新华社北京9月23日电 《经济参考报》报道,记者朱国亮和王皓然撰写的《数字化赋能:特钢行业如何实现“六最”?》一文指出,中信泰富特钢集团旗下的江阴兴澄特种钢铁有限公司(简称“兴澄特钢”),借助数字化和智能化技术,不仅实现了产品每七年更新换代一次,而且在钢铁行业波动中连续三十年保持盈利。记者近日访问了这个全球首个特钢行业的“灯塔工厂”,探索其背后的科技秘密。
步入占地约12万平方米的兴澄特钢厚板车间,可以看到偌大的厂房内鲜少有人作业,取而代之的是机械臂忙碌的身影,一片片炽热的钢板被连续不断地压制成型并送至冷却区。厚板车间综合室主任奚正信透露,得益于5G网络覆盖和自动化上下料系统,平均每块钢板的生产时间不超过两分钟。
在中信泰富特钢集团的数智中心,记者仿佛置身于未来世界,环形的显示屏上展示着炼铁、炼钢、轧钢各个环节的实时数据流。兴澄特钢智能及信息化部工程师李锰涛解释道,通过这些数据可以实时监控高炉、转炉、精炼炉的运行状态,以及各个环节的能耗情况。
兴澄特钢副总经理王永建表示,全流程数字化管理为公司实施高定制化、高品质、高效能和可持续性的生产模式奠定了基础。他提到,在最新的智能化改造中,兴澄特钢引入了四十多项先进的工业4.0技术案例,从而显著提高了产品的合格率和生产效率,并降低了生产成本。
王永建进一步举例说明,在炼铁过程中,通过大量的传感器和数百个算法模型,使高炉内部的操作变得透明化,这不仅使烧结矿的质量稳定性从98.1%提升到了99.5%,还减少了84.8%的高炉异常时间,降低了19.1%的焦炭消耗,并节省了大约1亿立方米的煤气,减少二氧化碳排放达10万吨。而在炼钢和轧钢环节,通过实时监控成分和过程控制,提高了产品合格率,并通过AI模型优化加热炉燃烧,提升了轧制效率,减少了钢坯在炉内的停留时间,增加了钢板的产量,加快了交货速度。
在中信泰富特钢集团的展示厅,一句标语“特钢是科技的结晶”令人印象深刻。王永建强调,过去三十年,兴澄特钢始终专注于钢铁制造和工艺改进,尤其是在新世纪以来,以信息化、智能化、数字化为驱动力,不断创新管理和工艺,每年淘汰10%的产品,每七年完成一次产品线的全面更新。
兴澄特钢以六大“最”产品自豪,包括最低氧含量的轴承钢、最长寿命的弹簧钢、最高强度的桥梁缆索用钢、最优屈强比的系泊链钢、最大直径的连铸圆坯以及最细的金刚线盘条。
企业研究专家周放生指出,持续推动产品升级是制造业发展的铁律。兴澄特钢从普通钢转向特钢,并通过信息化建设和技术创新保持了三十年的盈利状态,证明了这一点。
冶金工业信息标准研究院院长张龙强认为,当前钢铁行业正处于“减量优化”阶段,面临严峻挑战,而智能化和数字化是降本增效的关键。他指出,国内钢铁行业的数字化转型已取得一定进展,但仍存在不均衡的问题,一些企业尚未充分认识到数字化的重要性或缺乏明确的转型路径。
展望未来,王永建表示,兴澄特钢将继续深化全流程、全工序的数字化工作,并分享其成功经验,助力行业进步。
来源:新华社
(转自:特钢技术)
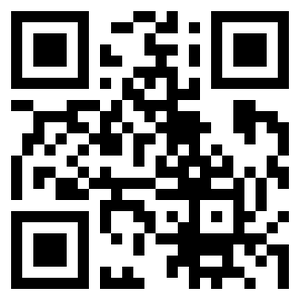
VIP课程推荐
APP专享直播
热门推荐
收起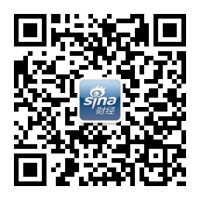
24小时滚动播报最新的财经资讯和视频,更多粉丝福利扫描二维码关注(sinafinance)