原标题:高强耐热的钛基复合材料投入使用让航空航天器轻装上阵性能升级
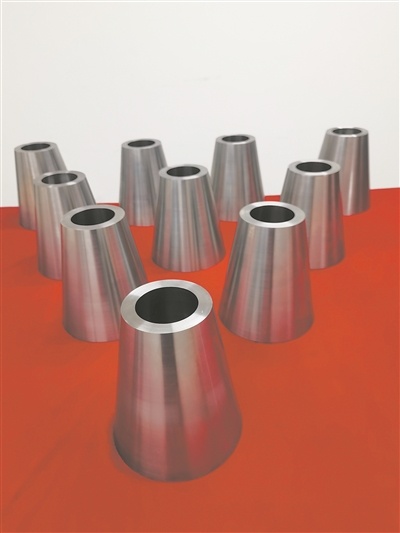
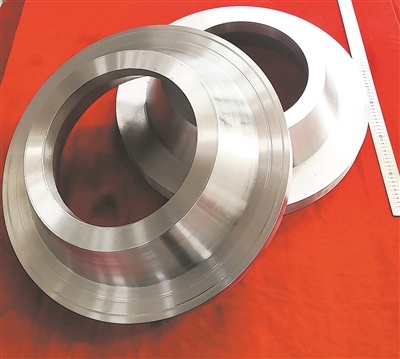
◎本报记者 王 春
航空航天是高技术、高投入、高风险、高回报和高牵引的领域。从C919国产大飞机成功商飞,到神舟号航天员乘组圆满完成出舱活动,我国航空航天事业发展进入“快车道”。这些成就的取得,离不开新型材料,特别是轻质高强金属基复合材料的广泛应用。
相较传统高温合金,钛基复合材料以陶瓷颗粒作为增强相,在同等体积下可减重40%以上,每年节省燃料数百万吨,是实现航空航天高端装备轻量化、提高装备功效和技术性能的关键战略新材料之一。其在航空、航天、民用高端装备等领域的关键部件中有着巨大应用潜力。因此,研发低成本、高性能且技术自主可控的航空航天等高端装备用耐热高强钛基复合材料十分关键。
中国科学院院士、上海交通大学教授张荻,上海交通大学研究员吕维洁带领团队,经过二十余年潜心研究,形成了耐热高强钛基复合材料的制备加工关键技术,实现关键技术自主可控。该材料在高温环境下表现出的高稳定性和强度使得我国航空航天器能够在极端苛刻的服役环境中稳定运行,为我国航空航天高端装备发展提供有力支撑。2023年度上海科技奖日前颁发,“耐热高强钛基复合材料关键技术研发与应用”项目获得2023年度上海市技术发明奖一等奖。
基础研究筑牢创新根基
传统钛基复合材料通常采用外加法生产,存在成本高、基体和增强体之间界面结合性能差、界面反应严重、成材率低的问题。研究团队创新性提出原位自生的学术思想和技术原型,利用传统钛合金的熔炼和热成型设备简捷、低成本制备出高性能钛基复合材料,降低了该材料的工业化生产难度。但由于原位自生增强体在熔炼过程中形核与“长大”,因此,增强体的优化控制是关键难题。
吕维洁介绍:“增强体的优化控制就像人类培育孩子,通过优生生出一个身体底子棒的婴儿,再经过优育进一步提升孩子的素质,成为国家的栋梁之材。”
团队通过创新突破了多元多尺寸增强体形状、尺寸、分布控制的困境;通过复合化技术,提升了传统钛合金的性能,使其能够应对航空航天关重零部件面临的更高温度和冲击载荷的挑战,提高了航空航天装备的性能和可靠性。吕维洁介绍,针对传统钛基复合材料存在的强塑性匹配不佳等问题,团队专注机理研究,提出多元增强体有序分布与耦合强化方法,构建了新的力学模型,创制出航空航天用新一代轻质高强耐热600℃—800℃钛基复合材料,其在室温和高温条件下的各项性能指标均达到国内领跑、国际领先的水平。
精细加工实现社会效益
新材料对制备工艺提出了更高要求。非连续增强钛基复合材料具有硬度高、弹性模量大、加工硬化严重等特性,这导致传统的加工方法难以满足材料精密成形的需求。在制备过程中,如要保证复合材料的性能稳定性,需要对制备工艺进行精细控制。
“解决这些问题,迫切需要开发先进精密成形技术,以应对钛基复合材料的加工挑战。”吕维洁说。
团队针对钛基复合材料复杂构件难以加工成形的问题,建立了动态再结晶诱发大塑性加工技术,并为航空航天重大装备提供了千余套钛基复合材料构件。
如今,先进金属基复合材料已在航空航天应用,并向新能源、现代交通及船舶与海洋工程等多个领域逐步扩展,正从“贵族”材料向“平民化”发展。
一组数据体现了新材料发挥的巨大作用。在民用大型能源化工装备领域,应用该新型复合材料后,在650℃环境下,离心式压缩机叶轮线速度较之前提高40%、压缩比提高33.3%,年节省能耗8%。在航空航天领域,新型复合材料在800℃的复杂应力环境下,使得先进装备的转动惯量大幅度降低,为装备关键技术指标的实现提供了关键支撑。
目前,团队获得授权中国发明专利26项,制定企业标准5项,发表SCI论文100余篇。团队还建立了国内领先的钛基复合材料产业化基地——浙江嘉钛金属科技有限公司。该公司建立了熔炼、等温锻造、精密铸造等产线,实现了大规格铸锭、棒材、等温锻件、精密铸件、宽幅厚板、薄板的工业化生产。(王春)
原标题:高强耐热的钛基复合材料投入使用让航空航天器轻装上阵性能升级 来源:科技日报
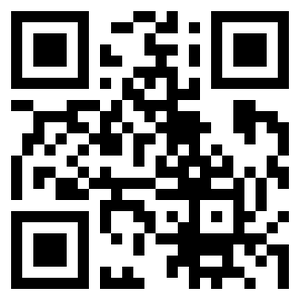
VIP课程推荐
APP专享直播
热门推荐
收起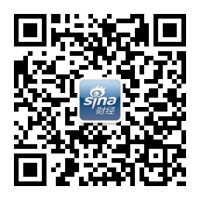
24小时滚动播报最新的财经资讯和视频,更多粉丝福利扫描二维码关注(sinafinance)