转自:中国能源报
作为一家天然气供应企业,佛燃能源为何要推出节能系统,帮助客户节约气、少用气?
佛燃能源所在地——广东佛山市,被誉为陶瓷之都,陶瓷行业是工业用气大户。截至2024年10月,佛山市成规模的陶瓷企业共有25家,陶瓷生产线131条。佛山市的陶瓷企业专注于生产多种高品质产品,包括但不限于抛釉砖、抛光砖、仿古砖、岩板和外墙砖,可满足不同市场的需求。
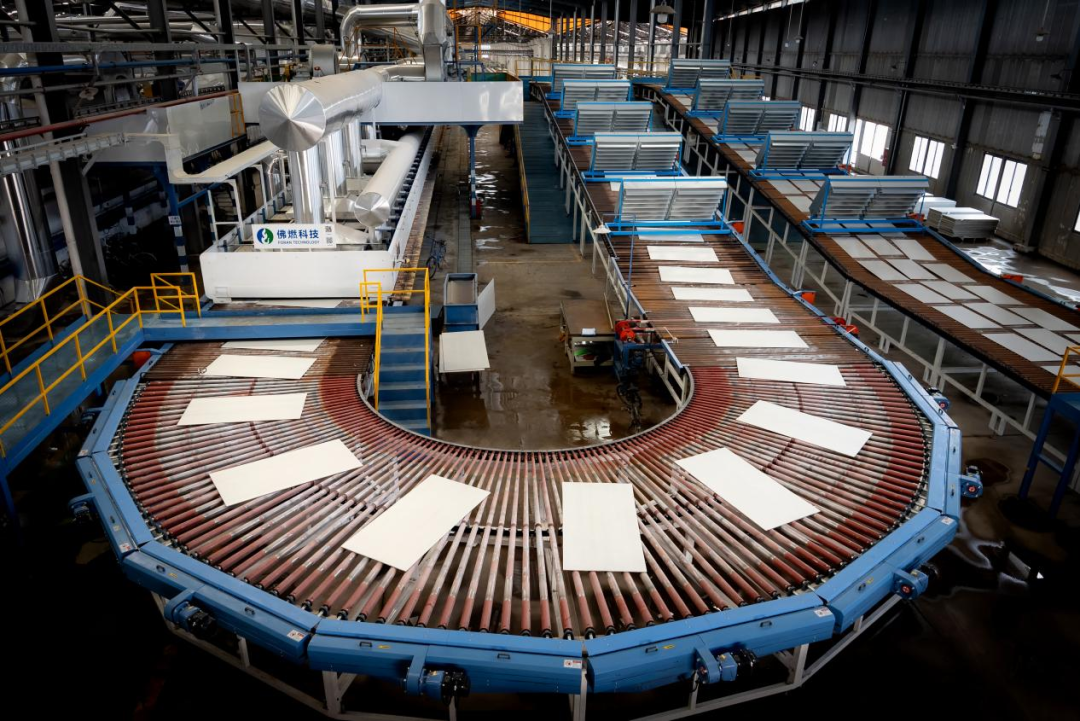
“传统陶瓷产业是能源、原材料消耗大户,其生产过程中的能耗问题一直是社会关注的焦点。” 佛燃能源旗下企业佛燃科技的工业燃烧与节能减排部负责人郭州指出,当前,受房地产行业下行及建筑陶瓷行业市场供需关系影响,陶瓷行业“内卷”严重。其中,燃料和电能消耗在瓷砖生产成本中占比超过40%,节能降本,提质增效成为陶瓷生产企业的迫切需求,在国家“双碳”政策的引导下,陶瓷生产加工势必要走一条资源节约型、环境友好型的新型工业化之路。
国家发改委等五部门2023年6月发布的《工业重点领域能效标杆水平和基准水平(2023年版)》要求,各地引导陶瓷、纺织等重点高耗能企业在规定时限内改造升级到能效基准水平以上,并淘汰无法按期达标的项目。基于此,陶瓷企业积极改进工艺设备、引入先进技术,提高能源利用效率,实现绿色低碳转型升级。
基于服务下游用能行业的丰富经验,佛燃科技对高能耗企业发展规律有着深刻的认识。据介绍,近年来,佛燃科技积极开展陶瓷行业的低碳研究,推进余热回收技术、创新燃烧技术、智能云控节能减碳等技术的研发攻关和推广应用,助力陶瓷企业高质量发展,帮助客户节能减排的同时,也抢占低碳技术和低碳市场的先机。
不同于其他行业,陶瓷窑炉节能改造具有哪些特点和技术难点?据介绍,陶瓷窑炉粉尘多、温度高,生产消耗的热能主要集中于原料制备、烧成和干燥工序,其中烧成及干燥工艺耗能占企业总能耗70%以上。目前,我国陶瓷生产过程能源利用率为40%—50%左右,而发达国家的能源利用率高达60%以上。相比而言,我国传统陶瓷企业的用能方式还较为粗放。而陶瓷厂家普遍拥有一套成熟的技术体系,在此基础上对设备进行节能优化改造,无疑是对节能服务企业提出了更高的要求。
近年来,河南、成都、淄博、佛山等省市纷纷给予窑炉节能改造真金白银的支持。比如,淄博市出台了《窑炉数字化提升行动计划》,提出全力支持窑炉改造建设,对已完工且达标的改造项目,列入市两化融合优秀项目,最高给予50万元一次性奖励;佛山发布《关于高质量推进制造业当家的行动方案》,重点推动陶瓷、纺织服装等传统制造业数字化改造。建设一批数字化示范工厂、示范车间、示范项目,对数字化示范工厂最高奖励2000万元、示范车间最高奖励200万元、示范项目最高奖励800万元。用好总规模300亿元转型发展基金,鼓励社会资本积极参与推动转型发展。
搭建数字化工厂系统平台,可以让陶瓷生产的用能情况精准化、直观化和可视化。佛燃科技针对陶瓷烧成窑,推出一套智能监控及管理系统,基于精准的数字化控制,实时监控窑炉烧成过程中温度、气氛和压力等工艺参数,根据不同产品的工艺需求,采用大数据云计算方法,自动调节和优化窑炉燃烧系统、排烟系统及冷却系统的参数,在保证正常生产的同时降低能耗,实现能源高效燃烧,提升物料传热效率,降低排烟热量损失,同时提高产品质量稳定性。
郭州举例说:“佛燃科技在三水金意陶生产基地安装了该系统,通过精准采集及控制全窑的工艺参数,实现生产区域智能化自适应调节,保持窑炉各区高效燃烧。该系统在提升产品质量稳定和可靠性的同时,通过优化燃烧和制品传热的效率,降低产品能耗,最高节能率达18.86%。给企业带来实实在在,看得见的实惠。此外,佛燃科技自主设计制造的首条窑炉整线,搭载了自主研发的低碳数字智能化热能利用控制系统,实现了核定烧成(含干燥)能耗低至450kal/kg瓷,处于行业领先水平。”

可以预见,数字技术与窑炉产业深度融合是大势所趋。据了解,佛山是制造业大市,陶瓷建材、金属制品行业规模均位居全省前列,是名副其实的能源消费大市,除了陶瓷行业,佛燃科技还将积极推动低碳数字化热工技术向金属加工等高耗能行业的横向应用推广。
佛燃能源肩不仅肩负为城市提供能源供应的重任,在提升能源利用效率和助力制造业节能降碳方面也积极承担了其应有的社会责任。
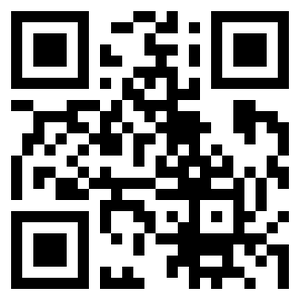
VIP课程推荐
APP专享直播
热门推荐
收起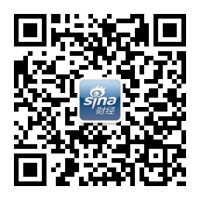
24小时滚动播报最新的财经资讯和视频,更多粉丝福利扫描二维码关注(sinafinance)