英飞凌1992年开始碳化硅技术研发,是第一批研发碳化硅的半导体公司之一。2001年推出世界上第一个商用碳化硅二极管,此后生产线不断升级,2018年收购德国Siltectra公司,2019年推出碳化硅CoolSiCTM MOSFET技术,2024年推出了集成.XT技术的XHPTM 2 CoolSiCTM半桥模块。英飞凌持续32年深耕碳化硅功率器件,不断突破不断创新,持续引领碳化硅技术发展。
本文引用地址:
近日,英飞凌在北京举办碳化硅媒体发布会,深入介绍了其在碳化硅功率器件产品及技术方面的进展及其在工业与基础设施领域的应用和战略布局。
碳化硅变革绿色能源
在全球政治经济多变的背景下,绿色、环保、低碳成为各国共识。IEA报告显示,绿色能源涵盖的发电、输配电、储能、用电等电力全价值链市场潜力巨大。到2030年,光伏装机量超5000GW,电网投资将达每年6000亿美元以上,电池储能容量将增加1000GW以上,电动汽车充电领域投资将超1万亿美元。据介绍,中国在高压直流输电、新能源产业发展迅速,如国内约90,000台风力发电机、超220GW光伏发电机组、约15GW/30GW新型储能系统以及2,800多列高铁都应用了英飞凌产品。
碳化硅作为满足可持续性能源生产和消费的核心技术,其产品创新、生产工艺创新和系统应用创新为客户带来高能效、系统级性价比和寿命周期可靠性的升级,驱动可再生能源发展和电网升级、电动汽车普及扩展以及工业和消费类应用的能效和智能提升。据预测,2024 - 2029年全球碳化硅市场规模将从31亿欧元增长到90亿欧元,年复合增长率超过24%。
解决碳化硅产品痛点

针对碳化硅产品一致性、领先性、创新性、经济性和适应性等痛点,英飞凌科技高级副总裁、工业与基础设施业务大中华区负责人于代辉先生表示,英飞凌作为IDM厂商,在技术和产品稳定性上,从芯片到封装协同效应明显,严格的质量管理体系可确保产品质量;在供货上,采用多元化采购,与中国本土及全球供应商签订协议。在技术驱动上,已积累近3万项专利,拥有冷切割、沟槽栅、以及封装等全球领先技术,并采用严苛的测试标准。在追求卓越方面,已推出多款全球首款产品并获多项奖项。产能布局上,奥地利和马来西亚工厂虚拟协同,,形成规模经济。同时,注重与中国市场和客户的深度融合,“融入市场,融入客户”,充分了解本土市场需求、加快对市场和客户的响应速度、加强本土应用创新能力,加深对本土需求和系统的理解,从而为国内客户提供“端到端”增值服务。
碳化硅何以英飞凌
会上英飞凌科技副总裁、工业与基础设施业务大中华区市场负责人沈璐女士向我们分享了关于英飞凌碳化硅的一个目标、两个误解以及三个持续。

在全社会正进行低碳化以及电气化转型的大背景下,英飞凌设立的一个目标是要成为首选的零碳技术创新伙伴。
新能源架构中能源转换次数逐步增加,尽管可再生能源免费,但每次转换都有能效损失,因此高效能源转换至关重要。碳化硅技术是提升能效的功率半导体技术,旨在满足低碳转型中的两大需求:能效创新(如光伏、储能、充电桩)和设计创新(系统小型化、低成本、节能高效)。英飞凌表示,碳化硅商业模式的成功在于与客户联合创新,以找到能效和设计创新的正确方案。
其次是关于碳化硅的两个误解,第一个误解是,大众认为平面栅结构比较简单,可靠性似乎更高,而沟槽栅结构和生产工艺都很复杂,可能会有长期可靠性的问题。
但实际情况是,在可靠性上,硅器件与碳化硅器件的关键部分在于“栅极氧化层”。若将电流比作汽车,栅极氧化层即为路面。硅基上的栅极氧化层平坦如高速公路,而碳化硅上的则崎岖如乡间小道,因其缺陷密度更高,影响器件寿命,导致失效。为提升碳化硅可靠性,需降低其栅极氧化层缺陷密度。英飞凌采用高效测试方法,用高筛选电压筛选器件,电压越高,发现缺陷越多,筛选出的器件可靠性越高。
平面栅技术难以实现高可靠性,因其如车行颠簸路面,速度受限。沟槽栅技术则如挖隧道,速度更快。若平面栅要达到沟槽栅速度,需更薄的栅极氧化层,但筛选电压与氧化层厚度成正比,薄氧化层难以承受高电压筛选。因此,英飞凌的沟槽栅技术通过更厚的氧化层和更高的筛选电压,最大限度降低缺陷密度,保障可靠性。
第二个常见误区是关于碳化硅性能的评价。常听到只看单位面积导通电阻(Rsp)来评价器件好坏的说法,但这并不全面。碳化硅的商业价值在于长期、可靠、高效的能源转化效率。能量损耗由导通损耗和开关损耗组成,随着碳化硅高频开关应用的出现,开关损耗越来越重要。例如,在60kHz的开关频率下,导通损耗已远小于开关损耗。除了芯片损耗,封装参数如热阻也影响能效转换。模块杂感优化对功率输出和频率稳定性也很重要。此外,鲁棒性和可靠性也是关键,包括长期使用寿命和极端工况下的稳定性能。
关于高温漂移,沟槽栅和平面栅的电阻变化不同,并非产品可靠性问题。导通电阻由沟道电阻A和外延层电阻B组成,它们的温度特性相反。平面栅的沟道电阻A占比大,能补偿B的上升,所以导通损耗受温度变化影响小。而沟槽栅的沟道电阻A占比小,无法补偿B的上升,导致高温漂移。因此,碳化硅性能评价标准应多元化,包括导通损耗、开关损耗、杂散电感、封装热阻以及鲁棒性和可靠性。英飞凌为用户提供详尽的设计参数,帮助工程师充分利用每个器件。
对于三个持续,沈璐表示:“第一我们要持续布局,步履不停。第二持续创新,超越期待。第三是持续深耕,穿越周期。”三个持续是英飞凌对于碳化硅业务的坚定选择,也是英飞凌应对市场挑战的信心。
第二代CoolSiCTM MOSFETs惊艳亮相
英飞凌持续布局碳化硅业务,从芯片技术迭代到生产线升级,不断满足客户多元化需求,避免同质化竞争。英飞凌的目标是减少工艺损耗、优化散热性能,以保持高可靠性。从CoolSiCTM MOSFETs第一代到新一代技术,英飞凌一直致力于降低损耗、提高散热性能和可靠性。
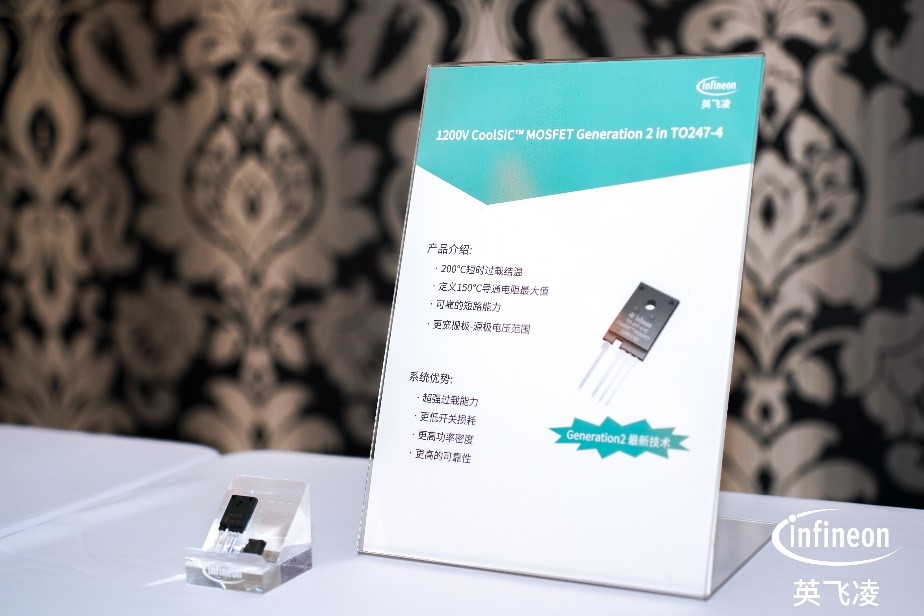
CoolSiCTM MOSFETs G2的电阻范围从7毫欧到78毫欧,其中7毫欧是业界工艺密度之最。与G1相比,G2具有更低的损耗、更好的散热、更易用且更宽的VGS范围。同时G2还增强了开关性能,降低开关损耗,提高功率效率。
RDSON*QGD品质因素反映开关损耗。在开关过程中,QGD和RDSON的乘积影响开关损耗和导通损耗的平衡。乘积越小,损耗越低,器件性能越好,这在硬开关应用中尤为重要。不同应用和拓扑结构对器件性能要求不同。英飞凌优化了驱动损耗等其他因素,使G2系列表现最佳。在半桥拓扑测试中,通过对比,包括与第一代产品的比较,G2整体效率更高。
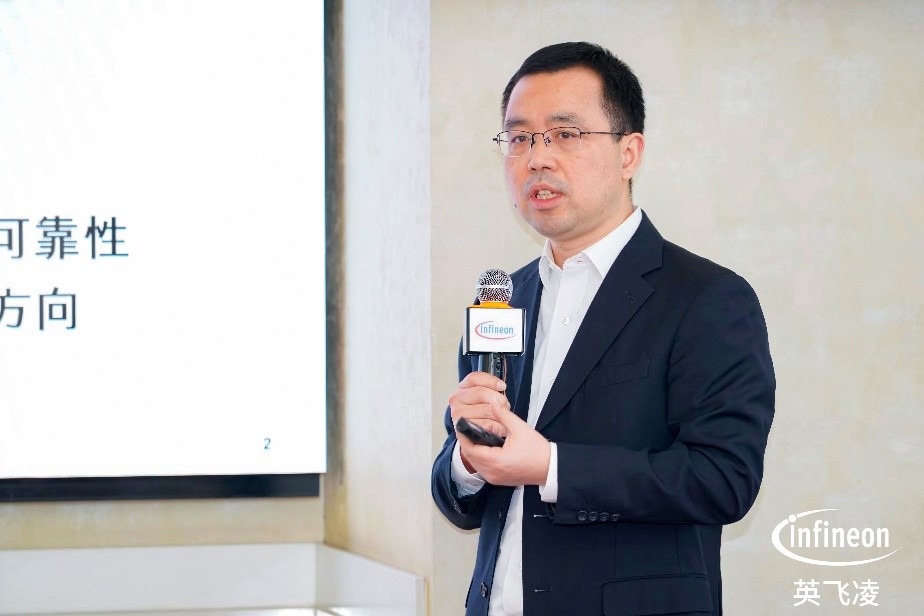
值得一提的是G2采用了英飞凌.XT互连技术和扩散焊技术。英飞凌科技高级技术总监、工业与基础设施业务大中华区技术负责人陈立烽先生介绍到,“在传统器件中,无论是单板还是模块,通常采用标准焊接方式,即将芯片焊接到芯片引线框架或者DCB等载体上。然而,通过X光或者显微镜观察,标准焊接过程往往难以达到完全平滑的焊接效果。相比之下,采用.XT扩散焊技术则能显著改善这一情况。该技术使得芯片与载体之间的结合处变得非常紧密。这种紧密的结合不仅有助于降低热阻,提高散热效率,还能显著提升焊接的可靠性,从而增强器件对于温度热应力的抵抗能力。”
在工艺水平方面,英飞凌采用了冷切割技术,能够更加充分的利用材料,特别是在工艺器件生产的一道工序减薄环节中。
未来,相信英飞凌会继续深耕在碳化硅领域,并持续创造出引领行业发展的碳化硅产品。
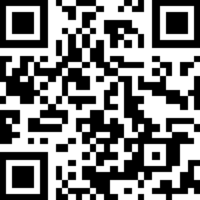
“掌”握科技鲜闻 (微信搜索techsina或扫描左侧二维码关注)
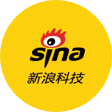