基合金,具有较高的熔点和耐高温特性,但是这些合金密度极高,考虑到发射成本和条件,其在火箭上的应用较为受限。

经过热处理工艺的铜合金材料能够兼具上述所需的材料强度、热导率、抗氧化性、低周热疲劳性等条件。如上所述,纯铜的屈服强度和抗拉强度相对较低是其主要弱点,但可以通过加入其他合金元素及特殊工艺处理来强化合金的物理性能。虽然这会降低材料的电导率,但仍然符合推力室内壁材料的选材条件。铜合金由于具备与氧的相容性、高热导率、高熔点等优异性能,在一众材料中脱颖而出。值得注意的是,在推力室内壁的实际应用中,由于铜合金抗腐蚀及高温承载能力相对有限,为提高材料应用上限,一般还会采用涂/镀层工艺来降低内壁基体结构工作温度、提高抗腐蚀及抗冲刷性能。得益于上述特性,国内外液体火箭发动机推力室材料的研究重点也因此聚焦于不同成分、不同工艺制成的铜合金材料,从而持续推动材料的更新迭代。
2.1.2
铜合金材料持续更替
海外对航天应用材料的研究和实践起步较早,欧美等在火箭发动机内壁材料方面研究较为广泛。氢氧发动机因其比冲性能高、燃烧稳定性好及绿色环保等优点,一直是国内外运载火箭动力系统发展的重点。早在20世纪70年代,美国国家航空航天局(NASA)便针对氢氧火箭发动机开展了无氧铜、铜锆合金和银锆铜合金三种内壁材料的圆柱形推力室低周热疲劳试验。热试结果表明,三种内壁材料中银锆铜合金的抗拉强度和屈服强度虽略低于铜锆合金,但其高温强度与导热率和铜锆合金接近,是无氧铜的2倍多;同时银锆铜合金在三者中具有最好的循环寿命,其热疲劳循环次数是铜锆合金的1.6倍。

银锆铜合金(NARloy-Z)因其优异的低周热疲劳寿命而被应用于多款可重复使用液体火箭发动机推力室内壁。NARloy-Z为含3%Ag和0.5%Zr的银锆铜合金,由美国洛克达因公司开发,其兼具高导热性和高强度,既具有铜合金的高导热性,又因Ag、Zr合金元素的添加而改善了其高温强度,因此可专门用来制造推力室内壁及具有类似性能要求的部件。银锆铜合金在多款典型的可重复使用液体火箭发动机推力室内壁中均有应用:美国的梅林1C/1D发动机、SSME、RS-68/A、欧空局的火神系列发动机、日本的LE系列发动机等均采用了银锆铜合金作为内壁材料。

弥散强化型铜铬铌合金为最新一代火箭发动机推力室内壁材料。随着合金制备方法的多样化,美国NASA在2005年推出了一种弥散沉淀强化型新材料——铜铬铌合金(GRCop-84)。铜铬铌合金中的Cr和Nb能形成具有耐高温、高硬度的Cr2Nb相,在超过1600℃时仍然稳定,这使得铜铬铌合金不仅有较好的高温稳定性和热导率,还具有非常好的高温抗氧化性、室温/高温强度、及抗蠕变、抗热腐蚀等能力。
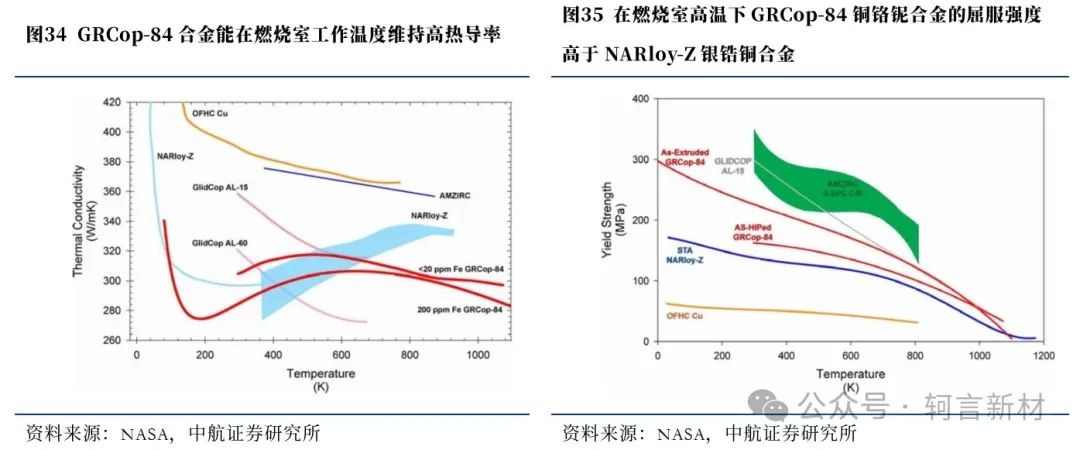
至此,液体火箭发动机内壁材料经历了4个发展阶段:不锈钢—锆铜合金(Amzirc)—银锆铜合金(NARloy-Z)—铜铬铌合金(GRCop-84)。其中铜铬铌合金作为第四代高强高导高耐热合金,有望逐步取代银锆铜合金,应用于火箭发动机推力室内壁。

除了上述材料外,学术界和产业界也都在持续探索特种铜合金材料的各个分支,以寻找契合推力室应用需求的新材料,其中铬锆铜合金因优异的力学性能和导热性而在近年来得到了落地应用。随着对铜合金材料的研究推进,人们发现铬锆铜合金(CuCrZr)不仅具有优良的综合力学性能和物理性能,还具有高强度、高导电率、良好的塑性、高效的热传导性和冷却效果,贴合火箭发动机零部件应用需求。日本将自研的铬锆铜合金用于H2火箭发动机中,我国部分商业航天民营企业在近年来也开始采用铬锆铜推力室内壁方案,主要由于铬锆铜合金优越的热导率和强度以及较低的热膨胀系数能够契合发动机材料应用需求。
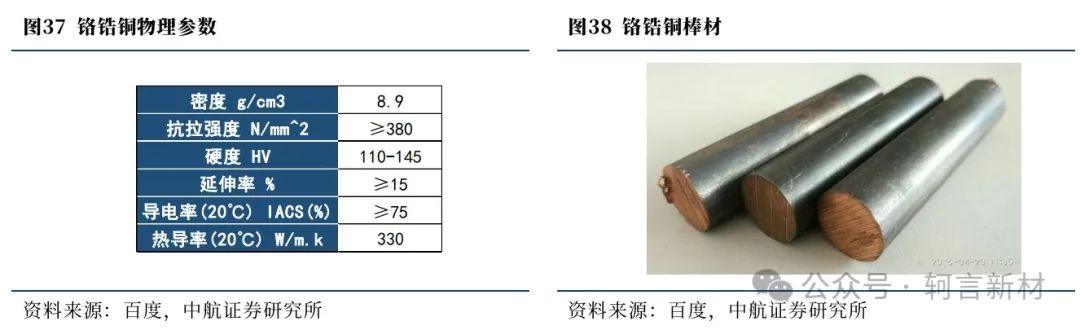
国内可重复使用火箭技术仍处发展前期阶段,铜合金材料研用代差仍存。从当前国内对火箭发动机推力室材料的研究进展来看,由于我国液体火箭发动机一般以满足运载火箭一次性使用为设计目的,追求最高的性能和推重比是发动机设计的目标,零组件的疲劳尤其是高周疲劳问题一般不作重点考虑,因此国内对材料及相关工艺技术的研究与海外存在代差。当前国内推力室内壁材料仍然以第二代锆铜(Amzirc)合金为主,国外使用已久的第三代银锆铜合金热疲劳性能是铜锆合金的1.6倍,对比之下,国内关键材料体系与国外相应材料体系相差一到两代。但随着以航天科技八院为代表的国家队,以及以蓝箭航天为代表的商业航天公司陆续带头开展10km级VTVL试验,火箭的可复用技术发展被提上日程,相关的材料研究和应用也受到了越来越多的重视。
2.1.3
行业准入壁垒较高,发展前景广阔
铜合金材料的制备及推力室内壁产品的生产均处于火箭发动机产业链上游。铜合金推力室内壁主要由耐高温高导热铜合金材料的设计&制备、3D打印或锻造旋压、精密加工及组装焊接等产业环节构成,具备较高的技术壁垒。由于推力室内壁产品的生产需具备工艺技术成熟、质量性能可靠、供应链的稳定保证、可持续发展等特点,因此该环节也具备较高的市场准入条件。海外对推力室用铜合金材料研发及生产环节参与度较高的企业主要包括美国NASA、法国铜合金集团(Lebronze Aalloys)等,国内参与者主要为斯瑞新材:
美国NASA是世界上最权威的航空航天科研机构。作为美国联邦政府的行政性科研机构,NASA负责制定、实施美国的太空计划,并开展航空科学暨太空科学的研究。NASA具备完善的航天发动机及材料研究中心,自上世纪起便引领了火箭发动机用铜合金牌号的更新迭代,其在特种铜合金材料研发领域占据先行者地位;

法国铜合金集团是一家专门生产高性能铜合金、镍基合金产品的工业集团。公司已在航空航天工业特种铜合金行业深耕50余年,目前可为多类机型、火箭、卫星制造商提供产品解决方案,具备火箭发动机用铜合金材料的定制化供应能力;

当前国内液体火箭发动机推力室产品主要供应商为中国航天科技集团、中国航天科工集团等国营企业,优先供应深空探测、载人航天等重大国家太空项目的需求,但仍难以满足未来商业航天发展的需要。斯瑞新材作为火箭推力室内壁行业的民营龙头企业,拥有高强高导铜合金制造的核心技术和关键装备,具备为客户提供规模化、性能优异的推力室内壁产品的能力。
我国商业航天产业尚处于初期发展阶段,产业链供应尚未充分发展,铜合金推力室内壁产品的技术成熟度和产能规模仍有大幅提升空间。由于先前我国火箭研发制造目标一般为满足运载火箭的一次性使用,国内重复使用运载技术较美国仍有较大差距。随着越来越多的民营商业航天企业开启了VTVL回收试验进程,未来国内火箭发射也将步入可重复使用时代,与之相对应的是应用材料性能要求的大幅提升。在此背景下,铜合金推力室内壁的产品成熟度需通过材料的产学研用及生产工艺的改进完善来提升,填补国内外材料代差刻不容缓。国内以铜铬铌材料为代表的推力室内壁产品需求量有望随火箭应用材料需求的推进而迎来从0到1的增长,相关企业需突破产能瓶颈以满足下游市场的快速扩容。
2.1.4
市场空间测算
对于全球火箭发动机用铜合金组件市场需求,我们可根据卫星发射需求量、单台发动机对应卫星载荷、发动机可复用次数及铜合金组件价值量来推算铜合金组件市场空间。我们对2025-2030年期间商业航天领域中铜合金组件产品的应用场景做出以下假设条件:
根据中航证券军工组队我们预计,在悲观、中性、乐观情况下,2025-2030年国内卫星发射需求量分别为6307、8410、10512颗,海外卫星发射需求量分别为41000、45000、49000颗;
假设单台发动机对应的卫星载荷数量均为2颗;
鉴于我国火箭可复用技术尚未成熟,发动机复用次数暂时不计入考虑;假设海外发动机复用次数为15次;
国内火箭发动机以锆铜、铬锆铜材料为主,假设单台发动机中铜合金组件价值量约为40万元/套;国外火箭发动机以铜铬铌、铬锆铜材料为主,由于铜铬铌材料具备更高的价值量,我们假设单台发动机中铜合金组件价值量约为120万元/套;
根据以上假设条件计算得出,2025-2030年期间全球商业航天领域铜合金市场空间在不同情境假设下分别为29.0、34.8、40.6亿元。
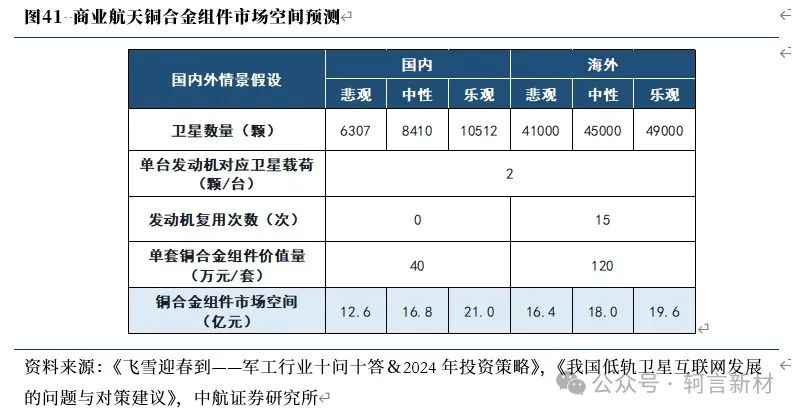
2.2
热障涂层应用前景广阔
2.2.1
基本介绍及历史沿革
随着航天技术的不断发展,航天发动机开始向着更高推重比、更高燃料使用效率发展,尤其是近两年可回收火箭概念的提出,航天发动机的使用寿命也成为了重要议题。为实现上述目的,更高的燃烧温度和二次加力燃烧室的使用将成为重要的发展方向。为了保证部件在高温环境下长时间稳定工作,通常的做法是采用耐1000℃以上高温的高温合金作为主材料,由于一般涡轮的温度高达2200K,因此只能通过在部件内开设导气通道,通过再生冷却的方式将温度降低到极限使用温度以下,目前受到镍基高温合金熔点限制,燃烧室和二次加力燃烧室的温度提高越来越困难。为解决这一难题,美国国家航空航天局于20世纪50年代提出了热障涂层(TBCs)概念。

热障涂层是指将具有高耐热性、高抗腐蚀性以及低导热率的陶瓷材料以涂层的形式覆盖在热端部件表面的一种热防护技术。作为一种复杂的多层涂层,可以在一定程度上阻止燃气温度向基体材料传递,降低基体工作温度,从而保障热端部件在高温环境的稳定运行。传统的热障涂层主要包括了四个部分:镍基高温合金基材、金属黏结层、顶部陶瓷层以及在高温环境中生长的热生长氧化物层。其中镍基高温合金基材是主要的基础材料,承担应力;金属黏结层作为顶部陶瓷层和高温合金基底的中间层,不仅能提高基底材料与顶部面漆之间的结合能力,还能保护基底不被氧化;顶部陶瓷层起到隔热以及防腐蚀的作用。目前氧化钇稳定氧化锆(YSZ)因其优异的隔热性能、较高的热膨胀系数与断裂韧性,150μm的涂层最高可以提供170℃的降温效果,因此成为使用最为广泛的热障涂层陶瓷顶层材料。

热障涂层的提出和发展建立在航空工业对于“更快、更高、更强”的要求上:1)起源:热障涂层的研究起源于20世纪40年代末至50年代初,首次应用是60年代。美国国家航空航天局(NASA)将热障涂层应用于试验机型X-15的发动机喷管和燃烧室。2)发展:70年代后期,在J75发动机燃烧室应用的等离子喷涂热障涂层标志着第一代涂层的诞生。20世纪80年代,美国普惠公司成功研发的第二代等离子喷涂(PS)热障涂层PWA264首先在JT9D发动机的涡轮中应用。随后普惠公司使用第三代热障涂层PWA266采用的是低压等离子喷涂技术,这一代热障涂层将涡轮叶片的耐温极限提升了150K左右。3)高潮:20世纪,各国都在积极研究热障涂层的设计和制备,并大量应用于发动机热端部件中,进入21世纪,热障涂层的工艺逐步成熟并广泛应用,美国几乎大部分民用、军用发动机都使用了热障涂层技术。
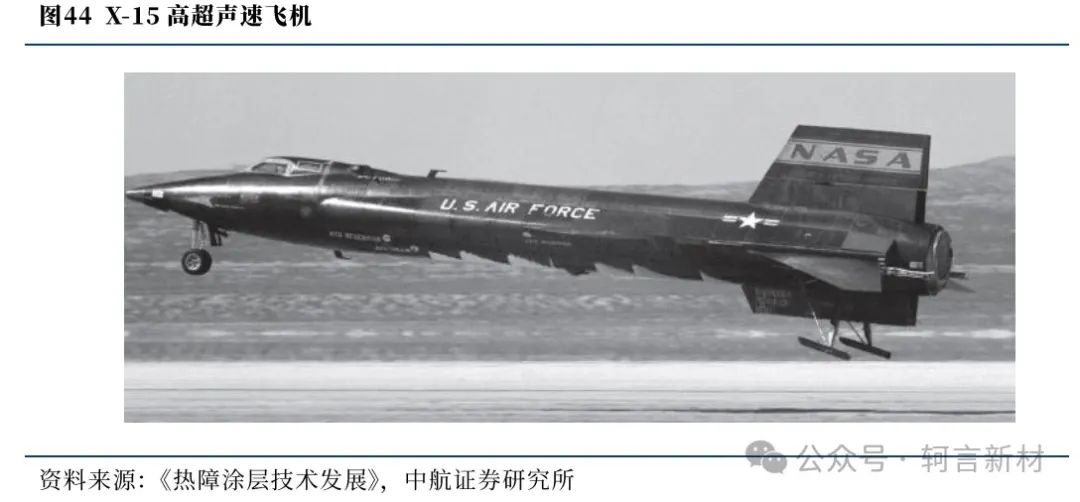
在航天领域,热障涂层的应用开始逐步增多,包括火箭发动机的热端部件、航天热保护系统、姿态控制发动机等等,已经或潜在有可能使用热障涂层作为一种热防护的材料来保护基材。这主要是由于热障涂层的耐温极限的不断提升、可回收可复用火箭技术的出现以及热障涂层工艺的成熟和成本的降低推动所致。相信随着上述利好因素的不断扩大,热障涂层在航天领域的应用前景广阔。
2.2.2
工艺路线多元,三大技术趋势明显
热障涂层的制备主要是将颗粒状的金属或陶瓷材料熔化后均匀的覆盖在基体表面,形成具有隔热特性的涂层。目前已有的热障涂层制备技术包括激光重熔(LR)、化学气相沉积(CVD)、等离子喷涂(PS)和电子束物理气相沉积(EB-PVD)等方法,综合来看,等离子喷涂和电子束物理沉积综合性能最高,目前使用最为广泛。
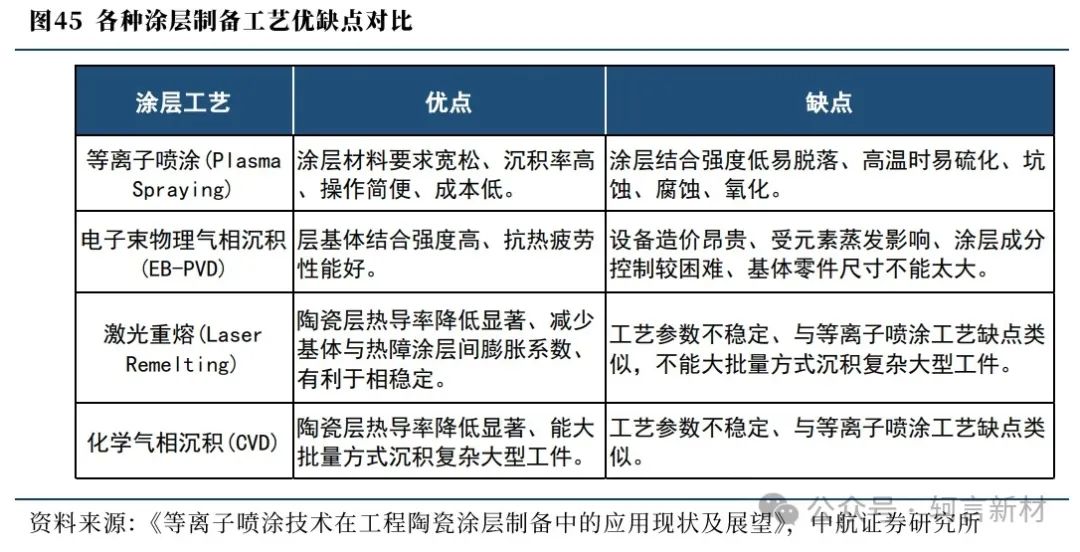
等离子喷涂(PS)应用于热障涂层制备始于20世纪50年代末,其工作原理是利用等离子弧发生器(喷枪)将通入喷嘴内的气体加热电离,形成高温高速的等离子流,等离子流将粉末加热到熔化的状态,然后通过高速焰流喷射到预处理件表面,快速凝固后形成热障涂层。等离子喷涂主要分为大气等离子喷涂技术(APS)和低压等离子喷涂技术(VPS),其中APS应用陶瓷层的制备,而VPS主要制备黏结层。等离子喷涂具有喷涂用料适用范围广、致密度和强度高等特点,因此是所有热喷涂工艺中适用性最广的喷涂方法。

电子束物理气相沉积技术(EB-PVD)是在真空状态下,以聚焦的高能电子束为热源将金属或陶瓷材料置于水冷坩埚中加热熔化至蒸发,然后在偏转磁场的作用下将气相的涂层材料沉积在基体上形成的热障涂层。EB-PVD蒸发速率高,几乎可以蒸发所有物质,且其沉积得到的涂层与基体的结合力比较好。相比于APS涂层,EB-PVD涂层的柱状晶体结构具有更高的应变容限、涂层更加致密且有更高的结合力,从而具有更高的热循环寿命、更好的抗氧化和抗热腐蚀性能,但其成本较高。
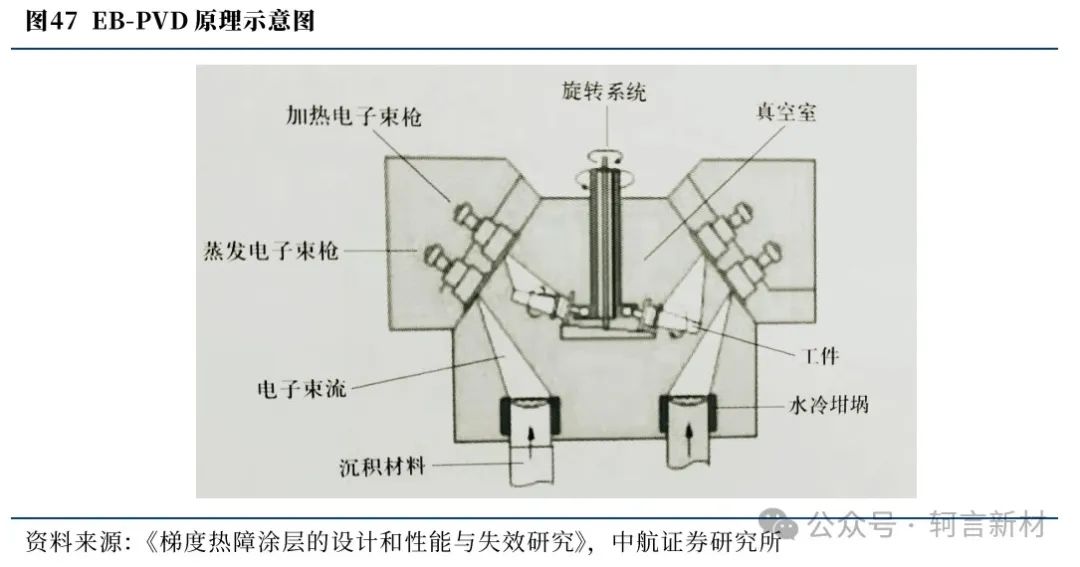
目前产业链主要涉及喷涂设备、喷涂服务以及下游部件客户等多个环节。主要商业模式是中游零部件加工后,交由热喷涂服务企业进行热障涂层工作,随后由零部件企业确认质量后交付给下游总装企业进行装配。因此热喷涂服务大多涉及到保密资质,取得军工资质证明的企业具有较大的优势,并且部分下游企业也会要求该环节的企业负责部分中游零部件加工方面的工作,代表企业包括华秦科技、新劲刚等;而上游的粉末供应商主要是研究所或者是大型集团下属的子公司,典型的如北矿科技集团下属子公司北矿新材和中钢集团下属子公司中钢洛耐等;设备方面,金轮坤天等具有热喷涂设备制造能力的企业占据核心地位。

近年来,随着科研人员对热障涂层的研究逐步深入以及下游应用行业对于热障涂层的性能要求发生变化,热障涂层整体呈现出三大趋势:
结构/功能一体化:热障涂层的应用目前正在从简单的在热端部件表面进行喷涂和固化向结构/功能一体化的热障涂层部件转化,这意味着从部件层面,部件的结构设计的重构以及喷涂工艺的颠覆。但目前热障涂层的喷涂仍然受制于喷头的角度、工艺的难度以及产业链分工等多方面影响。未来,随着设计端更加一体化、更加复杂化的设计要求出现,从部件制造到涂层制造的一体化企业出现,热障涂层的结构/功能一体化将成为可能;
硅基非氧化物陶瓷逐步应用:在发动机燃烧室温度要求逐步提高的情况下,热端部件表面温度将达到1400℃以上,这大大超高了现有镍基高温合金的耐温极限,因此硅基非氧化物陶瓷成为研究重点。区别于传统的氧化物陶瓷,硅基陶瓷具有耐高温、热导率高、耐化学腐蚀等特点,因此被应用于高温热端部件中;
环境障涂层崛起:发动机工作环境中,硅基陶瓷的表面稳定性恶化严重,因此环境障涂层成为重要的解决方案。环境障碍涂层与热障涂层并不冲突,热障涂层的主要功能是降低基材的温度,而环境障涂层的主要功能是提高基材在高温下抵抗熔盐和水分侵蚀,提高陶瓷基复材的高温稳定性和耐久性。随着可复用火箭的技术进步,商业航天对火箭发动机的使用寿命提出了更高的要求,因此环境障涂层的需求将逐步提高。
2.2.3
未来市场需求旺盛
根据产业调研,目前热障涂层主要应用于航空发动机的涡轮叶片等反复使用的热端部件上,而战略航天则由于价格高昂、一次性使用等特点,使用热障涂层的必要性和经济性不足而主要是用于空间站和货运飞船,例如天舟四号的大面积复杂部位、前舱门舷窗玻璃等部位。
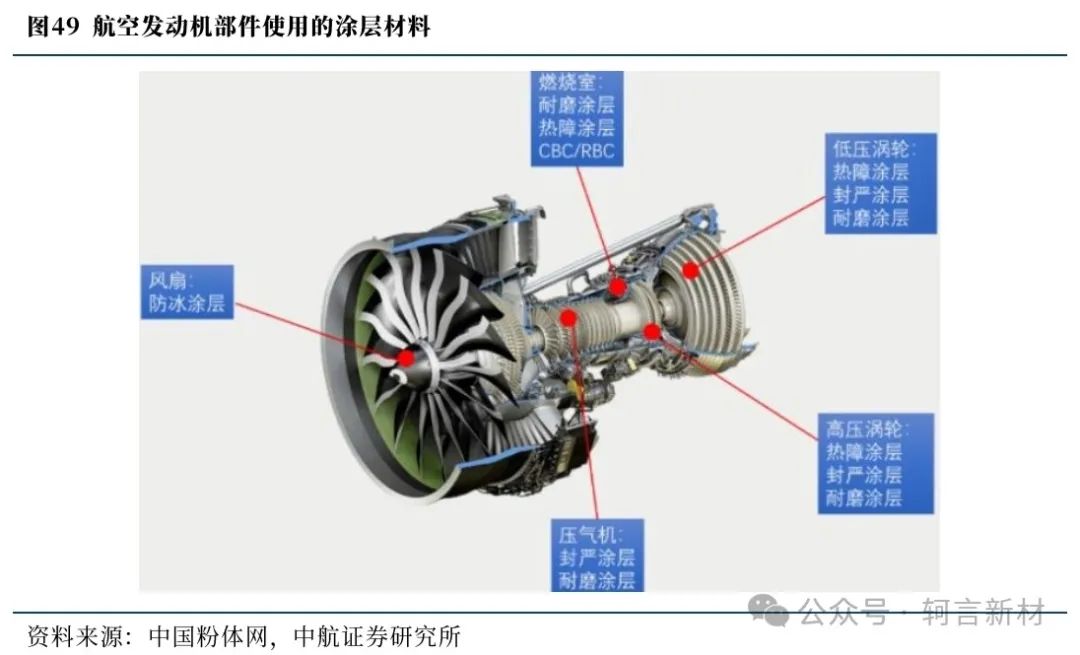
商业航天对飞行器的寿命要求介于航空与战略航天之间。商业航天相较于战略航天的区别是火箭的反复使用及经济性考量,火箭的寿命介于航空和战略航天之间,而热障涂层的使用正在被商业航天客户逐步接受。1997年,欧洲航天局就已经在LRE发动机的设计中考虑采用热障涂层来解决发动机耐温极限的问题。随后,2007年,美国NASA在新一代先进运载火箭技术中也开始采用类似技术。
我们依据悲观、中性、乐观三种情况,对2025-2030年期间国内热障涂层在商业航天领域的应用需求做出假设,假设条件如下:
预计国内卫星数量在不同情况下,分别需求量为6307、8410、10512颗;
假设单发火箭的卫星载荷为18颗,对应发动机数量9台;
假设单台发动机热障涂层使用量在三类情形下分别为140、150、160kg/台;
假设热障涂层更新频率分别为0.85、0.9和1次/发;
假设热障涂层的价值量在三类情形下分别为5500、6000、6500元/千克;
根据以上假设条件计算得出,在不同情境假设下,2025-2030年期间国内商业航天领域热障涂层材料市场空间分别为20.6、34.1、54.7亿元。
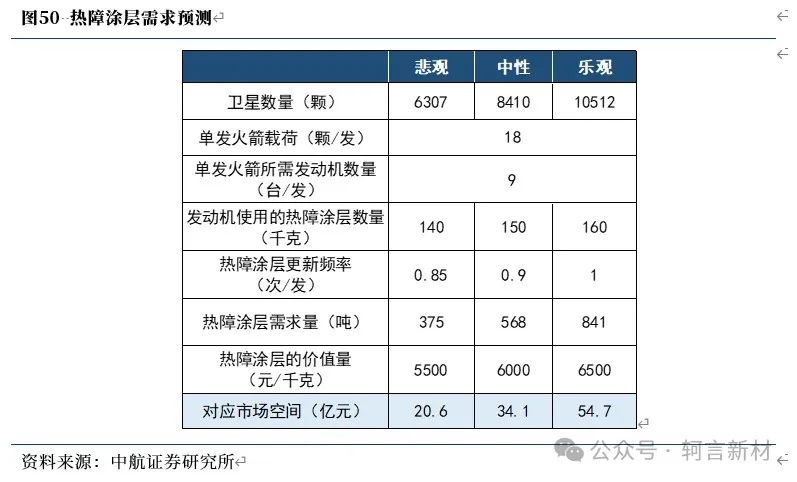
2.3
小结
火箭发动机作为对航天器对抗地心引力的核心,其推力的递增是火箭载荷提升的先决要素,而热端材料的极限性能高度是发动机能否持续提升燃烧效率和推力的关键。特种铜合金材料凭借其优异的力学性能,超越了一众材料,成为了最贴合燃烧室长期服役要求的合金。铜合金材料的迭代升级也逐步满足了现代先进火箭发动机对可复用性能的要求。随着未来火箭发动机向大推力方向不断发展,燃烧室温度的提升将进一步催生具备高温稳定性和高热导率的铜铬铌合金材料的应用,走在材料应用前沿的相关研发制造企业和方案应用者将把握火箭发动机性能跃进的机遇。热障涂层有望助力火箭发动机进一步突破温度的限制,也保护了组件不受高温侵蚀,符合火箭回收利用理念。当前热障涂层的应用范围也逐步从热端部件表面向结构/功能一体化来转化,这意味着部件结构设计的重构以及喷涂工艺的颠覆。相信随着我国商业航天产业的崛起,上游材料端有望受益于产业增量带来的牛鞭效应,从而站上更大的舞台。
三、制造需求引领新工艺变迁
除了涉及到新材料的应用外,商业航天领域中新工艺的应用对零部件的力学性能影响也不可或缺。由于商业航天在商业模式、需求结构等方面与战略航天的定位截然不同,因此对于供应链的需求也完全不同,前者更倾向于在达到性能要求的同时,努力提高性价比、载荷比。结合产业现况,我们将在本节对增材制造和热等静压工艺的应用情况作出分析。
3.1
增材制造的应用不可或缺
3.1.1
三类主要参与者
增材制造的技术路线较多,目前在航天领域中应用较多的工艺包括激光铺粉、激光送粉以及电弧送丝,他们其中大部分都是传统战略航天和军用航空的供应商,根据他们的业务特点,我们将其分为三类:
1)产业链现有参与者:根据产业链参与度,铂力特、飞而康、钢研极光、华曙高科以及威拉里等企业,已经参与到商业航天火箭产业链中。涉及环节包括原材料供应、打印设备制造以及提供打印服务,部分企业已涉足其中多个环节。通过深度参与到下游火箭公司部件的设计、制造中,这些企业在相关领域的收入已经实现了一定规模,发展迅速;
2)进入预研阶段的企业:铺粉工艺目前已经被火箭发动机制造企业接受,并深度参与到上游零部件的制造中。但送粉以及送丝等技术路线尚未在商业航天领域中铺开应用,融速科技、英尼格玛、抚顺东工等电弧送丝工艺为主的企业在该领域的应用主要以产品预研为主。随着增材制造在火箭封头、贮箱等部件接受度的提升,未来电弧送丝技术也有望在火箭制造环节中崭露头角;
3)有潜力的企业:近年来随着航天市场的蓬勃发展,部分为军工体系配套的公司也在商业航天领域跃跃欲试,如鑫精合、苏州倍丰等。相信随着行业规模的扩大,该部分企业也有望随着商业航天领域规模的扩大而一同成长。
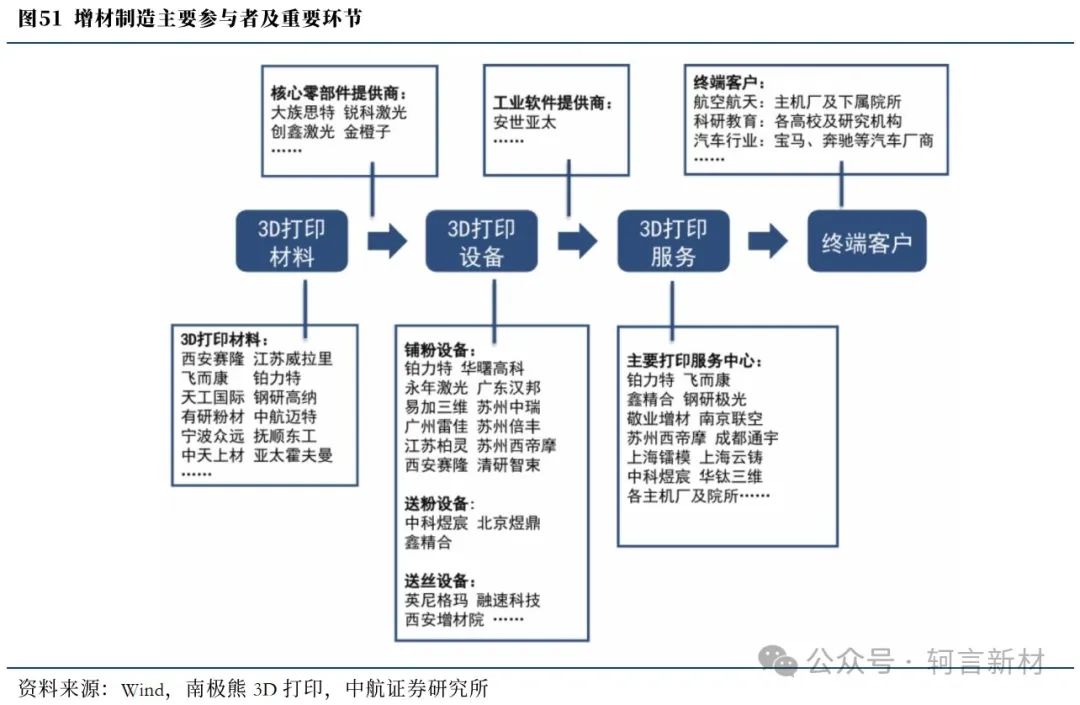
3.1.2
多元需求带来广阔空间
近年来民用航天的兴起带动了航天产业的全面繁荣,金属3D打印完美符合了航天产业多品种、小批量、整体化、轻量化、低成本等需求,在卫星、火箭、发动机多个领域存在较大的增长空间。未来增材制造工艺势必成为商业航天产业中主流加工技术,甚至是某些产品的唯一加工技术:

1)增材制造实现卫星结构减重:2019年8月17日,千乘一号01星作为主星搭载捷龙一号遥一火箭升空,卫星发射入轨圆满成功。千乘一号是目前国际上尺寸最大的增材制造整星结构,使用轻量化的三维点阵结构完成设计,通过铝合金增材制造技术一体化制备,整星历时14个月完成研制,重量65公斤。与传统卫星相比,传统卫星结构承载比20%左右,整星频率70Hz,千乘一号01星结构承载比15%,整星频率110Hz。该卫星采用铂力特的BLT-S600设备打印,内部采用点阵化结构,零件最小特征仅0.5mm,由于整体轮廓尺寸较大,因此整星内有超过100万个点阵结构特征。通过宏细观一体化优化方法设计的千乘一号考虑了整体工艺约束和整星装配约束,实现了点阵材料细观构型和连接结构的创新设计。目前该设计方法已经用于卫星整星结构、相变储能热控结构与有效载荷支架结构,相较于传统的制造工艺,实现了结构减重30-60%;
2)火箭零部件需要增材制造:近年来,随着星链计划的推出以及行业内对航天的重视度提高,火箭发射将朝着高频次方向发展,因此加工的时效性成为了近年来产业的关注重点。传统火箭制造由载荷、制导、推进和结构四个主要系统构成,多年来一直依靠大型工厂、固定工具、复杂供应链以及大量成熟的产业工人,在2年或者更长的时间内完成制造。而如今商业火箭零部件生产商囿于投资久期、发展历史、风险承担能力等因素,难以套用传统火箭的制造体系。3D打印凭借无库存、柔性生产、快速制造、性能优异等优点,完美符合了他们的诉求,在小批量的情况下,成本较重新培育传统供应链具备更大优势,因此3D打印几乎成为商业火箭零部件加工的必选路线;
以3D打印火箭创业公司Relativity Space为例,其将于近期发射首枚全金属3D打印火箭Terran 1,该火箭载荷约1000公斤,火箭采用了两种类型的3D打印技术制造火箭质量90%以上的结构。公司子公司Stargate可以打印直径3.4米、高7.6米的结构件,是目前最大的金属部件。每个Terran 1装备有九台Aeon 1发动机,通过3D打印减少发动机燃烧室、点火器、涡轮泵、推进器等系统内的零部件数量(数千→100个),其可以在60天的时间内制造出Terran 1的发动机。此外,Relativity Space正在开发新一代火箭——Terran R,将一代火箭的有效载荷提升20倍,同时支持可重复使用,这将有力支撑客户对于大型火箭的商业需求。与Terran 1一样,Terran R也将使用3D打印制造90%以上的零部件。3D打印技术将帮助公司力争在20年内实现规模化太空旅行的目标;

贮箱和封头作为火箭箭体价值量最大、技术含量最高的部分,目前已经有部分商业航天企业开始采用3D打印制造封头和贮箱等大尺寸设备。与发动机不同,火箭的封头和贮箱采用大尺寸薄壁厚的加工方法。融速科技使用其自主研发的AMmake R1通过软件工控等方式实现了变位机联动,克服了悬垂筋打印、散差率控制等问题,极大的促进了3D打印在火箭箭体方面的应用进展。
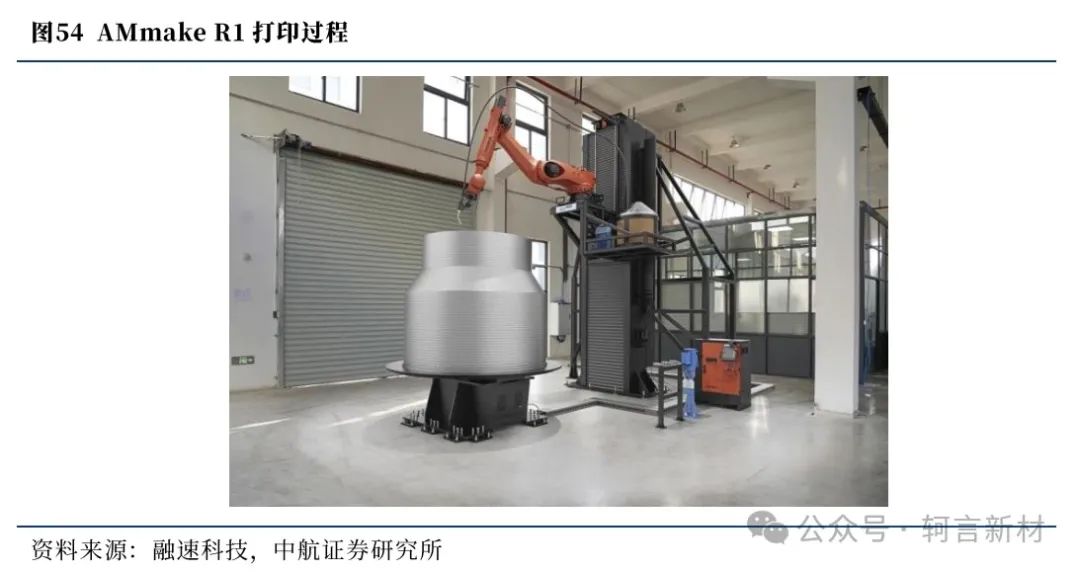
1) 火箭发动机:以SLM(激光选区熔化)为代表的技术正在逐步渗透,如火箭推力室的喷注器、燃烧室以及推力室喷管等部件均有应用。目前火箭发动机公司为了提高核心燃烧室耐温性、提升燃料的燃烧效率,采用再生冷却方法制造发动机内壁。再生冷却是一种提升发动机燃烧效率的工艺,推进剂直接流过推力室内外壁的冷却套,在吸收燃烧室热量的同时实现了推进剂的预热,这既降低了燃烧室温度,又实现了更高的燃烧效率,因此愈发受到重视。使用钎焊方法来制造再生冷却系统成本高、良率低,而3D打印的火箭推力室部件能生产带内流道的薄壁结构,从而实现结构功能一体化,有效解决了再生冷却系统加工困难的问题。火箭发动机燃烧室温度提升推动了再生冷却的需求,带动了内流道设计的兴起,而3D打印可以在成本更低的情况下更快的加工出内流道,因此成为了火箭发动机推力室部件的重要成型工艺。
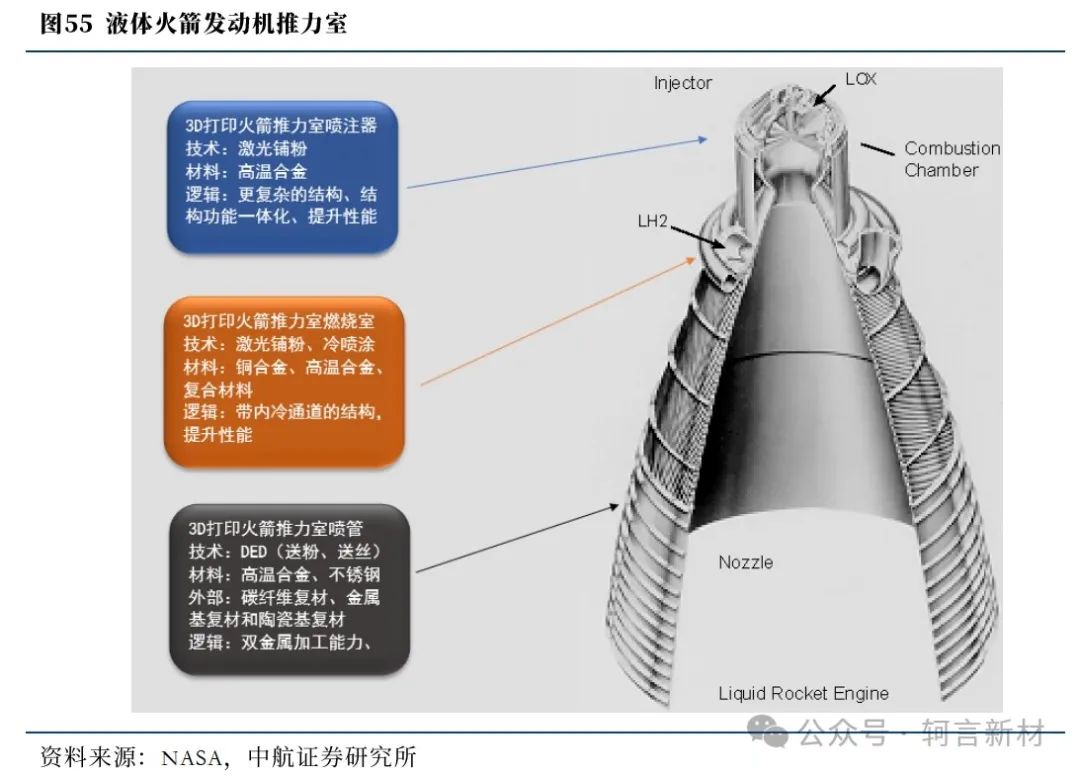
外部简单,内部复杂的3D打印结构:以SpaceX为例,从Raptor1代—3代对比来看,新一代的发动机外部看起来更加简化,很多管线都消失了,一方面是由于早期发动机需要进行大量的调整和检测,另一方面也是由于Raptor3采用了金属3D打印技术,将大量管线整合进发动机中,从而导致了这种外部简单但内部结构复杂的独特设计,充满了工业美感。根据SpaceX数据,单台发动机具备280吨推力与350s的比重,而其自身重量仅1525kg。3D打印的使用使得发动机减重7%,推力较上一代发动机高出了21%,比初代Raptor提高51%。

综合以上三种增材制造在商业航天领域的应用,我们根据情况做出悲观、中性、乐观的假设,以下是假设的条件:
1. 首先是在卫星结构制造中增材制造的市场空间估计:
假设在不同情况下,卫星数量分别为6307、8410、10512颗;
假设在不同情况下,卫星价值量为0.40、0.45、0.50亿元/颗,卫星的结构件价值量占比6%;
假设在不同情况下,增材制造的渗透率为9%、10%、11%。
2、其次是在火箭箭体制造中增材制造的市场空间估计:
在上述假设基础上,单发火箭的载荷为18颗卫星/发;
假设在不同情况下,增材制造在火箭箭体的渗透率为1%、1.2%、1.4%。
3、最后是在火箭发动机部件中增材制造的市场空间估计:
在上述假设基础上,单发火箭的发动机数量为9台/发;
假设在不同情况下,增材制造在每台火箭发动机的价值量分别为250万、300万、350万/台。
根据上述假设,我们预计增材制造在悲观、中性、乐观情况下的市场空间在105、166、240亿元。

3.1.3
低成本大尺寸成为未来发展趋势
增材制造成为火箭发动机制造不可或缺的技术:基于上文,增材制造在火箭中尤其是发动机生产环节的应用范围较广。尤其是在再生冷却系统中,核心设计在于发动机推力室的冷却流道:一方面发动机尺寸较大、壁厚较薄,以便于推进剂的充分预热;另一方面,流道需要气液密封性好,内部结构复杂。这样复杂的需求使用传统工艺只能通过钎焊流道来实现,而采用增材制造工艺可以轻易实现流道的一体成型,这加速了设计的迭代以及发动机性能的提升。
低成本大尺寸成为下阶段目标:下个阶段来看,商业航天对于低成本、大尺寸增材制造部件的需求有望提升。一方面,商业航天更加密集的发射任务以及降本增效的需求使得打印部件的服务企业急需通过工艺改进来实现降本。另一方面,越来越多的部件开始采用增材制造工艺,其中不乏如贮箱、封头等大尺寸部件需要使用送丝工艺制造等案例。未来商业航天的制造工艺或将分为使用低成本、大尺寸以及高效率的送丝工艺用以制造火箭箭体,以及高精度及高复杂性的铺粉工艺用于制造发动机部件等。
3.2
热等静压未来或将大放异彩
热等静压最初主要应用于航空领域,在涡轮盘成型以及粉末冶金成型领域发挥了重要作用。由于可复用技术尚未成熟,因此热等静压部件价值量偏高始终限制着其在航天领域的铺开应用。与增材制造类似,随着可复用技术的推广和商业航天主机厂对于高价值、高性能以及高可靠性的商业航天部件需求愈发旺盛,我们判断未来热等静压无论是作为部件成型抑或是热处理环节,都将在商业航天领域大放异彩。
3.2.1
成型工艺复杂,有效提升部件性能
热等静压(HIP)近净成型技术是几十年来发展起来的新型成形技术。该技术以热等静压设备为基础,通过将粉末加热到一定温度,在高温高压下实现粉末材料的致密和成型。该技术和铸造类似,首先是根据产品结构设计制造包套,再通过各种包套形成类似产品形状的空腔,然后将粉末装入空腔中,经过氩弧焊接后形成密闭空间,通过预留的除气管将密闭空间抽真空,在一定的真空度内进行封焊,然后热等静压处理。高温高压后的粉末经历了粒子重排、塑性变形和扩散蠕变后完全致密,实现了构件成型,然后采取机加或化学方式将包套去除,即可得到热等静压构件。

热等静压经历了几个发展阶段,欧美国家发展较快,我国加速追赶阶段:1)热壁式等静压机:世界上第一台热等静压设备是美国巴特尔研究所为元件的扩散粘接而研制的,由于加热方式是红外马弗炉,因此也被成维热壁式等静压机,2)冷壁式等静压机:随后在1958-1962年,美国通过改变热偶组装方式、电极摆放和容器密封方式,实现了冷壁式等静压,使得粘接效果和粉末冶金致密度大大提升;3)第三阶段主要从1963到1966年,通过使用氦气等传压介质,并利用钢丝缠绕对工件产生预应力,实现工件内部缺陷的减少;4)第四个阶段主要从1967-1969年,热等静压在世界范围内得到认可并得到广泛研究,在这个阶段,碳纤维预制体的热等静压技术逐步成熟,碳化钨零部件得以发展;5)1970-1990s,隔膜式压缩机、非润滑气体压缩机和液体活塞泵逐步应用于热等静压设备,提升了加热效率,高温、高压、大尺寸成为这阶段的主流设计;6)上世纪90年代中期至今,热等静压设备得到极大发展,设备大型化、自动化和低成本化趋势明显,被广泛应用于航空、航天等战略领域,由于涉及到军事领域,因此技术封锁明显,各国发展水平差距巨大。
热等静压近净成型是一个复杂的工艺过程,由于粉末体相对密度只有65%以内,在热等静压成型过程中,粉末会发生30%~40%的体积收缩,在致密化过程中体积收缩和尺寸变化比较大,而包套的不规则变形将引起内外层热传导性能的差异,进一步使得包套收缩过程中的不均匀变形,使得表面产生开裂,因此粉末的收缩均匀性成为了构件能否顺利成型的关键。
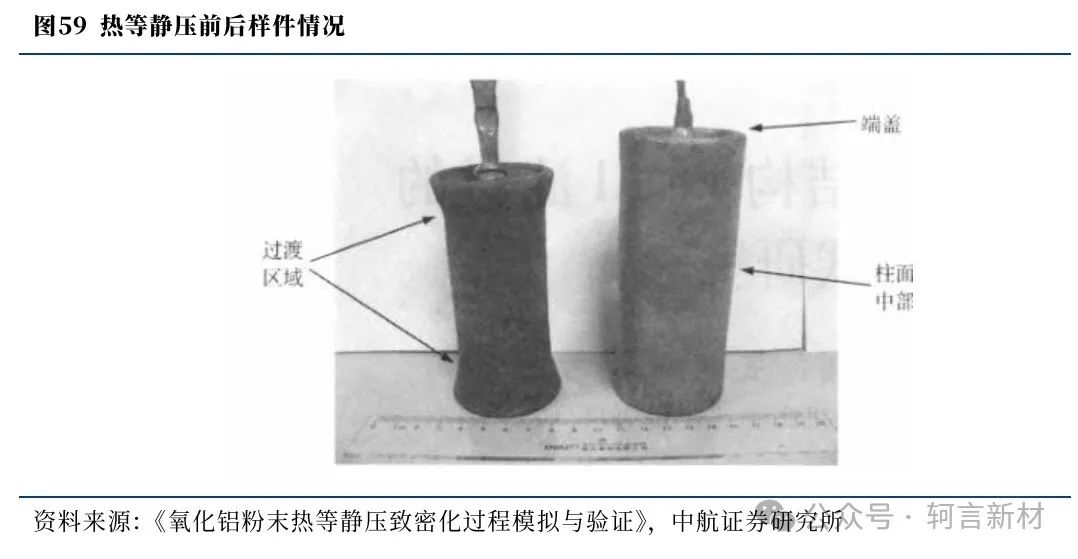
热等静压提升了部件的力学性能。近年来热等静压需求的另一方向,来自于增材制造后端热处理需求。由于增材制造快速成型过程中输入能量不均匀会导致部件存在未融合孔隙,形成一定程度的缺陷。通过热等静压等热处理后,合金组织将部分马氏体组织进一步分解,并且因为高压实现了β晶形态的改变,使得工件内部组织结构更加均匀,能够提高合金的致密度,从而带来更好的力学性能。

3.2.2
欧美较为领先,中企奋起直追
热等静压设备呈现出欧美领先,国内奋起直追的局面。瑞士的著名热等静压企业ABB相关技术储备处于世界领先地位,而我国钢研院主要是从1972年开始研究热等静压技术,目前其子公司钢研昊普最新的产品HIPEX1850主要技术指标已经达到了国际领先水平。此外,还有中航工业川西机器、欧中科技、宁波江丰等多个公司先后研发出热等静压设备。整体来看,由于我国热等静压设备发展起步较晚、国内航空数据积累较少等因素,我国相关技术与欧美差距仍存。
粉末成型方面,我国已取得较大进展。在近年来航空航天旺盛的需求驱动下,北京航材院、航天材料与工艺研究所、中科院研究所以及华中科技大学等科研院校,安吉精铸、天工国际、钢研高纳以及应流股份等企业纷纷投入资源,目前已制成的钛合金热等静压件已经与传统锻件力学性能相当,并且具有较高的精度;
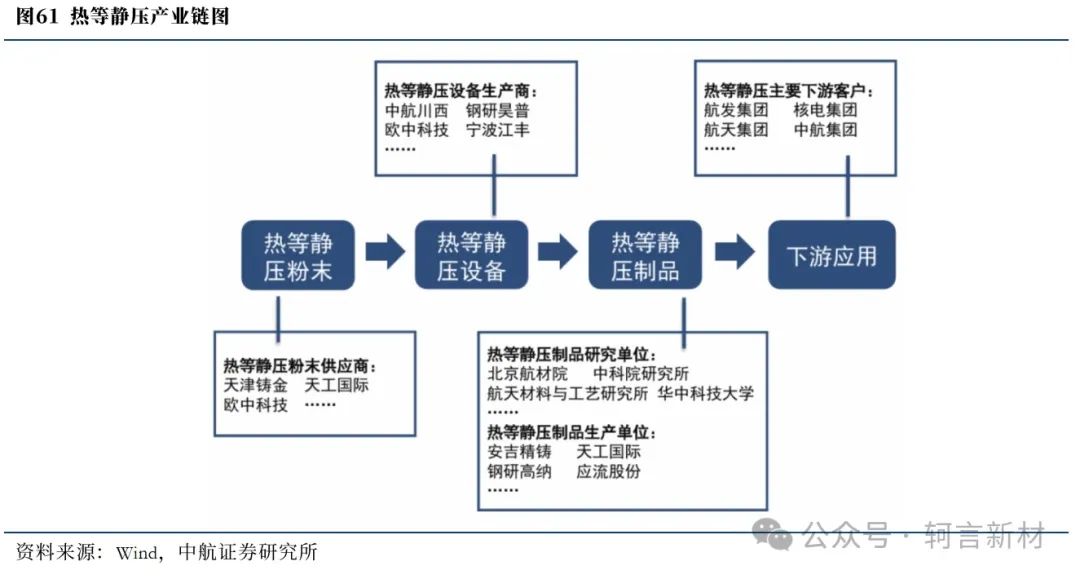
3.2.3
可复用技术推动热等静压需求增长
目前热等静压技术主要应用领域包括航空航天、燃气轮机等。尤其在航空领域,热等静压在航空发动机涡轮盘、压缩机外壳等部件的生产中已得到了成熟应用,粉末热等静压可以实现部件致密化,大大提升涡轮盘等部件的寿命。下图是英国罗罗公司通过热等静压生产的钛合金发动机压缩机外罩,通过计算机模拟和热等静压,实现了部件的高性能、高效率制造。
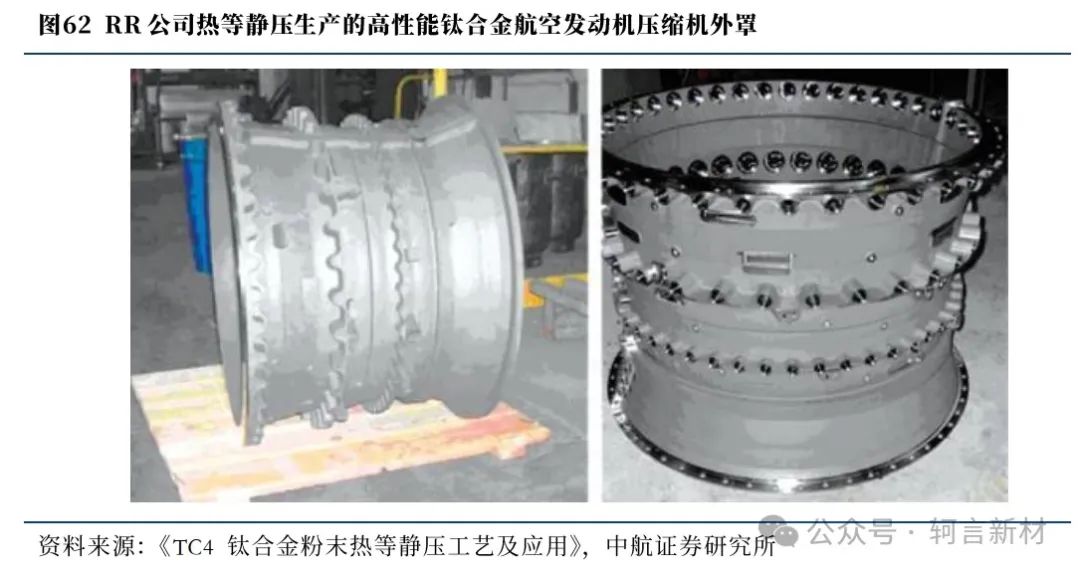
航天领域热等静压方兴未艾。反观传统战略航天领域,热等静压的应用却并不如意,主要应用热等静压成型一些致密碳质结构件,如火箭的舵面和固体火箭发动机的喷管喉衬等。分析原因,我们认为主要是航天领域受制于热等静压部件的价值量较高,传统航天由于无法回收,因此热等静压制件的普及率并不高。随着国内商业航天可复用技术持续推进,且传统战略航天的供应链体系与当前的航天商业化趋势并不兼容,在此背景下热等静压流程短的优势将得到凸显。我们预计,热等静压技术潜在的应用包括火箭发动机喉衬、涡轮盘以及各类动转子等对转动性和致密度要求较高的部件,热等静压在商业航天产业链中的应用面有望持续扩大。
3.3
小结
商业航天最关键的问题是经济性,可复用技术的出现帮助降低了成本,同时较高的载荷也对更高性能的部件提出了要求,这有利于新工艺的拓展应用。增材制造在卫星结构、火箭箭体以及发动机部件中均有应用,而该工艺制造的发动机再生冷却体系极大的提升了燃烧效率,已经成为发动机不可或缺的核心工艺。热等静压工艺目前在航天领域应用较少,相信在可复用技术持续推进的背景下,未来应用有望扩大。与此同时,上述两项工艺又具备短流程的优势,顺应了商业航天对火箭部件快速生产的需求。
四、相关标的推荐
在国内火箭可复用运载技术持续发展、发动机推力持续提升和液体火箭发动机的应用大趋势下,未来液体火箭发动机的升级迭代和火箭制造市场的增长将共同牵动上游新材料和新工艺的应用需求,建议关注以下企业:
火箭发动机用铜合金推力室内壁:斯瑞新材;
热障涂层材料:华秦科技、新劲刚;
增材制造设备及服务:铂力特、华曙高科、钢研极光;
热等静压设备及服务:钢研昊普、欧中科技;
贮箱生产及加工:九天行歌、寰宇航天、超捷股份、融速科技;
其他相关结构件及零部件:超捷股份(阀门)、光威复材(碳纤维制件)、钢研高纳(高温合金铸件)、盛帮股份(橡胶零部件)。
4.1
斯瑞新材
斯瑞新材作为一家新材料研发制造企业,主要致力于铜铬基合金的研发制造,并以此为核心,将技术同心圆拓展至各相关产业领域。公司主要产品包括高强高导铜合金材料及制品、中高压电接触材料及制品、高性能金属铬粉、CT和DR球管零组件、光模块芯片基座/壳体、液体火箭发动机推力室内壁等。公司作为我国铜合金推力室内壁行业的先驱者,已成功将铬锆铜(CuCrZr)为核心的航天级高强高导铜合金材料应用于液体火箭发动机推力室领域,填补了国内技术空白。
目前斯瑞新材已助力蓝箭航天、九州云箭、星际荣耀等商业航天客户完成多次试车、发射、回收,并获得成功。公司的铜合金制品已成功应用于“龙云”、“天鹊”等多款火箭发动机型号,并获得客户认可:
2024年6月23日,航天科技八院进行了我国第一次可回收火箭10公里级VTVL试验,标志着我国商业航天在可重复使用运载火箭技术上取得重大突破。此次飞行试验箭配备了九州云箭公司研发的“龙云”液氧甲烷发动机,是九州云箭推出的首款多次启动、可回收、大推力液体火箭发动机。斯瑞新材为“龙云”发动机的推力室提供了可重复使用的解决方案,并已进入量产阶段。
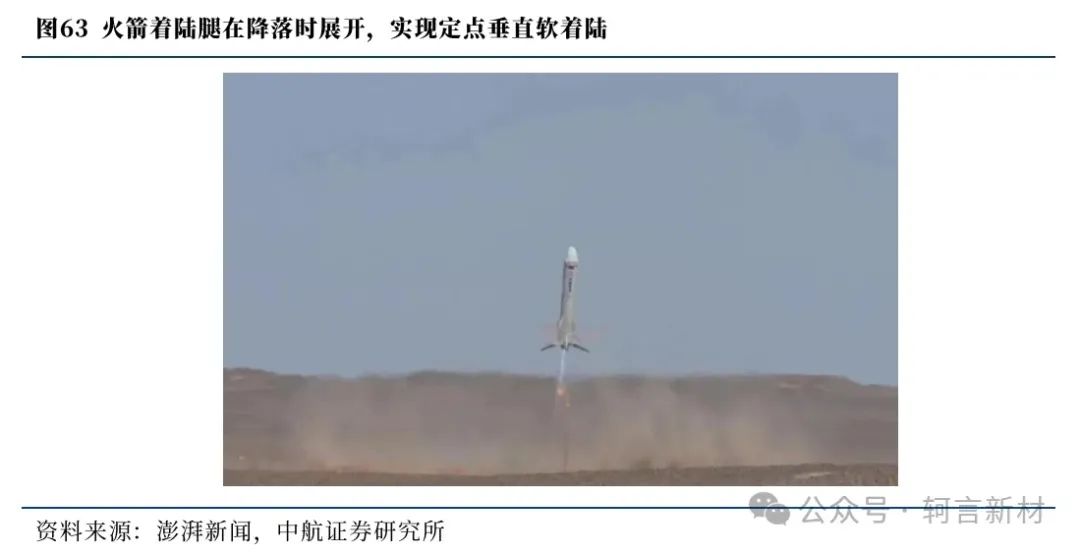
2024年9月11日,由蓝箭航天自主研发的朱雀三号VTVL-1可重复使用垂直起降回收试验箭圆满完成十公里级飞行试验。斯瑞新材为蓝箭航天朱雀三号的“天鹊”改进型号发动机提供了高性能的铜合金材料零组件,这些高强高导耐高温铜合金材料零组件作为火箭发动机燃烧室中的关键部件,确保了火箭在垂直起降过程中的稳定性和安全性。
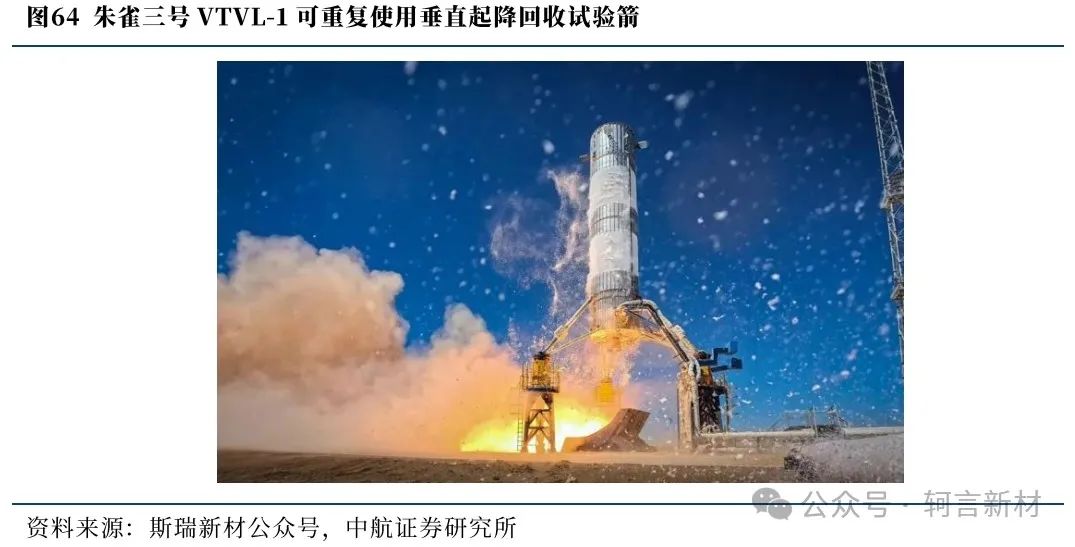
为顺应我国商业航天火箭发射日益增长的需求,斯瑞新材于2024年1月公告称,拟投资5.1亿元于“液体火箭发动机推力室材料、零件、组件产业化项目”。该项目致力打造从材料到制品的“全工艺链能力”,计划购置精密加工设备、扩散焊设备等200台套左右,实现年产约300吨锻件、400套火箭发动机喷注器面板、1100套火箭发动机推力室内壁、外壁等零组件,形成年产销约4.3亿元。公司有望通过该项目来延伸推力室内壁产品产业链,整合不同制造环节,提高市场竞争力,建立该细分领域的“护城河”。公司于2024年中报披露,已开发完成了200吨级液体火箭发动机推力室内壁铜铬铌(CuCrNb)材料制备技术及热等静压技术,未来将致力于打造新一代铜铬铌材料生产能力,以填补我国推力室内壁用铜合金材料与海外的代差,助力火箭发动机产业链实现材料端自主可控。
4.2
华秦科技
华秦科技是特种功能材料制造商,在2019年到2020年分别实现隐身材料及伪装材料的核心型号批产应用,目前公司产品已开始朝着多元化全面发展,参与了多个武器型号特种功能材料的研制任务,围绕着先进新材料产业领域持续深度布局。

多元化布局协同发展:公司围绕新材料产业链,成立了华秦航发、华秦光声、上海瑞华晟等子公司,华秦航发围绕航空发动机产业链布局零部件加工与制造,华秦光声主要从事声学超构材料、声学装备和技术服务,其研发的声学超构材料已进入工程化阶段,上海瑞华晟主营陶瓷基复材,目前正在积极开展项目前期建设工作,力争在2024年下半年实现部分产线试生产。
基于材料研发经验,拓展热防护领域:其中,高效热阻材料(热障涂层)主要应用于耐高温部件,提高了部件的使用寿命。根据招股书披露,公司有两个拍好高效热阻材料处于小批试制阶段,一个牌号的高效热阻材料处于预研阶段。根据2024年中报披露,公司通过组分设计及制备工艺优化,已经实现了多型装备多种零件的热阻涂层的制备,并针对部分子项目完成小批零件试制并进行试车,公司技术水平处于国内领先阶段。

4.3
铂力特
公司及创始人介绍:公司核心团队来自于西北工业大学的材料学院,以黄卫东教授和薛蕾教授为核心,凝结了一批西工大的技术骨干。西北工业大学是我国航空航天传统强校,培养了大批在航空航天领域的领军人物。依托西工大优秀的航空航天基因,铂力特在航空航天领域的资源优势显著,先后拿到了“星、箭、船、弹、机”等六十余项重点型号的零部件预研认证,并逐步走向批产。
全产业链优势突出:公司以LSF工艺起家,随后介入到SLM工艺中,在代理海外EOS设备的同时积极布局自研设备,随后从设备、打印服务切入到粉末制备,2021年公司入股北京正时精控,主要业务为振镜及其控制系统的研发生产。经过多年积累,公司形成了从软件设计到粉末制备到设备制造到打印服务的全产业链生态,通过与下游主机厂客户的深度绑定和设备的快速更新迭代完成了自身护城河的打造,同时全产业链的模式实现了公司盈利能力的提高,全套解决方案也进一步提高了公司的营收规模,加快了融资的节奏。全产业链的模式使得公司领跑同行,成为国内首家在科创板上市的增材制造企业。

产能规划彰显公司信心:2022年7月22日,公司在官方公众号中官宣三期项目正式开工,根据其环评报告披露情况,三期项目较一期、二期扩产较多。此外,公司于8月29日发布定增预案,拟募资31.1亿元,建设四期项目,项目投资额25.1亿元,主要用于粉末生产线、打印服务生产线建设,共配备各类设备505台,建成后,产能将实现跨越式增长,进一步拉大公司与竞争对手的差距。大规模的产能扩张反映了公司目前充裕的在手订单,彰显了公司对于行业发展的信心。
4.4
超捷股份
深耕紧固件行业多年:公司是紧固件头部企业,深耕行业多年,在汽车紧固件领域具有较高的知名度,与多家汽车Tier1零部件厂商以及新能源汽车主机厂保持较好的合作关系。公司不断扩大产品覆盖品类,持续加强与客户链接。

无锡基地落地支撑公司业务扩张:随着国内重要客户项目以及海外出口项目的落地,公司产能遭遇瓶颈。募投项目无锡超捷汽车项目逐步投产,公司产能有望打破天花板,从而满足海外出口和国内重点客户项目落地等产能需求。

切入航天赛道,享受商业航天红利:公司于2022年收购成都新月数控机械有限公司,正式进军商业航天领域,公司设立了商业航天业务团队,目前业务主要方向为商业火箭箭体结构件制造,包括了火箭的壳体、整流罩、发动机阀门等,目前公司已经完成铆接产线建设并投入生产,可生产包括壳段、整流罩以及发动机阀门等产品。
五、风险提示
原材料价格大幅波动:若原材料价格大幅波动,相关材料生产企业无法及时传导成本将会导致产品利润被侵蚀的风险;
企业募投项目不及预期:目前部分上市企业正通过募投项目提升产能规模,需留意项目推进不及预期风险;
下游需求增长不及预期:需留意火箭制造环节下游需求增长节奏情况;
技术路线迭代风险:新材料与新工艺的发展与终端需求的技术路径发展息息相关,需留意下游需求技术路径变更带来的影响;
股价大幅波动风险:需留意二级市场股价大幅波动风险。
本文数据来源如无特别说明均来自Wind资讯
中航证券新材料团队:擅长新材料和宏观周期研究,依托中航工业集团强大产业背景,研究体系重点围绕航空航天新材料、能源材料、轻量化材料及工艺等,形成赛道型产业链覆盖和跟踪,注重投研一体,形成业务层面一、二级市场协同。
邓轲(证券执业证书号: S0640521070001),中航证券研究所新材料行业首席分析师。
156-5176-6816
dengke@avicsec.com
证券研究报告名称:商业航天深度报告:星辰大海,“材艺”相随
对外发布时间:2024年10月27日
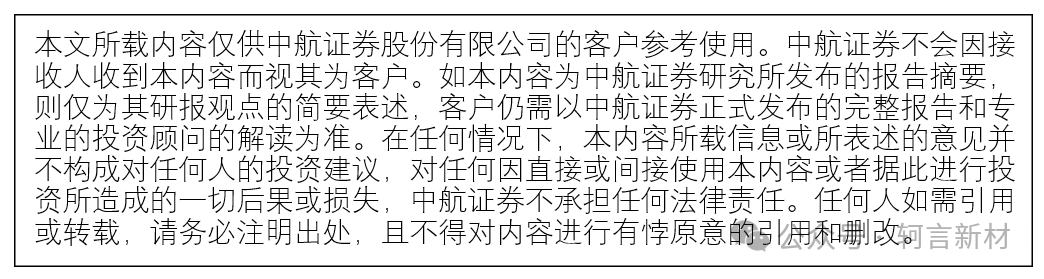
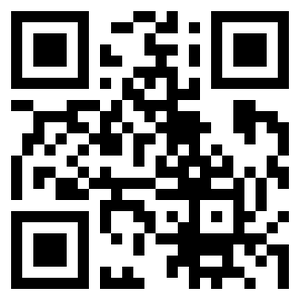
VIP课程推荐
APP专享直播
热门推荐
收起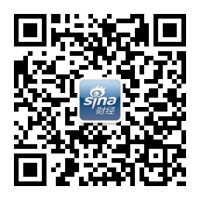
24小时滚动播报最新的财经资讯和视频,更多粉丝福利扫描二维码关注(sinafinance)