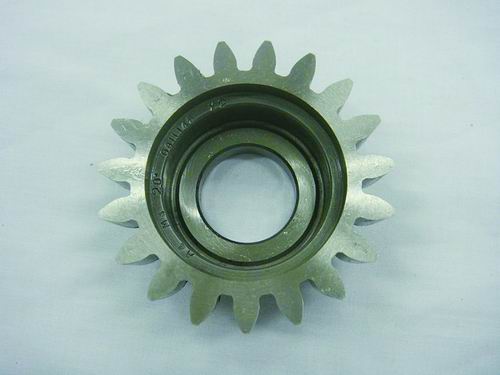
①AA级插齿刀(m4)。

②A级精度剃齿刀。

③王立鼎磨削标准齿轮。

④王立鼎绘制齿轮图。

⑤王立鼎(左)与徒弟一起磨削齿轮。

■本报记者 温才妃
高级轿车为什么比普通轿车更安静?
工厂车间机器轰鸣,怎样降低噪声?
人类无法完成的细微手术,手术机器人为什么能做到精确无误?
……
剥开这些钢铁“外衣”,一对对紧密咬合的齿轮在工业进化史上立下汗马功劳。越是高精度的齿轮组,运行越平稳、噪声越少、传动精度越高。
不久前,工业和信息化部、国家发展和改革委员会等七部门联合印发《推动工业领域设备更新实施方案》,在先进设备、数字化、绿色化、安全性等方面提出了推动工业领域设备更新和技术改造的要求。
“我国正在向高端制造转型升级,其前提是工业零部件的整体升级。现在我们有自信,因为工业用齿轮的升级换代使我国在技术上做好了准备。”中国科学院院士王立鼎如是说。
王立鼎的自信,与他在中国科学院长春光学精密机械与物理研究所(以下简称长春光机所)工作期间,开创出我国超精密齿轮工艺技术密不可分。
1 接到紧急任务,从4级跨越到1级
“在2300公里的距离内,法国阿基丹雷达的误差在5米之内。它是怎么做到的?”1965年,长春光机所窗外丁香花盛开,屋内的科技人员正在热烈讨论。
大家认识到,一个关键要素——齿轮的精度决定了雷达的精确度。但阿基丹雷达中的齿轮并不是由法国生产的,而是由瑞士苏黎世马格公司制造的,这家公司就是大名鼎鼎的西格玛公司的前身。西格玛公司的齿轮加工装备——特型马格磨齿机在业内声名显赫。
20世纪60年代,西方国家在精密仪器的核心技术与装备方面领先一步,并将其牢牢掌握在自己手中,根本不会轻易出售和转让。中国也想做一台类似的新型精密测量雷达,可是仅凭国外杂志的文字描述,其制作工艺、关键数据等无从得知。为攻克超精密齿轮制造技术,长春光机所启动了新一轮的攻关项目。
时任长春光机所所长王大珩把这项重任交给了齿轮研究室的磨齿组。当时正在磨齿组任研究实习员的王立鼎承担了这项超精齿轮攻关任务。1965年,大学毕业刚5年的他,已是一名“熟练工”,由他经手加工的齿轮,精度最高可达4级,而在当时,国内工厂加工的齿轮精度普遍为7级。因为这手本事,那一年,他荣获了中国科学院优秀科研成果奖。
在齿轮的精度等级中,6~8级为中等精度等级,可应用于机床与汽车等工业设备;3~5级为高精度等级,主要应用于超精机床、仪器、船舶、雷达以及航空航天发动机等具有高速高平稳传动要求的场景;1~2级为超精密等级,主要作为国家级或国际齿轮量仪校对和精度传递实体基准。
超精密加工与测试技术是反映一个国家制造工业水平的重要标志之一。精密齿轮加工技术在工业生产、航空航天等领域起到关键作用,齿轮的精度直接影响机械工程装备的整体精度。而在当时能做出2级及以上精度齿轮的国家,全球范围内只有德国和瑞士。
“制作一台精度与阿基丹雷达相当的雷达,齿轮精度起码要2级以上,准确说是1级。”长春光机所经过分析,确定了齿轮箱研究需要达到的目标。
从4级一下子跨越到1级,这让所有人倒吸一口凉气——当时我国没有一个人加工过如此超精密的齿轮。这意味着没有经验可循,一切都得靠自己摸索。
王立鼎接到的任务中包括磨削齿轮,这是齿轮制造的最后一步,也就是说,齿轮精度最后只能靠王立鼎的智慧与双手把控。
2 没有“豪华”实验室,我们自己造
20世纪50年代末至60年代初,美国一家知名企业要为太空导航系统制作一台超精密齿轮设备。承担制作任务的实验室配置要求之高,令人叹为观止。
操作人员不能穿带棉絮的工作服入内,而且要提前洗澡、打发蜡,为的是防止棉絮、头皮屑掉落在室内。实验室外一公里之内不能有汽车行驶,以免引起震动。更重要的是,它对温度有绝对的要求,要求20摄氏度恒温,温差不能超过0.5摄氏度,且湿度控制在40%~60%之间,以最大限度防止齿轮加工设备受到外界因素影响。
可是,打造这样一间高规格实验室,当时的长春光机所实难做到。
王立鼎看看身后,他们只有一个与他人合用的加工间,这里没有恒温,也达不到超净,只有地基的稳定度还算“勉强过关”。加工间只有两台国产齿轮磨床,王立鼎对其中一台齿轮磨床Y7431进行了改造与精化,后来这台Y7431一直陪伴了他的整个科研生涯。
怎么才能在天差地别的条件下,研制出媲美德国和瑞士的超精密齿轮?对王立鼎而言,这着实是一道不小的难题。
同事在王立鼎磨削超精密齿轮时,都默默地把手中的加工设备停下来,以防自己磨削产生的灰尘弥漫到空气中。
一公里以内不让行驶汽车,在白天很难做到,王立鼎就和助手李振铎分成早晚两班。白班由李振铎进行半精磨,王立鼎值晚班进行精磨。王立鼎的晚班从傍晚5点到次日凌晨四五点。夜里万籁俱寂,车间里没有机床开动,马路上也没有车辆行驶,最大限度避免了各种震动干扰。只有加工间里一灯如豆,伴着磨齿迸发出的火光,把王立鼎的眼眸映得通红。
可是,最重要的恒温怎么解决?这离不开王立鼎的巧思。“哲学中有一句话叫作‘变中有不变’。每天的温度都有一个曲线变化。相邻几天如果没有天气骤变,温度曲线变化是有规律可循的。我就是利用每天温度变化趋于一致的自然现象,成功解决了恒温问题。”
简易版的“豪华”实验室有了,超精密齿轮就能顺利诞生吗?
3 把握细节,实现精度的“完美匹配”
磨齿的日常画面是这样——操作人员在机床前端安放一个齿轮毛坯,调整后端分度盘的参数,按下开关启动设备,连接齿轮与分度盘的轴承转动起来,磨齿就开始了。磨好的齿轮表面圆滑光洁,透着银光。齿轮个头儿均等,齿与齿之间的距离一致。
这是一个看似简单的工作,但磨制一对超精密齿轮,一般要耗费王立鼎一个季度的时间。为什么这么难?
超精密齿轮技术的核心要素之一是机床。轴系的精度对机床的传递精度有重要影响,分度盘的精度又决定了齿轮的分度精度。只有各配件精度完美匹配,才有可能诞生超精密齿轮。
“就像一个挑担人,前后各有一个筐,但不能没有扁担,扁担的好坏直接影响了挑担人的工作效果,而那根扁担正是轴承。”王立鼎打了一个比方。
1963年,第一届全国机械传动年会结束后,王立鼎跟随同事去上海机床厂参观。上海机床厂是国内机床界的翘楚,王立鼎心向往之。“在这里我发现,录磁机中的录磁盘回转轴系由多颗高精度钢球构成。录磁机的精度可比加工齿轮的机床高得多,如果我能用上它的轴系该有多好。”
正巧王立鼎的一台机床轴系的主轴坏了。但按当时的规定,更换机床轴系的主轴需要机械工业部批准,机床厂才会答应生产。因此,换轴承的事一直搁置未能解决。
受上海一行启发,王立鼎决定自己更换轴系。“机床轴系原来是不带钢球的,我在自行研制的主轴中加入400颗精密钢球,发现主轴的刚度大幅度提高,这样既保证主轴受力不易弯曲,也发挥了误差均化效应,轴承精度误差由原来的2微米缩小到0.5微米,高于国内外同类机床制造精度。”
他大喜过望,一鼓作气把另外一台机床的轴系也更换了,机床的精度就这样一劳永逸地解决了——不仅比当时国内外机床的精度都高,而且过去60多年精度始终不降,到现在还在使用。“这为后来研制超精密齿轮解决了不可或缺的设备精度问题。”
还有一次,王立鼎检查分度盘时发现,轴心运动产生的曲线并不像他画的那么规整,而是一条不太规律的曲线。
这条曲线很多人看一眼就放过了,而王立鼎却仔细琢磨起来。“它的形态似曾相识,就像是一条正弦曲线。”他再仔细检查分度盘,判断出有两种可能性—— 一是分度盘装偏了,没有跟中心对准;二是分度盘没有装偏,而是在制造中产生了误差。
“无论分度盘是否装偏,纠正的方法都是采用反正弦曲线,一正一反相互抵消,这样就能大幅提高分度盘的精度。”这便是王立鼎自创的“正弦消减法”的朴素思想。“那么,我故意把它装歪一点,产生反正弦曲线,从某种程度上便能解决精度问题。”沿着这一思路,他把分度误差从50角秒减小到13角秒。
这样的巧思来自对细节的把握。齿轮组同事张玉玲曾打趣说:“王老师观察问题,比女同事还要细腻。”一些细节看似简单却不易操作,比如磨齿芯轴的径向跳动从1微米调到0.5微米,王立鼎可以一次成功,换作他人就很难实现。
1966年,仅用一年多时间,王立鼎就采用“正弦消减法”和“易位法”磨齿工艺,研制出我国首套超精密齿轮,达到雷达设计精度要求。那一年,30岁出头的他,成为国内公认的超精密齿轮专家,“齿轮王”的美名不胫而走。
1965年到1980年,王立鼎先后研制出5批超精密齿轮,满足了国家相关项目需求。
4 做测量齿轮的齿轮,为行业定基准
20世纪七八十年代,正是我国工业生产体系全面恢复的时期。
为满足工业发展需求,王立鼎又确定了一个新目标——做标准齿轮。
在工业生产中,用仪器测量齿轮精度效率太低,半个工作日只能测一件齿轮。如果有一款标准齿轮,把它装在测量仪器上与被测齿轮咬合运转一周,便知被测齿轮是否合格,从而可大幅提升检测效率。标准齿轮通常比被测量的齿轮精度高2~3个级别,而当时国内只能做出4级标准齿轮,即只能检测6~7级的齿轮。
如果把标准齿轮做到2级精度,其功能不仅可以用于工业生产,还可以校对齿轮量仪的精度,该齿轮被称为基准标准齿轮,可以为齿轮行业提供基准。
“1975年,长春光机所提出一个目标:到1976年研制出赶超德国的2级精度小模数标准齿轮。”王立鼎回忆说。
有了做超精密齿轮的先例,大家都认为王立鼎之前紧张的科研攻关状态该“松快”一会儿了。然而,由于齿轮小带来了许多技术上的难点,要攻关的小模数齿轮已经超过了机床的加工范围。王立鼎依然还是每天5点起床,一路小跑到单位,打开机床让砂轮提前运转,以便机床更迅速地进入理想的工作状态。然后他再跑回家为家人做早餐,7点30分又准时出现在办公室或实验室。这一习惯他竟坚持了25年之久。
20世纪80年代,王立鼎组织研制的高精度小模数标准齿轮和中模数基准标准齿轮,经过中国科学院组织鉴定,达到德国DIN3962标准中的2级精度,居国际前列,其实体样件作为我国校对齿轮量仪的基准。
当时一个2级精度标准齿轮,在德国售价折合人民币几万元,国家财政购买有困难,长春光机所便无偿将标准齿轮赠送给中国计量科学研究院,帮助国家确定校对齿轮量仪的基准。
1998年,王立鼎被调到大连理工大学工作。他带着在长春光机所积累的经验,又继续在齿轮战线上奋斗了20年,将成果传播到了我国的大江南北。
2016年,经中国机械工业联合会、中国机械工程学会鉴定,王立鼎团队研制的精化齿轮磨齿母机、超精密磨齿工艺和测试技术,以及1级精度基准级标准齿轮,综合技术达到国际先进水平,精度指标国际领先。
5 哪怕只需要一个齿轮,我们也要上
王立鼎经常在不同场合被人问“为什么德国、美国等发达国家的标准齿轮没有做到1级,反而中国先做到了?”
王立鼎是这样回答的:“不是国外不想做,而是他们也有困难。机床是由我们改装的,测量齿轮的仪器是我们自行设计的,齿轮加工方法也是我们自己开发的。在国外,搞齿轮设计的是大学教授,搞齿轮制造的是工厂里的工人,搞计量测试的是实验室里的实验员。他们各自一摊、难以聚合,而我们则是把所有工作串起来。从某种程度上说,我本人既是科技工作者,也是高级大工匠。 ”
王立鼎认为,这与长春光机所老一辈科学家王大珩等一直主张的从预研到拿出成品,科研单位要“一竿子插到底”的理念密切相关。王大珩曾说:“实践证明,科研与实际结合既争取了时间,又保证了质量,可以取得又好又快的效果,还锻炼了一支科研与工程技术结合的人才队伍。”长春光机所有几位研磨技师,水平最高的那一位职级相当于副教授中的最高级。每次王大珩看见他们都笑呵呵地打招呼。
这也与长春光机所强调的“敢打敢干”精神密不可分。“王立鼎院士把国产设备加以改造,做出世界上精度最高的齿轮,这种敢为人先的精神,注重探究思考、勤于科学实践的工作方式,一直在所里传承,激励年轻人不断奋发向上。”长春光机所原所长唐九华评价道。
随着直驱技术的进步,工业上可以使用成型砂轮磨齿技术在机床磨制小批量的2级精度齿轮,但依然达不到1级精度齿轮的整体技术要求。
“我们希望把工艺传承下来,今后一旦国家急需1级齿轮,哪怕只需要一个,我们也能立刻在现有的加工和测试成套设备上完成这一任务。”王立鼎说。
而由超精密齿轮延伸出的技术,目前已应用于高精度齿轮刀具、高精度谐波齿轮、渐开线样板制造工艺等领域。
“就国内现在生产的标准齿轮来说,其制造精度低于国外1~2个级别。如果把标准齿轮整体提升1个等级,其精度指标便可以与多数西方国家同类产品水平相当,将有助于摆脱我国高端机床长期依赖进口的现状。”王立鼎表示。
“如果国家有需要,我愿意随时指导、传授相关加工技术。”如今的王立鼎已年逾九十,但他那颗“工业报国”之心,始终驱动他创新求索,至今熠熠生辉。
受访者供图 蒋志海制版
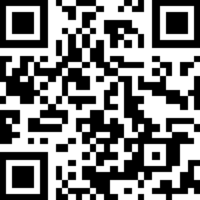
“掌”握科技鲜闻 (微信搜索techsina或扫描左侧二维码关注)
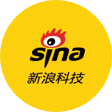