锂离子电池主流回收工艺分为四种:湿法工艺、火法工艺、联合工艺和修复再生工艺。
一
预处理与二次处理:放电、拆解与材料分离
由于锂离子电池成分复杂、结构致密,直接采用高温冶金或湿法冶金的方法回收效率较低。为提高回收利用效率,在从废电池中回收有价金属之前,通常需进行放电和初步分离预处理,以减少金属的混合和回收过程中试剂与能量的消耗。
1) 放电
为防止废旧电池短路、自燃,在拆解电池之前,首先需要对电池进行放电处理。主流的做法是将电池正负极浸入导电盐溶液中,实现短路放电;这种方法效率高且稳定,成本低廉,适合小型废旧电池的放电处理。对于电动汽车用锂离子电池组,由于残余容量较多,也可使用充放电机收集残余电量,检测残余电压处于安全范围后再进入拆解粉碎阶段。对于高容量电池的大批量工业化应用,也可使用低温冷冻法,即将废旧电池冷冻至极低 温度(如液氮冷冻)失活并安全破碎;但该方法对设备要求较高,初期建设成本较高。
2) 分拣拆解
由于不同活性材料、不同使用目的、不同电池制造商生产的电池在体积、包装、材料组分等方面的差异较大,分拣拆解的目的在于去掉废旧电池(组)的外壳和包装,减小电池体积,有针对性地分类处理不同类型废旧电池。在实验室研究和尚未规模化回收的企业,人工拆解是主要的拆解方式。操作人员用刀、 锯等工具手动拆卸废旧电池单体,去掉塑料或金属外壳,将外壳、正负极、隔膜等分离开。这种方式得到的活性物质纯度相对较高,电芯作为一个整体进入后续处理阶段,杂质含量少。但人工拆解效率低、处理量小,仅能作为研究阶段或小作坊生产,难以实现规模化工业应用。
面对大规模的回收过程,机械拆解在经济和工业应用方面更具优势。机械操作把塑料或金属外壳封装的电池用钢锯切割除去两端及壳体,获得电池内部的材料,再依据正极材料的化学组分采用更具针对性的回收工艺进行批量处理。
在实际应用中,电池包-模组-单体的拆解以手工为主,少数企业尝试采用自动化 拆解;而从电芯到废粉,大部分企业都采用自动化拆解。工艺流程来看,废旧电池包由输送机物料首先送入一级破机中进行粗破碎;粗破碎后的物料通过输送机送入二级破机中进行次破碎;次破碎后的物料进经过输送机和磁选器去除铁后,再进入三破机中进行细破碎至粉末。粉末状态的物料由负压系统进入到旋风分离器中进行空气过滤,并通过风机落至气流分选机上;气流分选机使不同密度的物质分层,将金属分选出来,并使非金属由负压系统带入脉冲除尘器进行集中。过滤得到的尾气由负压系统送入尾气处理设 备中空气净化,达到排放标准后再进行高空排放。
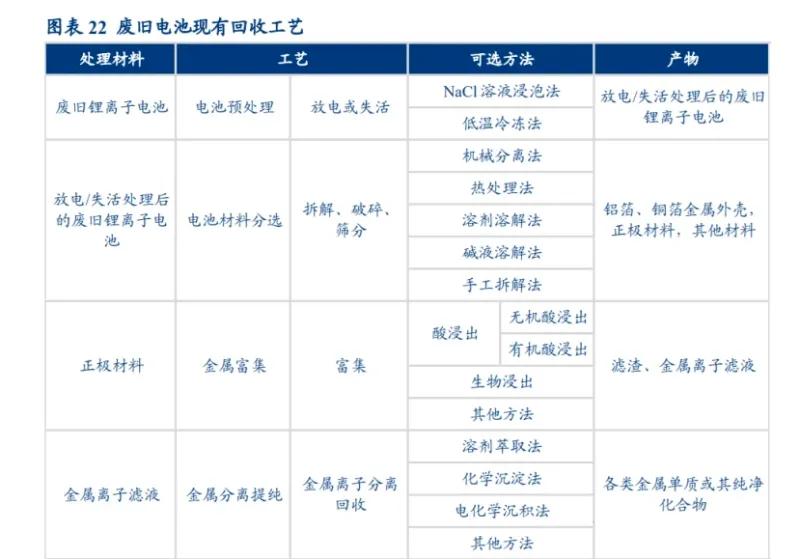
3) 粉碎筛分&活性材料与集流体分离
分拣拆解后,需要进一步分选出含有金属的材料,包括干法和湿法工艺。干法回收工艺是指不通过溶液等介质,直接对有价金属进行回收,主要采用热处理+机械分离联合处理。机械分离法是利用电池不同组分密度、磁性等物理性质的差异,采用浮选、振动筛选、磁选等方式筛选分类破碎后的电池材料,实现塑料、金属外壳、铜箔、 铝箔及电极材料的初步分离。但电池活性材料是通过粘结剂粘附到集流体上的,机械处理直接分离活性材料的分离率较低:如果破碎强度较小许多活性材料不能完全回收,强度过大又会使一些铜和铝被破碎成细小颗粒进入活性材料。因此去除有机粘结剂是机械破碎前的必要步骤,首先通过热处理法将放电、拆解后的电极废料高温煅烧去除隔膜、 粘结剂和碳材料等,再通过一系列机械处理(如粉碎、筛分等)实现活性材料和集流体的分离。干法回收操作工艺简单,在高温条件下反应迅速,适合用于处理大量或者结构 比较复杂的电池;但高能耗且容易造成大气污染,前期设备投资也较高。
湿法回收工艺是通过酸碱溶液对废旧锂电池中金属离子进行溶解,再使用沉淀、吸附、萃取等方法将溶液中的离子进行再提取,使其以氧化物、盐等形式分离。在活性材料与集流体分离工段,主要的湿法工艺有有机溶剂溶解法、碱溶解法等。有机溶剂浸泡法利用相似相溶原理,采用极性较强的有机溶剂溶解粘结剂,破坏集流体和活性物质接触界面的粘合,实现活性物质的脱离;该方法不破坏材料结构且不改变活性材料组分,回收效率高;但有机溶剂大多价格昂贵,且有毒易挥发,不适合大规模工业应用。碱液溶解法是利用铝的两性性质,利用碱溶解铝箔,而活性物质不溶于碱液,实现二者分离;该方法操作简单、分离效率高,但生成的铝酸钠较难回收处理,强碱也易腐蚀设备。湿法回收工艺过程较复杂精细,但回收产品纯度更高,因此是目前废旧电池回收工艺的首选。
二
深度处理:目标金属的浸出与分离提取
电池回收的深度处理是在预处理放电、拆解、破碎、分离后,将电极材料溶解浸出,使 其中的金属及化合物以离子形式进入到浸出溶剂中,再分别进行对应金属的分离回收;主要可分为浸出和提取两个阶段。
1) 浸出
浸出是废电池回收湿法工艺中的关键步骤,主要是将预处理后的正极活性物质中的金属 元素转化为溶液中的离子,便于后续分离回收工序,常用的酸包括无机酸(HCl、 H2SO4、HNO3、H3PO4 等)、有机酸(草酸、柠檬酸、苹果酸等)。传统无机酸中,盐酸浸出效果最佳,但易挥发,在反应过程中会生成 Cl2;硝酸不仅易挥发,还具有强氧化性,容易生成有毒的氮氧化物,且价格高于盐酸和硫酸;硫酸价廉易得,沸点较高,可采用较高的浸出温度提高浸出速率和溶解率。但硫酸的浸出效率相对较低,因此实际操 作过程常在硫酸溶液中添加还原剂H2O2,且需要较高的浸出温度和较大的液固比。但 由于 H2O2稳定性差、易分解,当前有很多研究致力于寻找更高效稳定的替代物。除无机酸外,对环境友好的有机酸也是目前的关注方向:有机酸较无机酸不会产生有毒气体,废液也没有强酸性,便于处理,对设备腐蚀较小;但有机酸价格较高,浸出速度较慢,且液固比高于无机酸,对应正极材料处理能力远小于无机酸,因此难适用于大规模处理。
整体来说,酸浸过程的核心是反应温度、时间、酸浓度、固液比和还原剂含量,直接影响到金属离子的浸取率。
2) 提取
正极活性物质浸出后,重点回收的钴、锂、镍、锰等金属均以离子形式存在于浸出液中,需通过进一步的深度处理,进行彻底的分离、提纯并回收,主流工艺包括化学沉淀法、 溶剂萃取法、电化学沉积法等。化学沉淀法是向金属浸出液中加入适当的沉淀剂,与金属离子发生沉淀反应达到分离效 果。化学沉淀法的分离机理是一定 pH 下金属化合物的不同溶解度,在不同 pH 值下对 Ni、Co、Mn、Li 等不同金属离子进行梯次沉淀分离;这种方法提取率高、成本低、对设备的要求低,但由于部分金属沉淀条件苛刻,如果没控制好沉淀剂用量和溶液酸碱度,可能会出现多种金属同时沉淀的现象,难以分离,造成不必要的资源浪费。
萃取法是选择一种特定的萃取剂或几种萃取剂的混合物,通过与目标金属离子形成稳定的配合物,在有机相中与浸出液分开,再将配合物反萃实现金属离子的分离提纯。萃取法优势在于目标金属离子提取准确、能耗低、操作简便,回收率和纯度都比较高;但缺点在于需要大量化学试剂,存在污染环境的风险,溶剂在萃取过程中也会有一定流失,成本较高。通常情况下,混合萃取剂具有更好的协同效应,萃取效果优于单一萃取剂。目前国内电池回收工厂主要采用分步萃取的方法回收浸出液中的金属离子:首先将Cu、Al、Fe 等杂质化学沉淀去除,净化液采用 P204 萃取锰,负载有机相经过硫酸溶液反萃、 净化后得到纯净硫酸锰溶液;萃余液再采用 P507 在不同 pH 条件下分别萃取 Co、Ni, 负载有机相经过硫酸溶液反萃的到纯净硫酸钴、硫酸锰溶液。该方法可制备纯的 Mn、 Co、Ni 硫酸盐产品,但萃取过程使用的P204和P507萃取剂均需皂化处理,碱消耗量大;另外整个萃取流程相对较长、级数较多。
电化学沉积法是指在外电场作用下,通过金属的电极电位差异,使浸出液中的目标金属离子在阴极发生电化学还原反应得到金属的方法。该方法简单易行、操作中不需添加化学试剂、引入杂质少,不仅使产品的纯度和回收率很高,也避免了后续处理工艺的复杂 化。但缺点是需消耗较多的电能,另外为避免其它金属离子的共沉积,需要在前处理过 程中纯化活性材料。
三
电池回收成本&产物价值量分析
成本端来看,电池回收成本结构主要分为两大块:废电池本身的费用和加工费。废电池本身的费用占比通常超过总体的 50%,其他加工费包括辅助材料成本、燃料动力成本、 环境治理成本、设备成本、人工成本、其他支出(场地费、公摊费、税费)等。对于磷酸铁锂电池,假设电池包回收价格为18000元/吨,干法与湿法回收单吨成本(购买电池包以外)分别为5900元/吨与11300元/吨,总回收成本分别为23900元/吨与 29300 元/吨;对于三元电池,假设电池包回收价格为38000 元/吨,干法与湿法回 收单吨成本(购买电池包以外)分别为6000 元/吨与14400 元/吨,总回收成本分别为44000 元/吨与52400 元/吨。
尽管干法工艺相对简单、回收成本较低,但其产物中杂质更多、处理过程中污染更大, 目标产物回收率也低于湿法,存在一定工艺缺陷;因此目前国内电池回收产线以湿法为主。对于磷酸铁锂电池,当前主要回收产物是废铜、碳酸锂、磷酸铁。参考本文第二章的测算,磷酸铁锂动力电池包中,单体质量占比约60%,单体中正极材料质量占比约32.1% (活性材料在正极材料中质量占比 88-89%),铜箔质量占比约10.8%;按照回收率铜箔98%、碳酸锂90%、磷酸铁95%假设,则单吨磷酸铁锂电池包可提取废铜 63.5kg、碳酸 锂 35.9kg、磷酸铁 154.8kg,对应主要回收产物价值量 1.7 万元/吨磷酸铁锂电池包。对于三元电池,当前主要回收产物是硫酸镍、硫酸钴、硫酸锰、碳酸锂。参考本文第二章的测算,三元动力电池包中,单体质量占比约 68.2%,单体中正极材料质量占比约 39% (活性材料在正极材料中质量占比 88-89%),铜箔质量占比约13%;按照回收率铜箔98%、硫酸镍98%、硫酸钴98%、硫酸锰98%、碳酸锂85%假设,则单吨不同三元电池包可提取废铜86.9kg、硫酸镍123.4~293.6kg、硫酸钴 36.8~123.6kg 、硫酸锰 35.8~120.4kg、碳酸锂84.9~85.7kg,对应主要回收产物价值量 4.2-4.5 万元/吨三元电池包。
通过成本与收益的核算,目前锂电回收行业仍处于微利甚至亏损的状态;主要在于 2022 年以来原材料端废旧电池包的高溢价。此前由于锂价较低,三元电池回收以镍钴为主,因此计价折扣系数仅体现镍、钴的价值;22年锂价大幅上涨,为体现锂价值量,只能调高镍、钴的折扣系数;叠加行业参与者激烈争夺废旧电池包资源,电池包的折扣系 数由正常情况下的 70-80%大幅飙升,最高超过 200%,与实际价值量水平存在较大偏差。

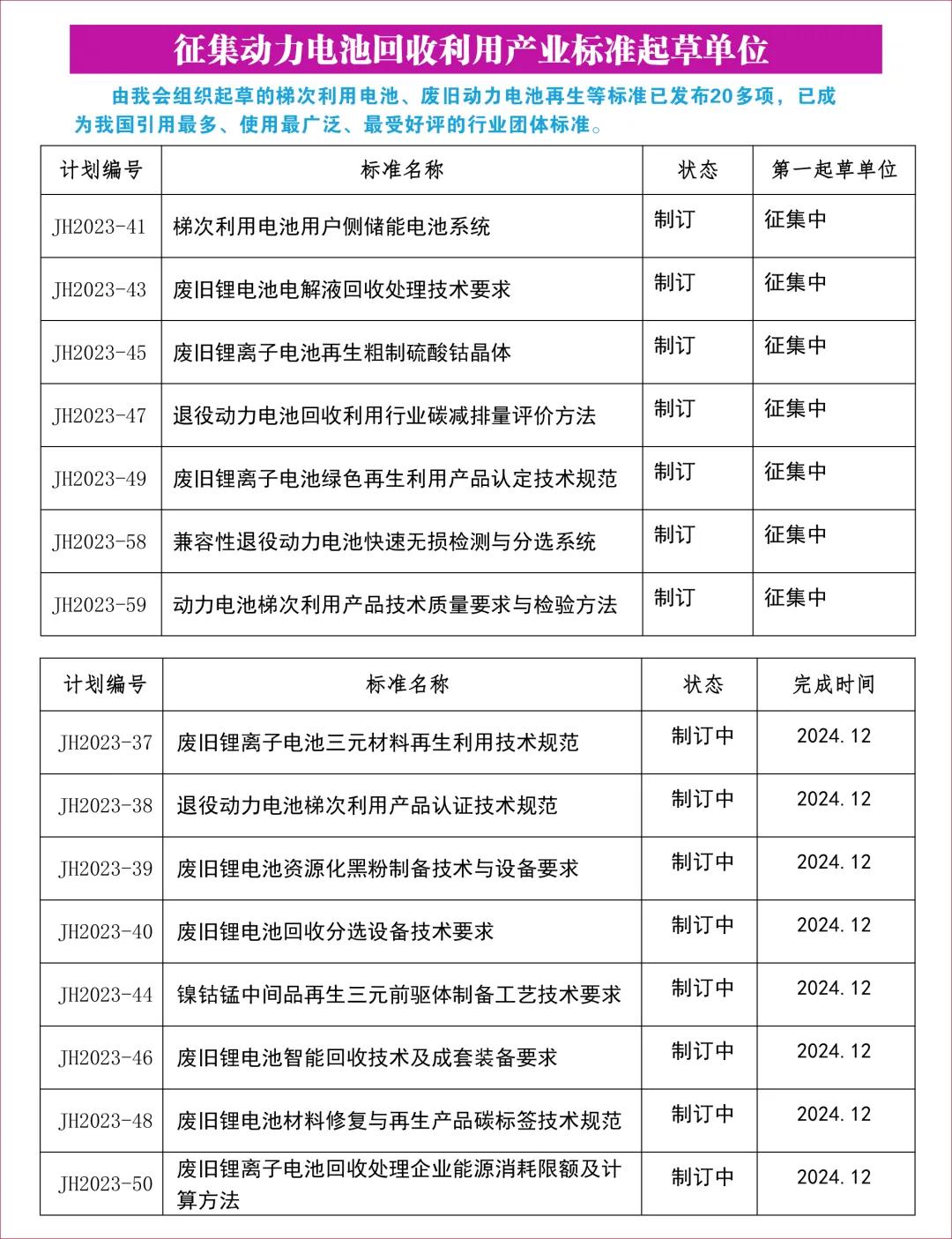
(转自:锂电行业动态)
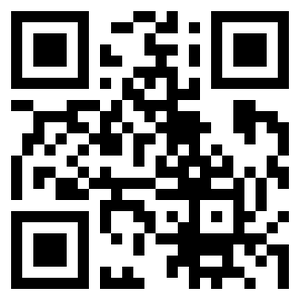
VIP课程推荐
APP专享直播
热门推荐
收起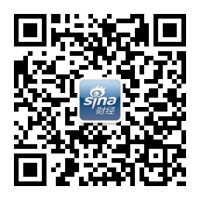
24小时滚动播报最新的财经资讯和视频,更多粉丝福利扫描二维码关注(sinafinance)