本报讯 记者王绍芬 通讯员王平 张伟明报道 8月12日,国内首条高铁双块式轨枕与小型预制构件共线智能生产线,在渝昆高铁建设现场正式投产,标志着我国高铁建设在智能化转型上迈出实质性步伐。这条生产线的成功投产,也为渝昆高铁开通运营奠定坚实基础。
该智能生产线位于云南省盐津县境内,占地面积达5万平方米,集数字仿真、智能机器人、物联网、大数据等技术于一身,承担着渝昆高铁50多万根双块式轨枕和60万块小型预制构件的生产任务。
记者在现场看到,这条智能生产线集成智能打磨、全自动安装、精准布料、智能检测等14个先进工位,以“物联网+”为核心,实现人、机、料、法、环等生产要素的深度互联,一根根高铁轨枕与小型预制构件在几乎无人工干预的情况下自动完成生产,大幅提高生产效率,降低成本和能耗。
在高铁建设中,轨枕的生产是一个重要环节。而轨枕构件,也就是轨枕中的各种钢材,以前需要单独加工后进入轨枕生产线,这样各自生产加工的形式不仅增加了生产线,人力、物力成本也要提高不少。
中国铁建大桥局渝昆高铁项目部经理饶胜斌介绍,这条生产线最大的特点,就是实现了高铁的双块式轨枕与小型预制构件的并线设计、共线生产,从钢材加工到轨枕生产一条生产线就可以完成,这是目前国内最先进的智能化生产线,每2.5分钟即可完成一个模块的生产,较传统方式工效提升50%,运营成本降低25%,单位产值能耗降低12%。
中国铁建大桥局渝昆高铁轨枕场负责人钱勇说,这条智能生产线相比传统生产线具有四个方面的优势:一是劳动力充分释放,传统生产线需要35个人才能满足作业需求,现在智能化共线生产仅需7人,而且劳动强度大幅降低;二是安全更有保障,机器人代替人工焊接、翻转脱模等安全风险高的作业,有效降低人身伤害的风险;三是质量更加可控,计算机控制进行精准布料、智能振捣和自动蒸汽养护,杜绝人为因素对质量的影响,并实现生产数据实时收集,便于后续产品质量的复盘和数据溯源;四是生产绿色低碳,采用机器人代替人工打磨和喷涂,有效降低粉尘污染和喷涂料对作业人员健康的影响,减少临时用地,加之智能化生产各工序衔接更加紧密,减少等待时间,提升了效率。
“这条生产线的投产,为高铁建设领域的数智化转型提供了宝贵经验,这是铁路建设积极响应国家智能建造发展战略、发展新质生产力,深入实践工业4.0理念的重大创新成果。”钱勇介绍。
据悉,渝昆高铁是国家八纵八横铁路网京昆通道的关键组成部分,全长699公里,其中云南段长达388.6公里。作为云南省内首条设计时速350公里的高速铁路,全线建成通车后,预计重庆到昆明行车时长将由原先的5小时缩短至最快2小时左右。
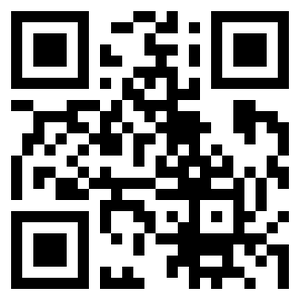
VIP课程推荐
APP专享直播
热门推荐
收起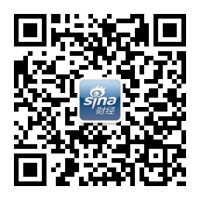
24小时滚动播报最新的财经资讯和视频,更多粉丝福利扫描二维码关注(sinafinance)