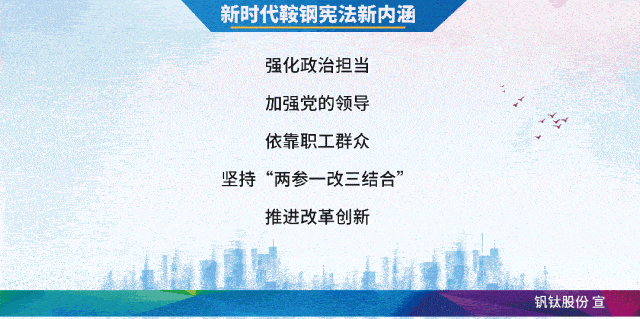

【《中国冶金报》编·语】
开钒氮合金数字化生产之先河
樊三彩
国内的钒氮合金生产目前仍以传统生产方式为主,作为首条钒氮合金数字化生产线,意味着没有任何过往经验可借鉴,在全国50多家钒氮合金生产企业中,攀钢成为“第一个吃螃蟹”的企业。
成为开先河者,就要系统地解决很多问题,敢于打破诸多常规,包括可预测和不可预测的问题,难度不小。首要难题就是确立科学的建设模式。要大规模改造这条国内首屈一指的年产8000吨钒氮合金生产线,需要在不影响生产的情况下实现升级,这个过程尤其需要精心设计、小心协调,即使在有规划图的情况下,也要随时准备应对计划之外的情况。例如,一次筛分接料装置(筛分机与料斗的衔接部分)起着将筛分后的料球缓冲并送入料斗的作用。最初的设计是一个螺旋形滑梯结构,但安装后发现它达不到预期的效果,要么料球不往下滑,要么滑下去速度太快导致碰碎。在现场,通过生产方和设计方集思广益、共同努力,最终采用了逆向旋转的斗提结构,完美解决了问题。
除了生产管控层面的难题,攀钢在数字化工艺、技术研发上也敢为人先,实现完全自主研发。以混配料模型为例,配料的比例原本只能保密进行,现在则需借助模型,这对于企业商业机密的保护提出了极高要求。攀钢最终通过签订保密协议、技术人员和工艺人员协同研发等方式确保了模型的成功开发。在推板窑模型的设计上,要实现远程数字化集控,就要对窑内生产情况进行实时监控。攀钢通过精准收集数据、调适设备连接方式,将窑内各部分温度、压力、流量等参数以及坩埚运转过程等以三维可视化的形式综合展现,并开发实现统计功能,实现对窑内情况的精准仿真模拟,变“黑箱”为“白箱”,打造了推板窑场景下的“黑灯工厂”。
作为钒氮合金数字化生产的先行者,攀钢敢于突破、敢为人先的创新精神,问题导向、独立自主的探索能力值得业内很多企业学习借鉴。

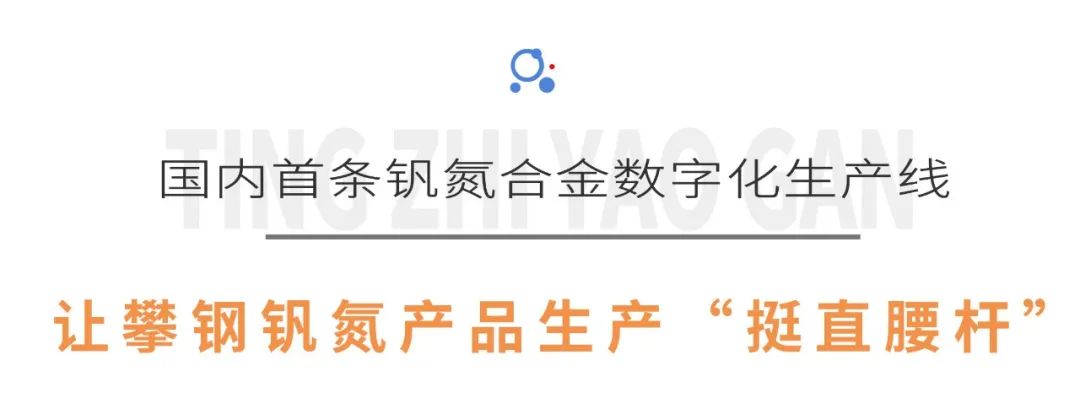
9月20日早上,换好工作服的倒班作业长江滔走进钒氮合金智能化中控室,通过察看大屏幕数据显示和视频画面,钒氮合金智能制造示范性产线的运行情况及主要指标变化情况一目了然。他到现场确认完毕后,快速返回中控室,组织召开了班前会,对当班任务进行了分工,交代了注意事项,整个过程不到20分钟。这是钒氮合金产线智能化改造前至少要花一个小时才能完成的工作。

鞍钢集团攀钢集团首批两化融合示范线建设项目——攀钢钒钛资源股份有限公司(下称“攀钢钒钛股份”)钒氮合金两化融合示范线建设项目(此为申报前采用的项目名称),成功融合了信息、制造、控制、通信、人工智能和5G等先进技术,并率先在国内钒制造领域实现了智慧物联传输、生产物料自主运转、产品自动包装、全线集中远控和物流连续自动等功能,是国内第一条钒氮合金数字化生产线。2023年11月份,该项目入选2023年度智能制造优秀场景。

钒氮合金主要用作含钒微合金钢添加剂,微量加入就能显著改善钢材的综合力学性能和焊接性能,是目前钒产品市场的主流产品之一。但因其生产工艺复杂,生产条件要求高,2018年以前,国内还没有钒氮合金生产企业做过全流程自动化、智能化生产方面的尝试。
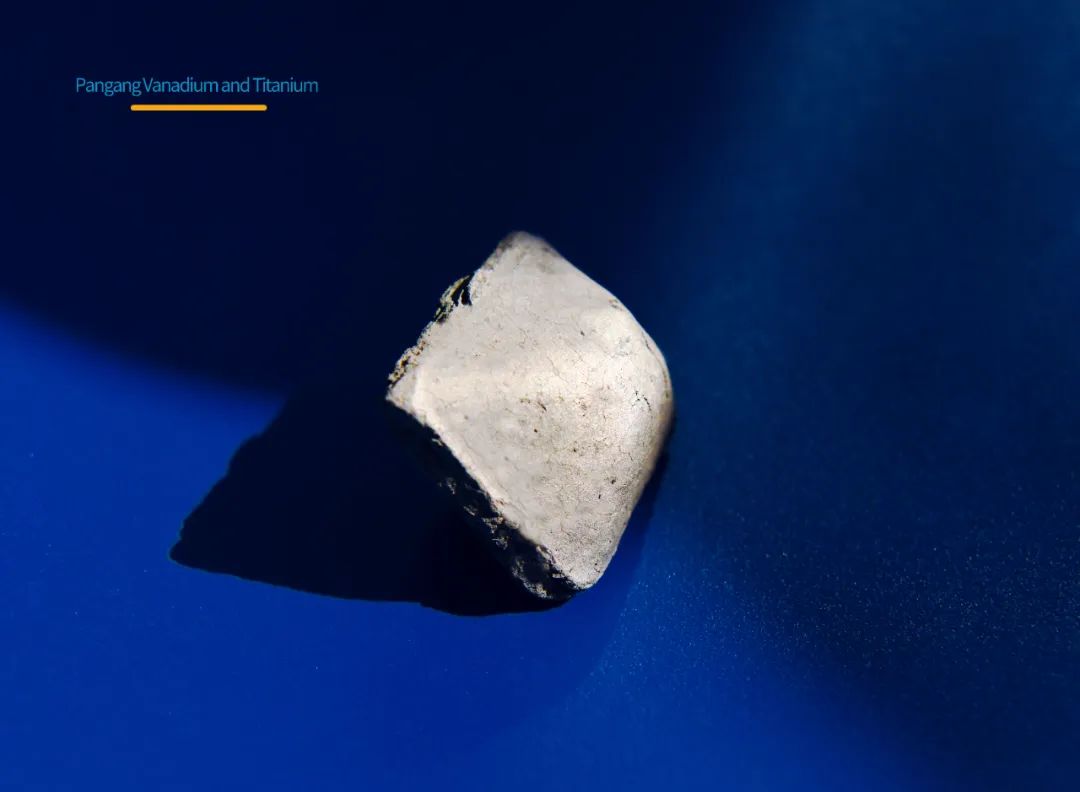
攀钢钒钛股份下属攀枝花钒制品分公司拥有在世界钒制品生产企业中处于领先地位的钒氮合金完整生产线。但由于产线建设时间较早,受场地和技术条件限制,各工序离散作业、自动化程度低、缺乏过程控制、人工作业环节多、劳动强度大、生产现场环境差,产品信息全靠人工记录和纸片传递,设备故障排查时间长,生产过程质量追溯难以开展,建设钒氮合金智能化产线具有重要的探索意义。
2018年初,攀钢立项实施钒氮合金两化融合示范线建设项目。攀钢集团旗下成都星云智联科技有限公司作为项目总承包方,与攀钢相关单位携手,按照“整体策划,分步实施”的工作思路,从技术设计、功能实现、方案实施等方面开始了大胆探索。
2019年下半年,随着机械臂自动卸料装置、无人吊车、AGV叉车和自动包装线等智能化设备,以及配套的5G信息化、物联网等系统陆续在攀枝花钒制品分公司钒氮合金生产线投用,钒氮合金的传统生产方式逐步改变。

2020年,机械臂卸料装置的稳定运行,结束了攀钢集团钒氮合金煅烧工序生产全靠人工上卸料、搬坩埚的历史;智慧物联传输系统打通了生产过程中的物流断点,实现了钒氮合金生料球和成品的物流自动运转和集中控制;生产可视化系统对主要工艺参数、人员生产行为、设备在线状态数据进行了采集、存储、分析,对异常情况及时报警并集中显示,基本实现了即时调度和责任追溯等功能,有效减少了事故停机、事故扩大化等情况;生产过程控制系统紧密结合MES(制造执行系统)建设,通过对各单元生产数据的实时自动收集和高效准确传递,实现了各生产工序间的横向及纵向信息集成,基本实现了工艺过程控制自动化;生产物料自主运转系统配套无人吊车、AGV叉车等智能设备,实现了生产物料的自动转运;产品自动包装线建成投用后,实现了钒氮合金产品的自动破碎、输送、称量和封口等功能。
一系列自动化、智能化装备及5G技术陆续在攀钢钒钛股份攀枝花钒制品分公司生产现场落地生根,让钒氮合金产线的作业模式和生产环境发生了巨大变化,焕发出勃勃生机。

“未实施智能化改造前,我们在钒氮合金生产过程中,全靠人工进行上卸料、配料及物料倒运和包装等操作,劳动强度大。尤其是在煅烧工序,单个石墨坩埚装满生料球后,重达60公斤以上,全靠人工搬运,同时还要注意洒落在地上的石墨细粉,稍不留神就会脚下打滑,职工们干活都是弓着身子,小心翼翼地挪步,每天都是灰头土脸、汗流浃背。如今,职工在集成控制室中,就能清晰地掌握现场生产过程的重要控制参数变化和物料转运情况,及时发现设备故障,避免事故扩大化,生产作业效率得到明显提升,现场作业环境也得到极大改善,靠人工搬运坩埚、弓着身子在煅烧现场来回‘溜冰’的日子彻底成为历史。”全程参与了钒氮合金两化融合示范产线建设的攀枝花钒制品分公司钒氮产线技术员唐琪对改造前后的变化深有感触。
攀钢钒钛股份本身就拥有多项钒氮合金核心生产技术,近年来又持续开发了高氮钒氮合金制备、钒氮合金品位稳定控制等一系列原创性关键技术。钒氮合金两化融合示范线建成投用后,不仅产线用工优化22%,而且所生产的钒氮合金具有氮含量高、品位稳定、表观密度高等特点,产品畅销国内外市场,深受顾客喜爱。2022年11月,攀钢钒钛股份的钒氮合金产品获评为工信部、中国工业经济联合会联合发布的“制造业单项冠军产品”。
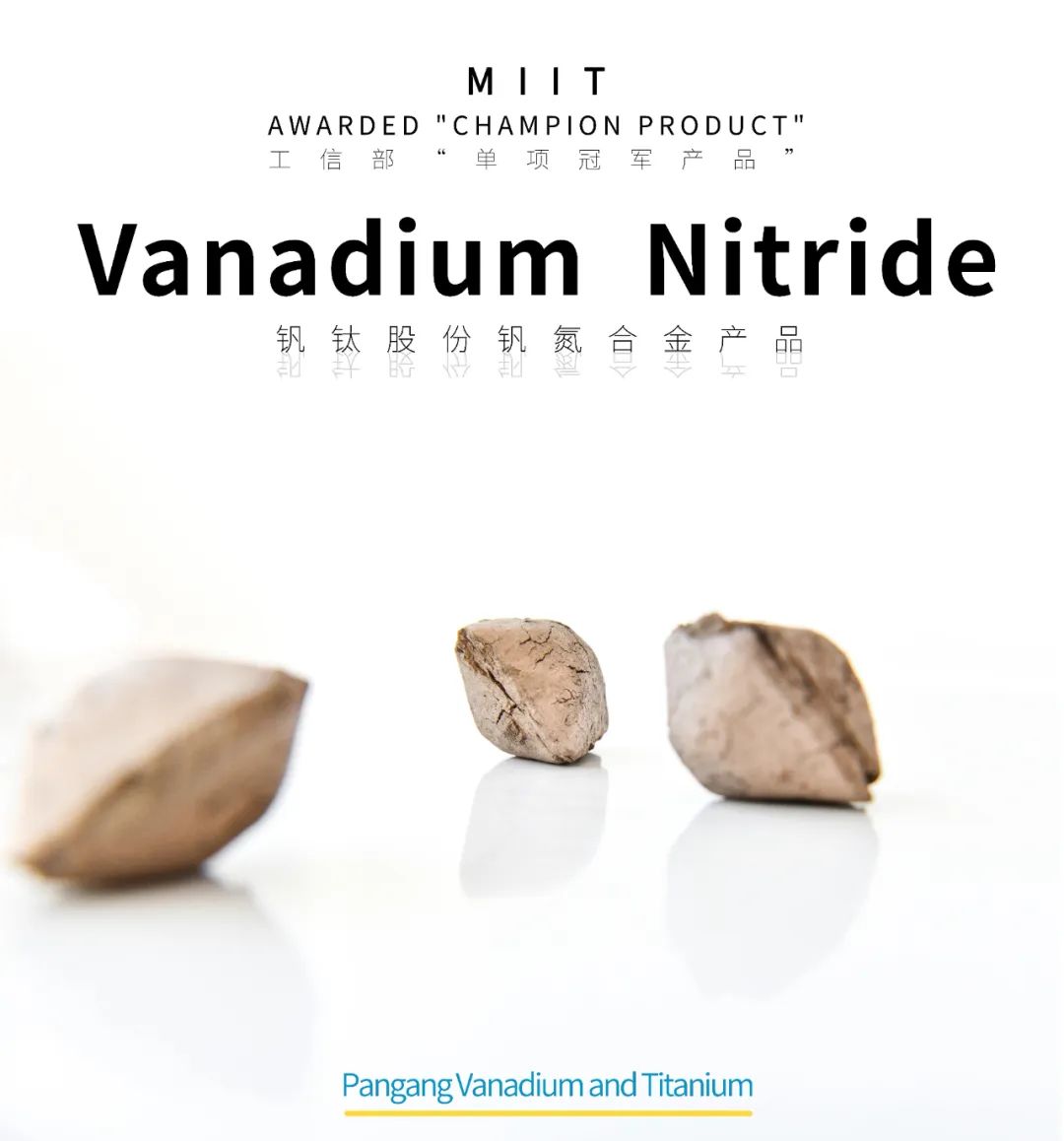
同时,攀钢钒钛股份将钒氮合金两化融合示范线建设的成功经验应用推广到旗下攀钢集团西昌钒制品科技有限公司智慧工厂一期、二期建设,有效解决了钒产业制造流程长、工艺机理复杂、工序断点多等诸多难题,实现了工厂生产态势感知与运营一体化智慧管控等,获评为中国软件行业协会2024年度中国企业数字化创新应用场景。

数字化智能化技术的成功应用,为攀钢带来了一系列的实绩和荣誉,让攀钢钒氮合金生产由“人工制造”迈向了智能制造,也让攀钢钒氮产品生产“挺直腰杆”。
文:孟祥林 李伟
(转自:钒钛股份)
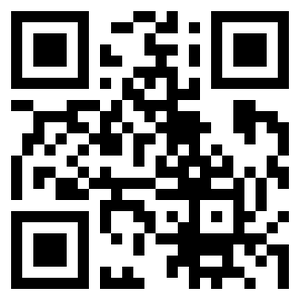
VIP课程推荐
APP专享直播
热门推荐
收起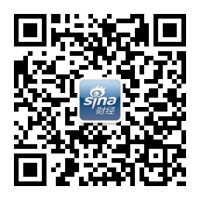
24小时滚动播报最新的财经资讯和视频,更多粉丝福利扫描二维码关注(sinafinance)