炒股就看金麒麟分析师研报,权威,专业,及时,全面,助您挖掘潜力主题机会!
(报告出品方/作者:中信证券,袁健聪、黄耀庭、李鹞)
电池结构件持续迭代,制造门槛提高、附加值增加
电池结构件包括电芯顶盖和壳体,是保障锂电池安全的核心部件,起到支撑、防护、 传输能量作用。锂电池精密结构件指具有高尺寸精度、高表面质量、高性能要求等特性的 壳体和顶盖,起到传输能量、承载电解液、保护安全性、固定支承电池、外观装饰等作用 的部件,并根据应用环境的不同,具备可连接性、抗震性、散热性、防腐蚀性、防干扰性、 抗静电性等特定功能。
电池结构件包括顶盖、壳体两个部分,顶盖和壳体价值量之比约为 2:1
锂电池顶盖结构复杂精密、承担能量传输和防爆泄压作用,价值量约是壳体两倍。锂 电池盖板由 10 多种元器件组合而成,主要由盖板、正负极极柱、注液孔、翻转片、防爆 片等结构组成,结构精密复杂,价值量约是壳体 2 倍。顶盖是穿刺、热失控、着火等情形 下的重要保护器件,它可以减少过流电流,减少翻转片被熔断的机率,从而防止动力电池 起火或者爆炸,有效降低危险性。目前,锂电池防爆方法通常有断路防护和泄压防护两种。断路防护是指在电池内密封片与极芯之间设置特殊的断路焊点,当电池内因产气而使内气 压增大到一定值时,密封片受压变形,与极芯之间的焊点被拉断,彻底切断电路。泄压防 护指在电池密封体上设置防爆阀,当内气压升高到防爆阀的开启压力时,防爆阀即从刻痕 处破裂并泄压,从而避免出现爆炸的现象。
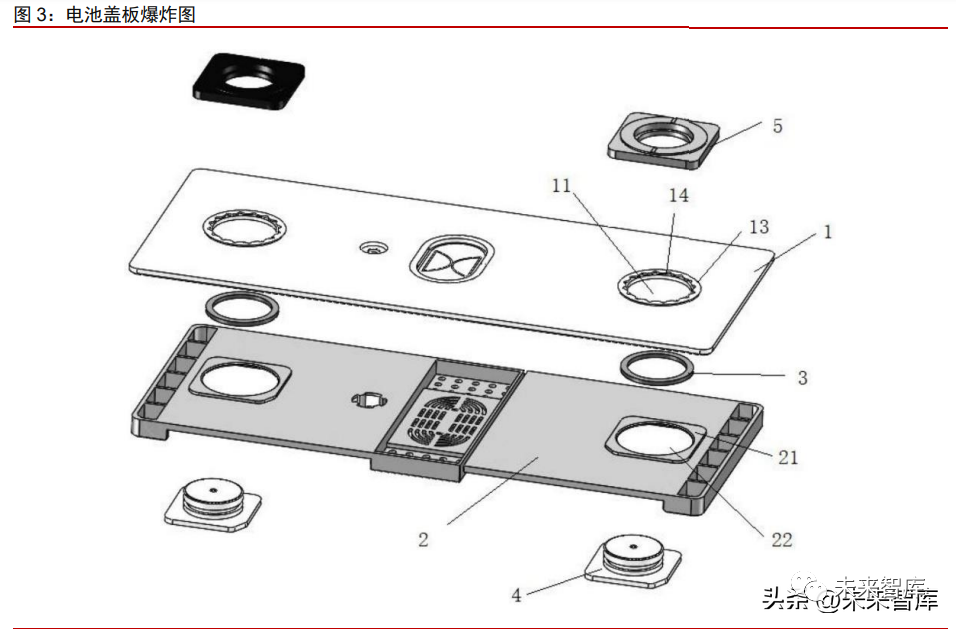
电池壳体主要起到对内部电化学系统固定和全密封作用,结构相对简单。壳体起到对 内部电化学系统固定和全密封作用,对结构强度、散热等性能要求较高。因为电池在充放 电过程中会产生一定量的气体、电芯也会膨胀,形成对壳体内部的压力,电池壳的结构强 度必须足以抵抗电芯膨胀力而不能发生破裂;电池壳的热量需要通过电池壳体向外散热, 若壳体的散热性差,电池散热不及时,长期处于高温状态下的电池容易出现损坏。此外电 池壳体拉伸过程需要严格控制无金属丝屑导致潜在短路,对一致性、稳定性要求高。由于 铝壳密度为钢的 1/3,导热性能是钢的 5 倍,可塑性强铸造性能良好等特点,壳体材质由 钢壳向铝壳转变。
冲压拉伸为主流生产工艺方案
电池结构件生产端具精密制造属性,顶盖生产流程较为复杂。顶盖结构复杂,主要生 产工艺包括冲压、激光焊接、注塑等,首先使用冲床将原材料冲压成各种金属件,经清洗 后再使用激光焊接技术将安全阀、加工极柱等部件焊接并组装在一起,注塑成型后对其进 行性能、气密性检测,检测合格后入库。除了基本技术,结构件也发展了众多延伸技术, 如安全阀防爆设计、摩擦焊接技术等,主要用于顶盖结构的优化升级。壳体的生产工艺主要有两种:1)板材冲压拉伸;2)板材折弯焊接。1) 绝大多数的电池壳体的生产相对简单,主要采用精密连续冲压拉伸工艺,原材料 分切后对其使用冲床进行多次拉伸直至成型,得到壳体半成品,再对其修剪、清 洗、烘干,经检测合格后入库。2) 刀片电池由于呈现窄而薄的特殊形状,两极位于电池两端,无法使用传统冲压工 艺生产盒式电池壳,目前多使用两端开口的管式电池壳。传统方形电池外壳铝制 薄壁管材宽度 50mm 以下,而“刀片电池”的“刀鞘”宽度在 64mm 以上,但由于刀 片电池的壳体很长,拉伸时易出现破裂,所以以板材折弯和焊接方式生产电池外 壳。
电池结构创新下,结构件设计变复杂,制造门槛提高,附加值增加
电池结构创新百花齐放,带动电池结构件设计持续迭代。电池技术创新是驱动行业发 展的主要推力,在电芯材料体系创新之外,4680、麒麟电池等电池结构创新使得电池系统 的能量密度、空间利用率、安全性等性能进一步提升。电池的结构创新最直接地带来电池 结构件上的迭代升级,设计的复杂度提升,从而带来制造门槛提高,附加值增加。
4680 大圆柱电池结构件壁厚增加、材料升级,制造门槛提高。4680 是特斯拉电池日 上提出的直径 46mm,高 80mm 的全新尺寸圆柱电池。为了配合特斯拉的 CTC (Cell-to-chassis)技术,4680 在电池包中起到结构支撑作用,因此 4680 电池的壁厚增 加(从 0.2mm 增加至 0.6mm),并采用预镀镍钢带增加强度。4680 电池体积变大,精度 控制难度更高;预镀镍钢壳加工性比铝壳弱,若冲压模具、流程等未合理设计,容易拉断 表面镀镍层而导致废品,制造门槛提高。
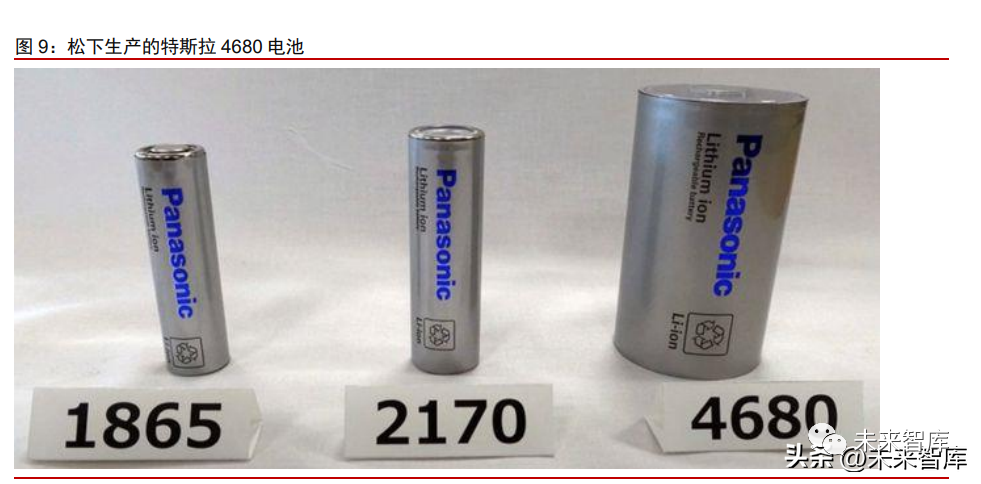
“热电分离”趋势下,电池结构件壳体上加开泄压阀,生产工序增加、难度增加。在 电池安全技术不断升级下,“热电分离”成为下一代电池结构创新设计趋势,宁德时代 NP2.0 技术和蜂巢能源龙鳞甲电池都采用了这种设计。“热电分离”指的是热失控泄压区与电气 连接区各自独立、烟气与高压隔离。在传统的电芯结构件设计中,正负极极柱与泄压阀在 同侧顶盖上,生产时只需对于顶盖进行多工序加工,壳体可以简单地通过连续冲压拉伸生产;而在热电分离设计下,要在壳体底部或侧面开设泄压阀,增加了结构件中壳体生产的 工序和难度。
电池向大电芯、无模组趋势演进,电芯级电池结构件功能性增强,生产的难度增加, 附加值提升。当前电池技术处于持续迭代创新期,无论是方形还是圆柱电池,都有向着大 电芯、无模组演变的趋势。在这种趋势下,模组级的结构件被简化,取而代之的是电芯级 的结构件需承担更多功能,例如承重、热电分离等。在电池结构件功能增加的需求下,电 池结构件的设计变复杂,生产的难度增加,从而带动附加值提升。
预计 2025 年超 500 亿空间,头部份额集中
预计 2025 年市场空间超 500 亿元,未来三年 CAGR 超 30%
电池结构件是方形和圆柱电池不可或缺的组成部分。按照电池封装技术路线不同,锂 电池主要有方形、圆柱、软包三种形状,方形、圆柱电池需要使用电池结构件、软包电池 使用铝塑膜封装。具体来看,圆柱形电池多采用具有较强稳定性的钢材作为外壳,部分采 用延展性较强的铝合金作为外壳,易散热、良品率高;方形电池壳体分为钢壳、铝壳、塑 壳三类,其中钢壳、铝壳较为普遍,结构强度高,不易受外力破坏,塑壳主要应用于二轮 电动车;软包电池使用铝塑包装膜替代金属壳体,单体能量密度高。当前方形和圆柱是主 流的封装路线。
电池结构件的价值量约为 0.4 亿元/GWh,与负极、隔膜、电解液等主材价值量相当。我们选取了几款国内热销车型所用的电池壳体的成本进行分析:热销车型用的电池型号集 中在圆柱 2170、方形 52148、方形 28148 和比亚迪刀片电池等,综合考虑主要型号电池 的结构件价值量和对应装机量的权重,我们测算出 2021 年电池结构件的每 GWh 电芯的 价值量约为 0.4 亿元,与负极、隔膜、电解液等主材相当,是“第五大主材”。
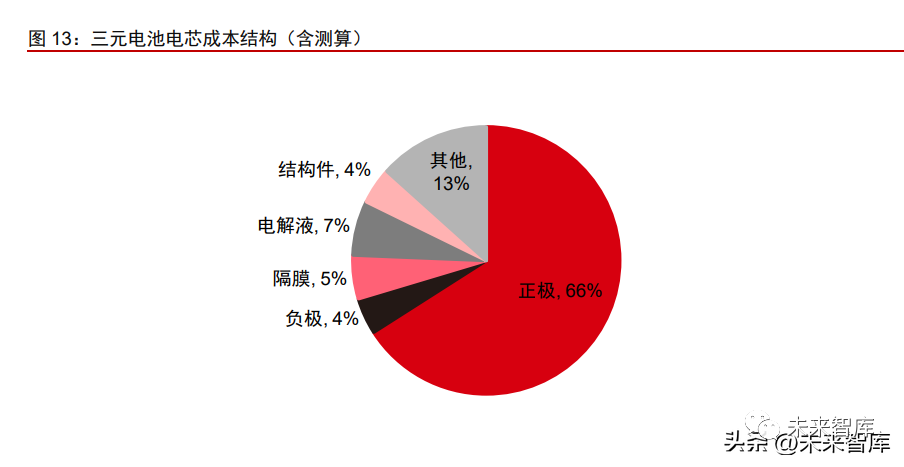
预计 2025 年动力及储能电池结构件市场空间约 532 亿元,对应 2022 年至 2025 年 CAGR 为 31%。测算假设与过程如下:
1、电池需求假设:受益于新能源汽车行业的持续高景气度,我们预计到 2025 年中国 /海外动力电池需求分别为 931/564 GWh,全球动力电池需求在 2025 年有望达 1.5TWh, 对应 2022-2025 年 CAGR 为 38%;此外,全球储能市场方兴未艾,未来需求空间大,增 速快,我们预计 2025 年全球储能电池需求约为 500GWh,对应 2022-2025 年 CAGR 为 57%,具备更高增速。整体来看,到 2025 年全球动力+储能电池需求达 2.0TWh,对应 2022 年至 2025 年 CAGR 为 42%。
2、方形与圆柱电池占比假设:国内电池厂多采用方形电芯技术路线,我们预计方形 电池未来将继续保持主流地位,圆柱电池占比随着 46 系大圆柱电池应用略有提升;海外 电池厂当前多采用软包技术路线,但预计海外主要车企特斯拉未来将采用圆柱/方形技术路 线、大众集团未来采用方形技术路线、宝马集团未来采用方形/圆柱技术路线,海外市场未 来方形与圆柱电池占比有望不断提升。
3、单 GWh 结构件价值量假设:根据上面的测算,2021 年单 GWh 结构件价值量约 为 0.43 亿元/GWh,我们预计随着电池成本按年下降、电芯能量密度提升,单 GWh 结构 件价值量亦按年下降,到 2025 年单 GWh 结构件价值量约为 0.29 亿元。由此我们预计 2025 年全球方形、圆柱电池需求总量约 1.7 TWh,对应结构件市场规 模 532 亿元,折合 2022 年至 2027 年 CAGR 31%。
行业格局一超一强多小,份额集中
格局一超一强多小,份额集中。行业内玩家众多,但份额相对集中,全球 CR2 超 60%, 国内 CR2 约 80%,呈现一超一强多小格局。行业龙头为科达利,2007 年开始布局动力电 池结构件业务,当前是下游大客户宁德时代、LGES、中创新航等主流电池厂的核心供应 商,我们测算 2022 年上半年科达利全球份额约为 42%,市场份额稳居行业第一;行业龙 二为震裕科技,2015 年成立锂电结构件事业部,是宁德时代的另一大核心供应商,随宁 德时代成长迅速,位居行业第二。国内其他企业规模较小,在体量上与头部企业差距明显。
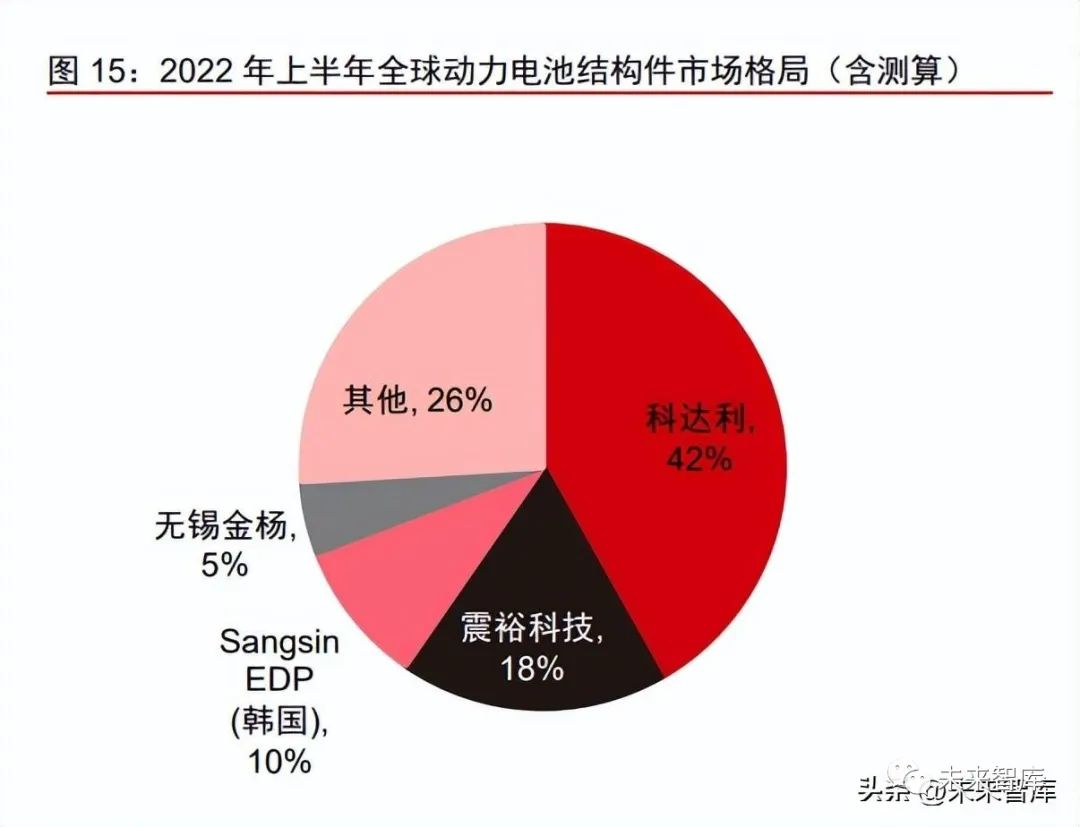
横向来看,电池结构件在锂电池上游各环节中格局最为集中。根据 GGII 等第三方统 计数据及我们的测算,2022 年上半年国内三元正极/铁锂正极/负极/隔膜/电解液/结构件 CR2 分别为 23%/40%/39%/59%/50%/83%。电池结构件行业在锂电池上游的各主要材料 环节中,市场格局的头部份额最为集中。
我们认为,未来的行业格局有望进一步向头部集中。因为行业的头部企业入局时间早, 拥有多年的从业经验积累,形成了工艺、规模和客户上的先发优势,在电池结构持续创新 下,二三线企业与头部企业的差距还将维持,所以未来行业格局会进一步集中,具体原因 会在下一章节展开讨论。
工艺、规模、客户是行业竞争要素,头部企业具备优势
竞争要素一:工艺水平
冲压工艺三要素是模具、设备和材料,决定生产产品的质量。冲压工艺是结构件生产 中最常用的工序,其利用事先设计好的模具,在冲床设备下,将板材加工成所需形状,具 备生产效率高、一致性好的优点。模具、设备和材料是影响产品质量的三要素。模具是生产工艺中的核心因素。同样的设备,在不同设计和精密度的模具下会生产出 品质截然不同的产品。模具的设计需要考虑被加工产品的形状、强度要求以及表面光洁度, 从而设计模具的工序分配、形状尺寸以及模具间隙。不合的工序分配和加工形状容易导致 冲压加工的过程中出现断裂、壁厚不均等问题。模具间隙影响产品的表面质量,间隙过大, 所冲压工件的毛刺较大,在电池内容易造成电池内部短路;间隙小,冲压质量好,但会造 成模具磨损严重,模具的使用寿命将大大降低。
设备及设备的使用影响产品的良率、生产效率。冲床设备自身的精度和一致性影响产 品的精度和一致性,尤其是在连续加工时,刀头容易在热效应下产生形变,从而影响精度。冲床一般分为进口冲床和国产冲床。当前进口冲床的设备更为先进,加工的效率、良率、 一致性更好,但同时价格也更为昂贵,如日本旭精机的高精度冲床售价在 1000 万人民币 以上,国产冲床售价约为 300 万元人民币。另一方面,拥有良好的设备下,设备的使用操 作也非常关键,一般而言,对于操作细节的打磨需要经过 2-3 年的试错期。
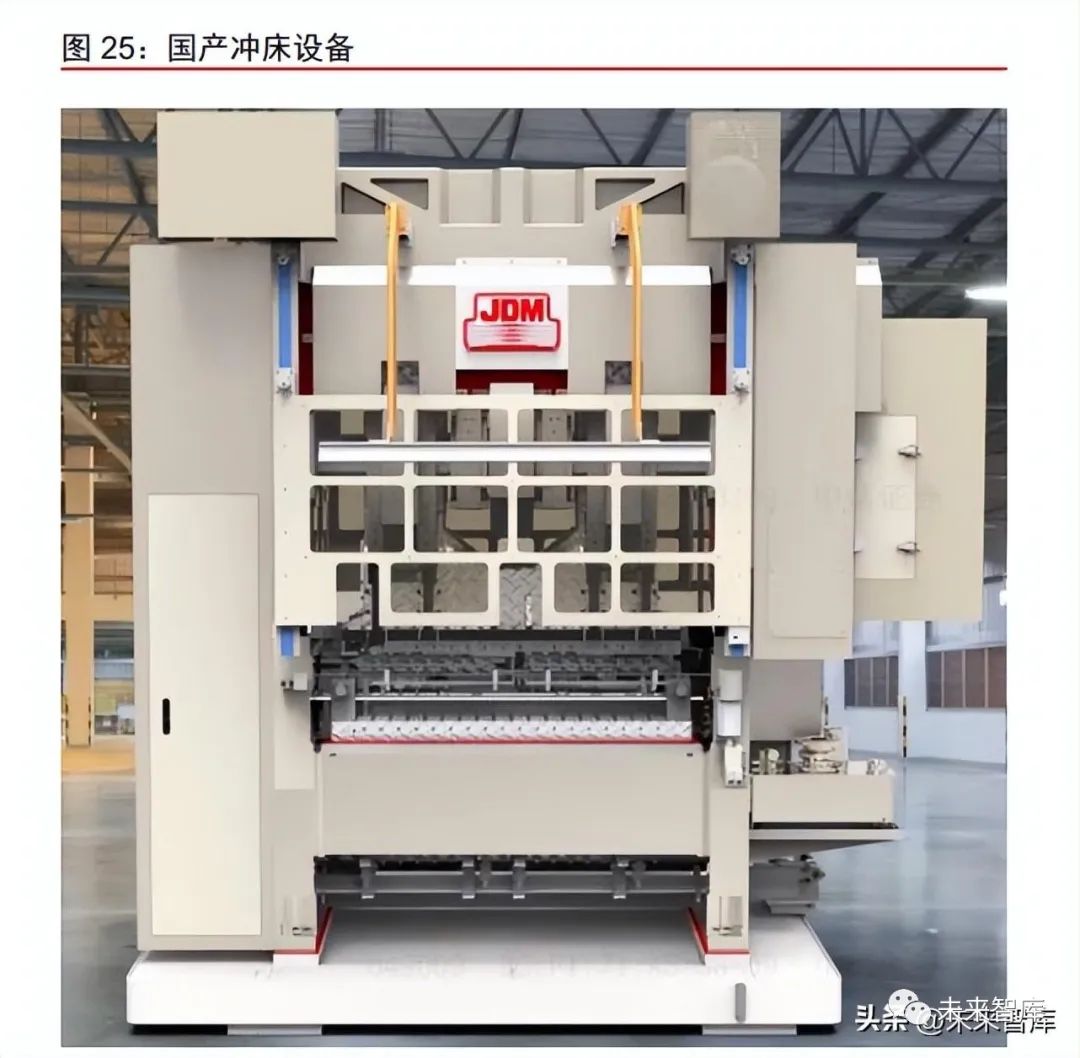
材料的加工性能影响成品性能。材料的加工性能主要包括屈服强度、延伸率、加工硬 化值、球化度等。屈服强度越高,在冲压成形结束后,冲压件弹性恢复的变形越大,影响 冲压件的尺寸精度;延伸率越大,材料的胀形、翻边的成形极限越大,利于结构复杂、长 行程的加工;加工硬化值越高,被加工区域材料的变形阻力越大,随后的变形便转移到其 它地方,得到更均匀的变形,更适用于拉伸类成形的加工。头部企业在模具上领先优势明显,拥有资深模具师,与二三线企业拉开差距。模具设 计依靠资深模具师的设计经验和对模具精细的调整,模具师需要对机械制图、加工工艺、 设备有全方位的理解。模具师的培养是学徒制,有经验的资深模具师将自己多年的经验与 徒弟口口相传,再加上徒弟长时间的实践积累,因此培养一名资深模具师需要 5-10 年的 时间。电池结构件的头部企业科达利与震裕科技前身都是做精密冲压模具起家,其中科达 利 2001 年开始为锂电池厂供货,拥有多位二十余年从业经验的资深模具师,并且科达利 通过“大业盛德”持股平台(占公司总股本 2.63%)绑定了这些核心技术人员,保障了公 司二十余年 know-how 的传承。
头部企业在研发上敢于投入,持续加码。头部企业在研发上积极投入,配合下游客户 开发高端新产品。研发费用绝对量上,科达利的研发费用从 2020 年到 2022 年增长 3 倍 以上,远高于二三线企业的研发费用增速,目前研发费用达到二三线企业的 8-10 倍以上;研发费用率上,头部企业科达利研发费用率稳中有升,营收体量在行业内最大的同时,研 发费用率在行业内依旧保持首位,积极投入。
因此,头部企业的设计创新能力最强,优先承接定制化、高端化创新需求,保持工艺 技术上持续领先。在头部企业的深厚工艺积累以及高研发投入下,下游客户优先将定制化、 创新需求交给头部企业研发,头部企业工艺上持续领先。头部企业与二三线企业在专利数 上差距明显,尤其是在各类创新的顶盖及壳体的结构设计专利数量上遥遥领先。
电池结构件是一个多品类的产品,中高端产品相比一般产品毛利率相差最大可达 10%。电池结构件的规格、型号繁多,因此公司往往直接采用产品对应产值代表销量和产能,披 露整体的毛利率水平。但如果细分来看,根据震裕科技定增审核问询回复函,不同产品之 间单价、毛利率水平有显著的差别,中高端产品比一般产品(非极简 vs 极简)毛利率相 差最大可达 10%。
头部企业工艺水平上的领先最终体现在毛利率上,利润空间更丰厚。头部企业拥有资 深模具师,模具设计能力强,同时又敢于在研发上加大投入,优先承接下游客户的高端化 创新需求,具备生产高端产品的能力。因此在产品结构中附加值高的中高端产品占比更高, 利润空间更丰厚。
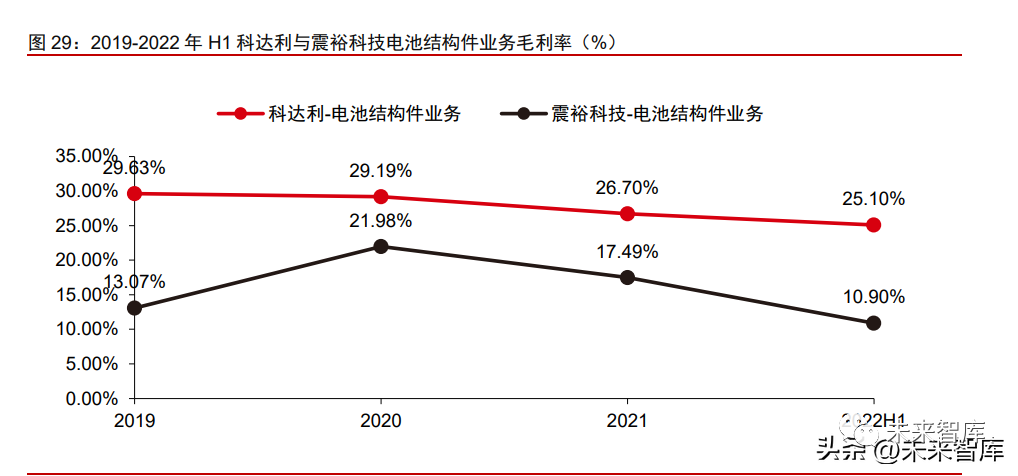
竞争要素二:规模及产能利用率
客户产能规划规模大,单个电池项目结构件产能需求在 10 亿元以上,对结构件供应 商产能规模需求大。锂电池需求未来将保持高速增长,电池厂积极在各地布局动力电池项 目,单个电池项目产能规划约在 30GWh 左右,按照 0.4 亿元/GWh 的结构件需求来计算, 单个电池项目所对应的结构件产能需求在 10 亿元以上。在电池厂的保供需求下,需要结 构件供应商的产能规模大。
电池结构件行业属于重资产行业,投入/产出比约为 1:1~1:1.2,单位产值产能的资金 需求大。电池结构件行业的固定资产占比约为 36%,在锂电池产业链中属于固定资产占比 高的行业。根据科达利可转债募集说明书,电池结构件项目投资中设备投资占比超过 50%;根据科达利可转债申请文件反馈意见回复函及科达利财务数据,我们测算结构件行业的机 器设备投入/产能比约为1:2~1:2.5。因此综合来看,结构件行业投入产出比约为 1:1~1:1.2, 即 1 亿元产值产能需要 8000 万-1 亿元资金投入,其中设备投资约 4000-5000 万元。
产能扩张依赖融资,头部先发企业具备融资资金优势。产能行业有重资产属性,扩产 需要大量的资本开支。然而行业利润率并不高,自身利润造血能力无法支撑后续持续的大 规模资本开支,需要依靠外部融资。因此对于主业为锂电池结构件的公司,未上市中小企 业难以在扩产速度上追赶已上市的头部企业,率先上市、规模体量大的公司在融资方面具 备先发优势。
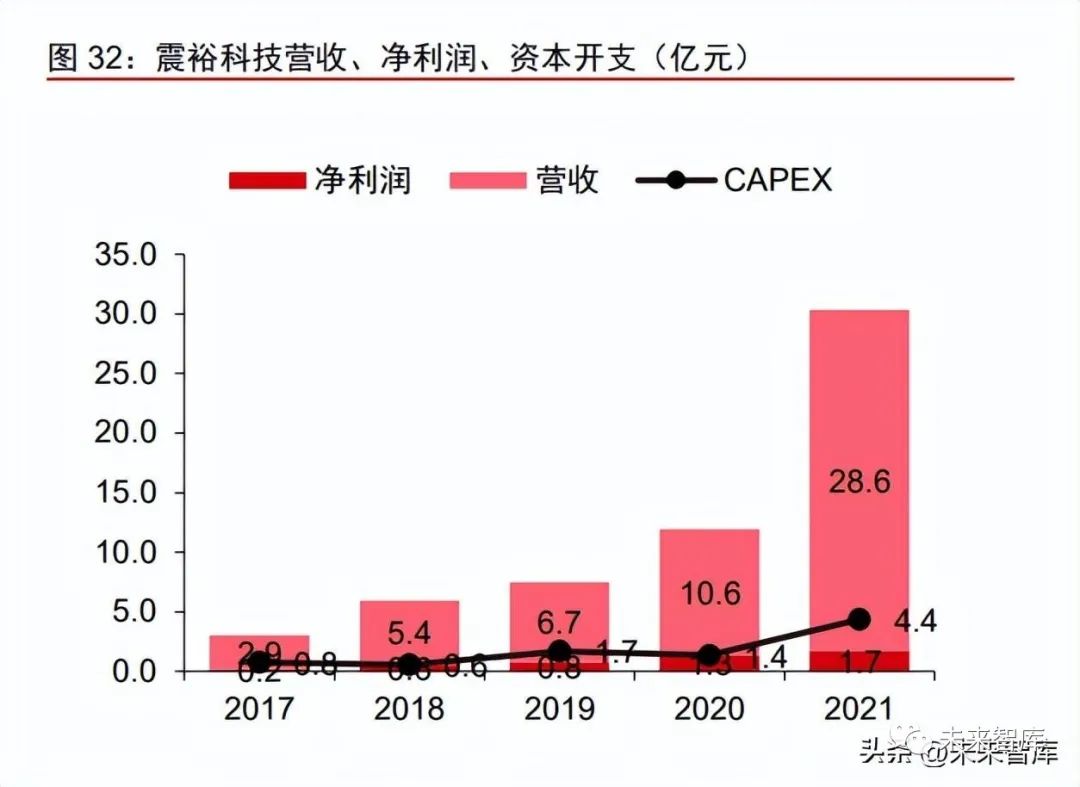
固定投入高,产能利用率是盈利能力保障。由于结构件行业的重资产属性,产能扩张 需要前期大量的设备资金投入,带来设备折旧摊销费用;此外,盖板生产需要依靠人工对 零部件进行拼接组装,机器难以完全替代,成本中人工成本占比高。设备折旧与人工成本 可视为固定成本,在产能的投资规模扩大后,需要生产规模跟上,即保证产能利用率,对 于固定成本进行摊销,盈利能力才有保障。
55%的产能利用率是龙头的盈亏平衡点,二三线企业的盈亏平衡点会更高。以 2021 年科达利的实际情况为分析基准,设备折旧、人工成本以及期间费用在营收中分别占比为 6%、12%、10%,2021 年科达利毛利率为 26%,净利率为 12%,产能利用率为 85%。假定设备折旧、人工成本以及期间费用为固定成本,材料成本、其他制造费用、其他损益 等为可变成本,由此我们测算出,55%的产能利用率是科达利的盈亏平衡点。科达利是行 业龙头,毛利率与净利率在行业内领先。对于一般的二三线企业,其产能利用率盈亏平衡 点会更高,想要实现盈利需要达到更高的产能利用率。
竞争要素三:客户绑定
动力电池精密结构件属于锂电产业链,具备认证时间长的特点,从结束研发到形成稳 定供应能力需要约 3-4 年时间。复盘行业主要玩家在动力电池结构件业务上的发展历程, 科达利 2007 年开始研发动力电池精密结构件,2010 年研发成功,到 2014 年动力电池精 密结构件销售额达 2 亿元,距离 2010 年研发成功相距 4 年时间;震裕科技 2015 年成立 锂电池结构件事业部,到 2019 年形成 2.2 亿元对外销售收入,中间同样相隔 4 年时间。
先发企业已经跟随大客户完成配套建厂,深度绑定合作。电池结构件是上游各环节中 最追求就近配套建厂的环节,核心原因在于就近建厂进行交互式研发模式,增强快速反应 能力,并且有助于减少运输成本。当前先发企业已经在就近配套建厂中实现深度绑定合作, 签订份额保障协议,等后进入者形成产能规模后,切入空间有限。
工艺、规模、客户相辅相成,共筑行业壁垒
工艺、规模、客户相辅相成,螺旋上升。工艺、规模和客户是行业三大核心竞争要素, 三者是相辅相成的关系。工艺水平是获得客户订单的核心,具备和客户就近配套建厂的资 金实力、形成规模是形成客户深度合作绑定的前提。客户的绑定、共同研发又是工艺水平 持续进步的推力,是规模扩张后产能利用率提升的订单保障,最终工艺与资金再去支持进 一步的客户拓展。在三者相互之间的互相催化中,企业完成工艺、规模和客户的螺旋上升。
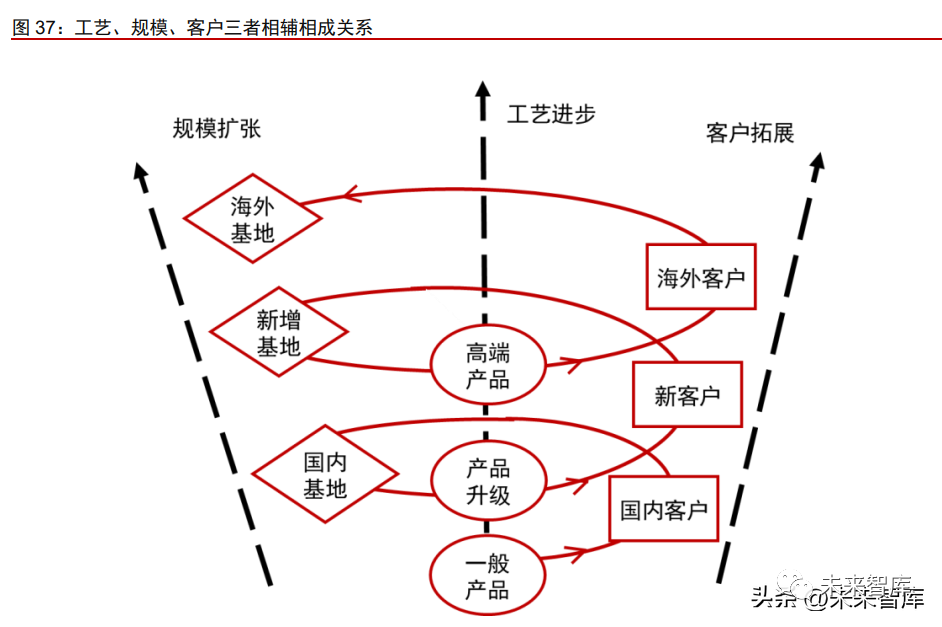
头部企业率先实现了工艺、规模、客户的有机循环,在三个竞争要素上建立起了先发 者的竞争壁垒。头部企业入局时间早,从业经验久,在工艺上拉开了与二三线企业的差距, 并且持续投入研发,工艺持续保持领先;规模上融资渠道丰富,产能规划充沛;客户上完 成了深度合作与绑定,形成了三者的有机循环,筑起行业壁垒。对于新入局者而言,在工 艺上与头部企业存在差距,形成规模尚需时间,因此我们判断行业格局未来还将稳固,有 望进一步向头部集中。
(本文仅供参考,不代表我们的任何投资建议。如需使用相关信息,请参阅报告原文。)
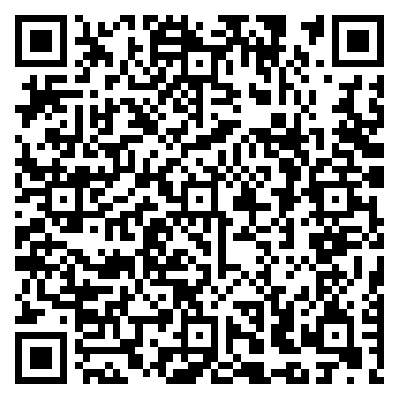
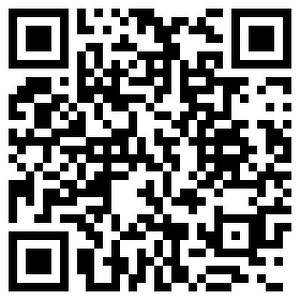
VIP课程推荐
APP专享直播
热门推荐
收起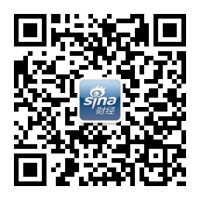
24小时滚动播报最新的财经资讯和视频,更多粉丝福利扫描二维码关注(sinafinance)