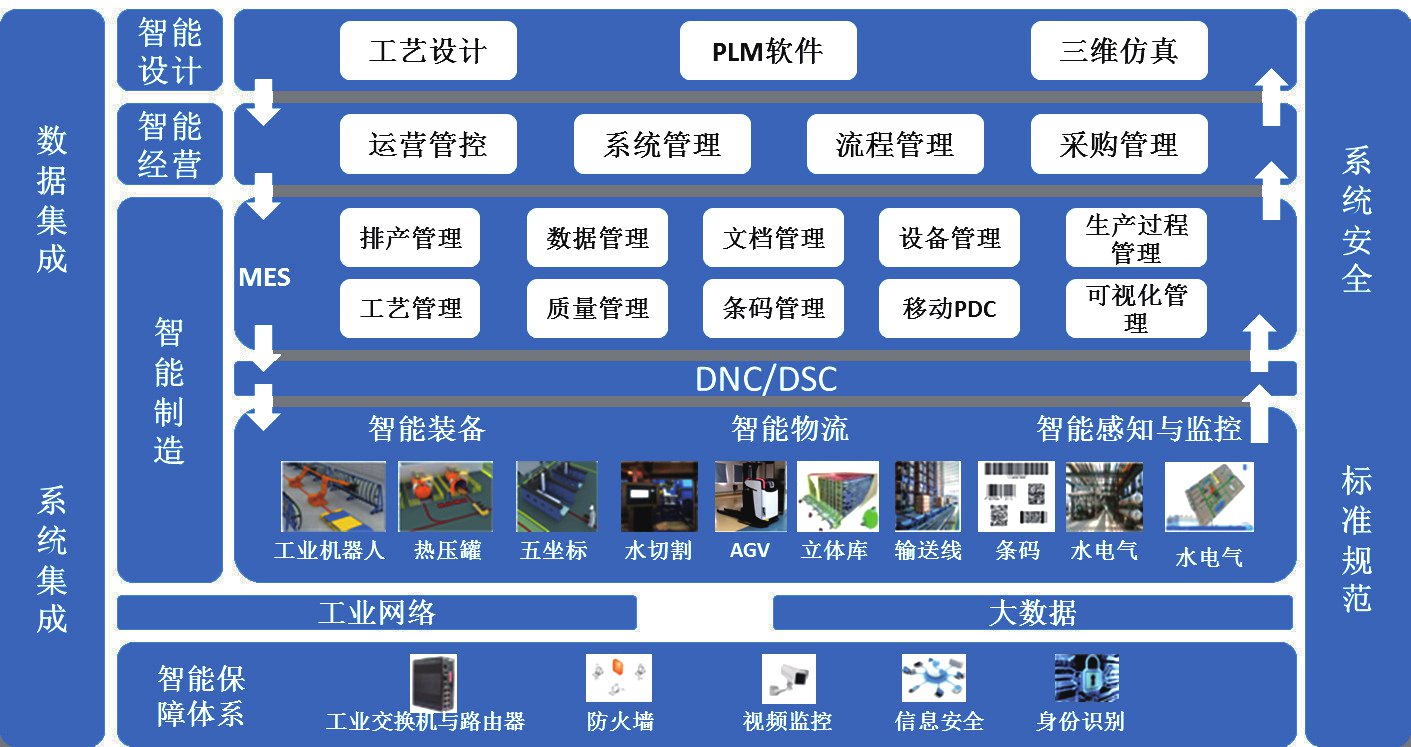
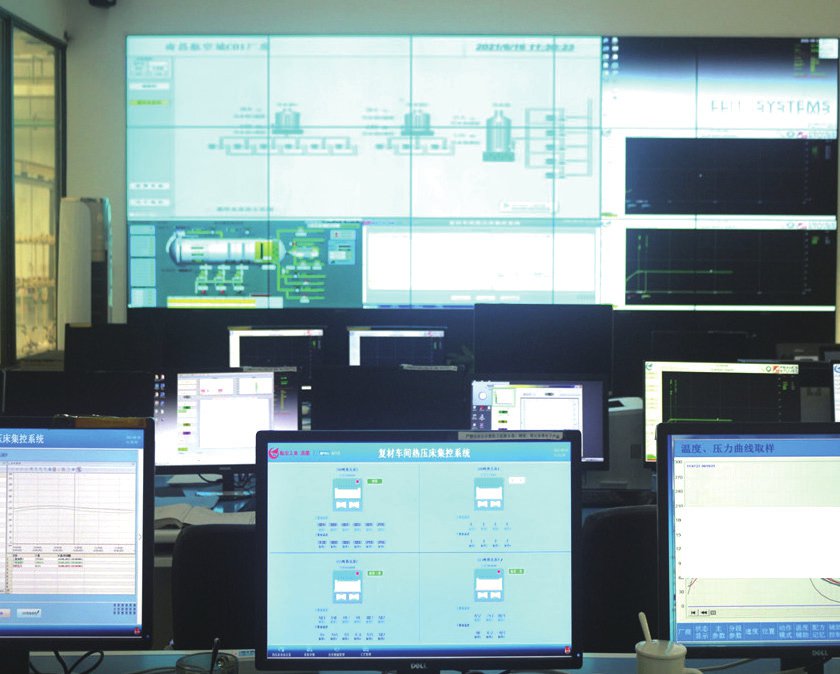
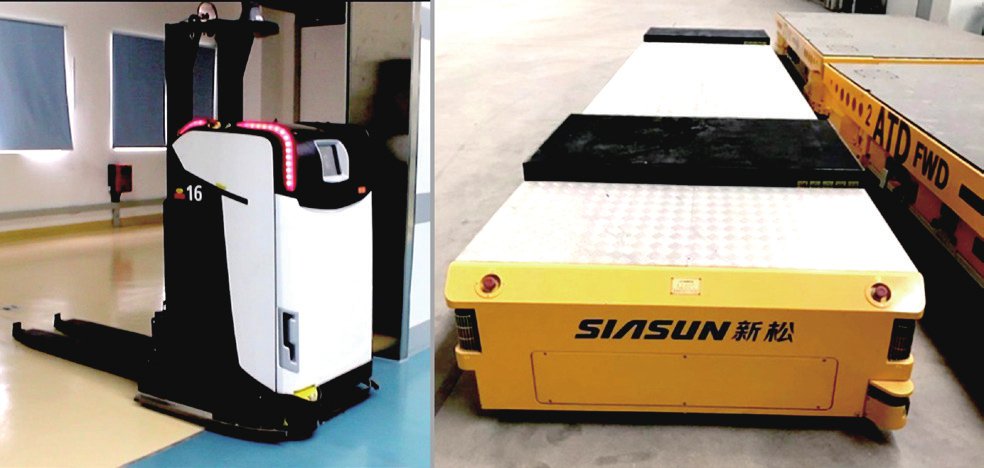
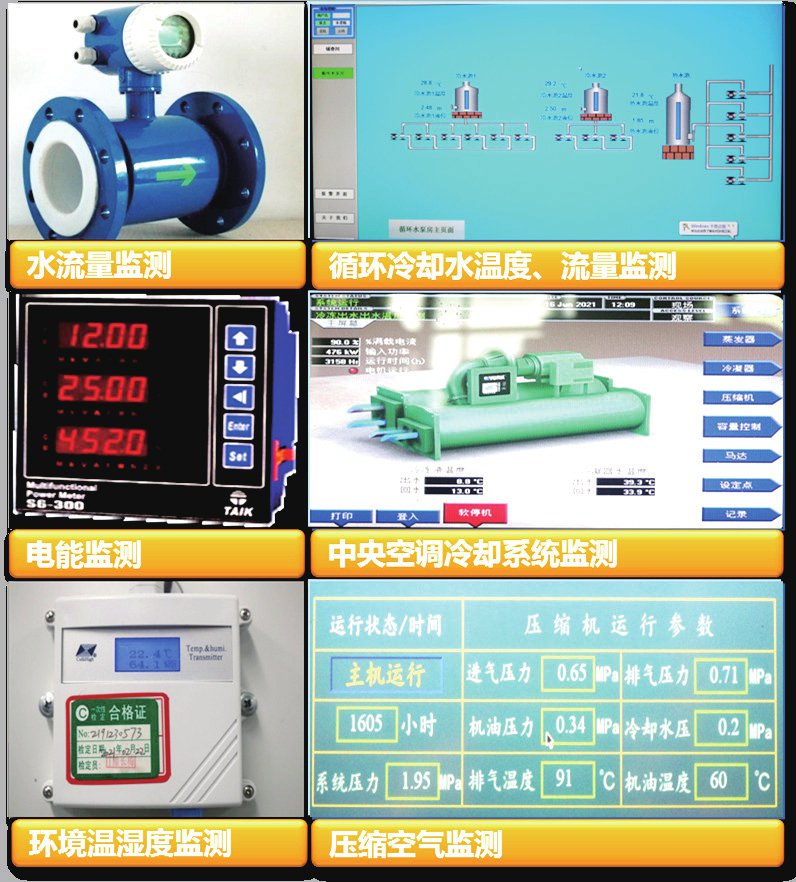
航空工业江西洪都航空工业集团有限责任公司(简称航空工业洪都)是中国航空工业奠基企业之一,是新中国第一架飞机的诞生地,也是我国教练机的摇篮。随着第四次工业革命变革的到来,洪都为实现飞机高质量、低成本、短周期研制目标,以工信部批复建设的《航空复材零部件智能制造新模式应用》项目为切入点建设航空复合材料数字化车间,大力推动信息化、数字化及智能化体系建设。航空复合材料零部件以其质轻、比强度比模量高、可整体成型复杂曲率零部件等优势在航空飞行器上的应用越来越广泛,其使用量占比已被用于衡量飞行器的先进水平,先进航空复合材料的快速发展也带来了自动化及数字化制造的巨大需求。由于复合材料结构制造工序流程长,控制环节多且复杂,交织着大量物理、化学变化,不同因素间相互作用影响很难量化及显性化,造成复合材料传统制造过程可控性弱,这种不确定性给复合材料制造及技术发展带来很大的挑战,通过自动化、数字化技术与复合材料制造融合创新,建设航空复合材料数字化车间是解决复合材料制造过程管控不确定性的有效方式。
技术架构为首航空复合材料数字化车间总体框架(如图1所示)主要涵盖了智能设计、智能经营、智能制造(MES、DNC/DCS、智能检测与装配装备、智能仓储与物流配送)三个层面。通过对复合材料车间的智能化软硬件升级改造,贯通工艺设计、生产计划、生产准备、仓储物流、质量检测等各个环节,搭建产品设计和制造之间的“桥梁”,形成向上衔接设计、向下承接制造、装配、物流等各个方面的功能,降低设计到生产制造之间的不确定性,缩短产品研发到批量生产的转化时间,产品全生命周期进行系统高效的管理。
数字化工艺设计先行项目通过工艺布局与流程仿真、工艺设计优化分析数据库支撑、产品制造加工过程仿真分析及制造过程的3D作业指导等方法手段实现产品从模型到制造环节准确有效演进,保障设计模型能够很好地在工程端落地实施。
制造管理信息化系统承接通过MES系统、采购管理、运营管控等信息化系统建设,实现计划排产、维修管理、过程质量监测、数字化检测、质量分析、文档管理、条码数据采集、现场数据可视化等功能。并通过软件技术、网络技术、视频技术、大数据技术,实现数据信息的共享、实时统计分析、动态判断决策,并实现信息反馈指导制造终端“智”造。
数字化装备和自动化物流夯实基础
基于复合材料零部件自动化铺放技术、自动化固化技术、自适应加工工装、机器人自动钻铆系统、自动化检测技术以及自动化物流配送系统等,实现生产准备—铺放—固化—机械加工—装配—检测—产品交付全流程的自动化、数字化制造,为数字化车间建设奠定基础。针对热成型设备、自动铺丝机、数控加工设备等数字化装备,开发设备集成系统进行集中管控,实现设备集中控制、集中监测、远程控制、能耗监测、数据采集与分析等,实现设备操作少人化、设备状态显性化、设备定检可预警的管控目标。
针对物流配送系统(如图3所示),建设适应不同物料的自动化立体仓储、各类自动AGV以及仓储管理系统(WMS)和仓储控制系统(WCS),实现主要物料的自动化准时配送。
环境监控保障复合材料制造过程中涉及大量环境因素的控制,针对空压系统、真空系统、冷却水系统、中央空调系统、冷库等等影响复合材料制造的辅助系统(设备),采用各类监测传感器实现环境、设施、设备的温度、压力、真空、流量、气体浓度、粉尘浓度等要素的监测、数据采集、传输功
能。并应用智能集控软件实现辅助系统的远程开关和状态监测。
工业互联网连接工厂内部建立一套完整的工业网络,覆盖整个厂房,实现生产设备、仓储物流设施、环境传感器及应用终端的互联互通,数据的快速流转。
经过多年的自动化、数字化实践以及数字化车间建设,洪都公司复合材料专业从工艺设计、制造仿真、自动化制造、检测、分析及自动仓储配送等方面构建了一个比较完整的具有自动化、数字化特征的航空复合材料数字化车间,构建了航空复材零部件智能制造新模式,实现车间生产效率提高30%以上;运营成本降低20%以上;产品研制周期缩短超过30%;产品不良率降低20%;单位产值能耗降低10%的显著成效。
(航空工业智能制造创新中心与航空工业洪都联合供稿)
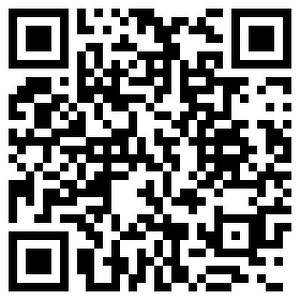
VIP课程推荐
APP专享直播
热门推荐
收起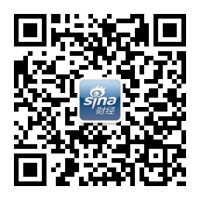
24小时滚动播报最新的财经资讯和视频,更多粉丝福利扫描二维码关注(sinafinance)