刘小虎
中航西飞复合材料重量轻、强度大,常被广泛应用于飞机制造领域。但复合材料制造成本较高,控制成本成为复材研制过程中的重难点问题。复材制造的成本主要分布在原材料成本、工装制造成本及能源消耗等方面。从原材料方面进行成本控制是直接有效的,可以通过材料利用率来体现,目前,不断提升材料利用率也成为提升制造水平的关键。
在生产制造中,提升材料利用率主要可以从以下两个方面进行:一是在零件工艺准备过程中对零件下料图的优化。二是在零件铺贴时对操作方法的不断精进。中航西飞复合材料厂通过优化零件下料图的方式对材料利用率进行提升。
目前复合材料零件下料图的制作方法是,先在三维数模中将零件的每一铺层展开成二维图形,然后根据所用材料料卷的幅宽及铺层角度要求,对每层预浸料进行分割切片,保证每一片预浸料均在材料幅宽之内,最后导出切好的料片并在同一材料幅宽中进行排布。在预浸料切片这一步中,对于结构较为简单的零件,为了减少每一层拼接的次数,同时尽可能有效占据材料幅宽,切片尺寸通常设置为比材料幅宽小20~50毫米;但对于一些结构型面较为复杂的零件,铺贴面非平面时料片尺寸过大容易影响铺贴过程,例如,蜂窝芯较多时需将预浸料开刀后再进行铺贴、零件曲率大时也会出现铺贴产生褶皱的情况,这就可能导致根据下料图裁剪好的预浸料无法准确铺贴整层,存在额外补充材料的情况。复合材料厂结合操作的方便性,在切片时适当减小每一片预浸料的幅宽,根据零件特点设置不同铺层的切片尺寸,从而避免铺贴时增加材料的情况出现。
其次,复合材料存在四种铺层角度,分别为0度、90度、45度和-45度,在排列切好后导出料片时,有手动排料和软件自动排料两种方式,二者优缺点各异:手动排料可以将料片按照铺层角度划分,同一角度排列在一起,以减少料片之间不必要的间隔,但手动排料速度较慢,也容易产生遗漏;运用自动排料软件进行排料时,速度快且整块材料空间能得到最大程度的利用,缺点是料片顺序被打乱。复合材料厂在排料时将这两种方式结合,先将不同角度料片分类整理,再使用排料软件进行排列,并对排列后的结果做适当调整,尽量减少空隙,如有较大空间可以用尺寸较小的料片进行填充;若料片为规则形状,例如,随炉试板下料图均为同样大小矩形,排料时每片料片之间不设置间隔,可以有效减少边角料浪费;如果同种材料包含若干个不同零件,便将零件下料图进行合并,排列在同一个下料程序中,也可以避免更换下料程序中间机器重新启动产生的材料浪费。
复合材料制造中的成本控制不可忽视,原材料成本控制也将持续整个研制过程。复合材料厂通过对下料图的优化,最直观地映射出材料用量的减少情况,在做好材料的排兵布阵的同时,从工艺准备的源头进行材料成本控制,更加有效地节约成本,提升研制与制造能力,推动公司复合材料研制向更高水平迈进。
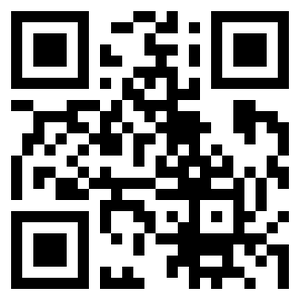
VIP课程推荐
APP专享直播
热门推荐
收起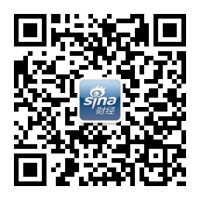
24小时滚动播报最新的财经资讯和视频,更多粉丝福利扫描二维码关注(sinafinance)