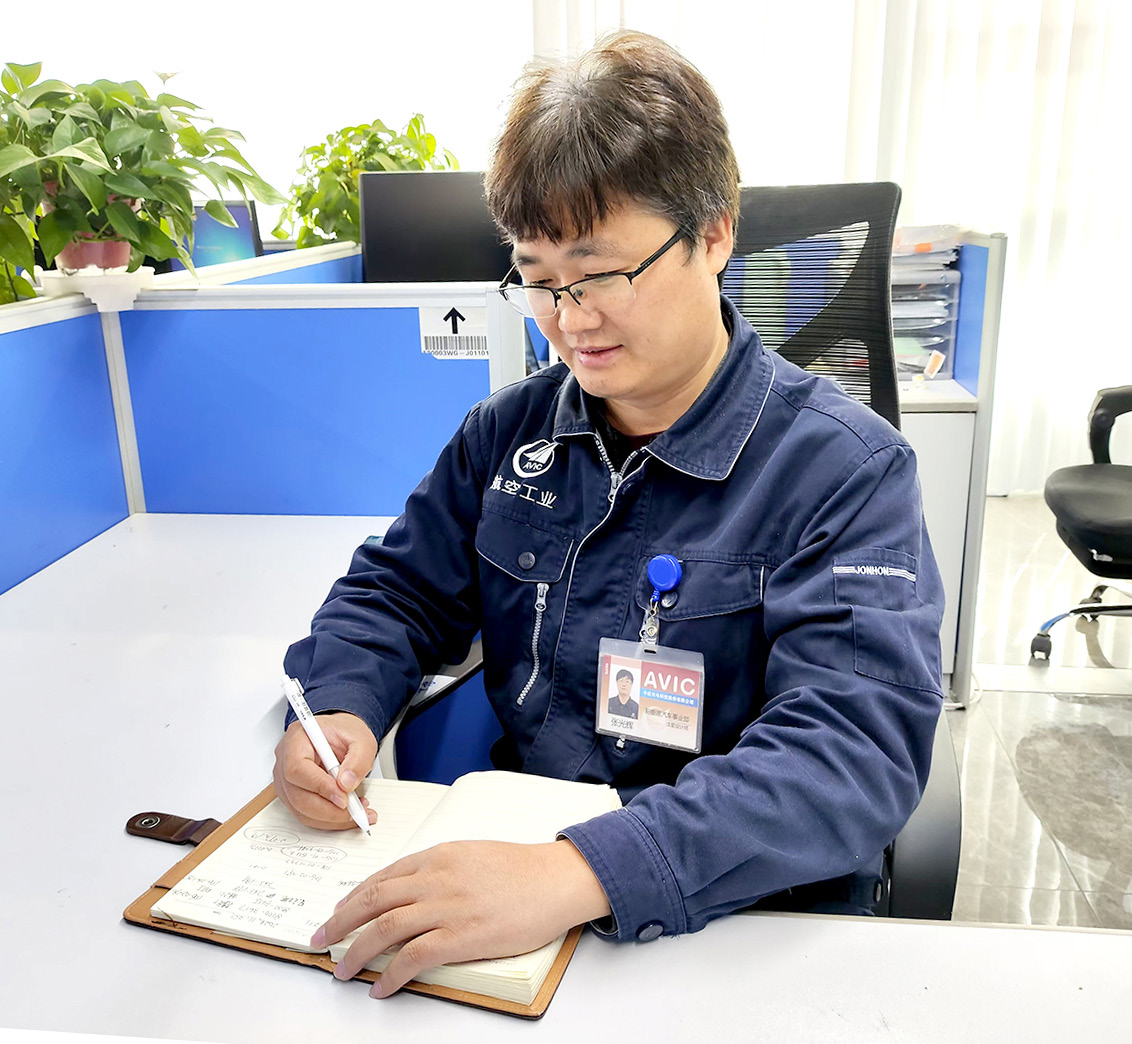
“你看,这个零件表面还有拉丝纹,达不到镜面标准。”“这个光一照就能看到水流纹”……设计员张光辉微微皱着眉,对着光源反复地审视着手里的零件,一丝不苟地“挑毛病”。零件哪个部位容易出现问题,怎样才能发现问题,他心里门儿清。不了解的人会觉得他“吹毛求疵”,只有和他一起经历过项目攻关的人才知道,正是这样的精益求精,才能一路过关斩将推动“项目定点”走向“批量交付”。
外观零缺陷
“公司拿到了一款高端车型的‘项目定点’!”消息传来,张光辉兴奋之余也感到了巨大的压力。因为客户提出:“我们要的是零缺陷,产品外观不能有任何问题。”进入方案设计阶段,张光辉才知道“零缺陷”有多难。划痕、擦伤、磕碰、水印、颜色不一致……这些问题像一道道紧箍咒让张光辉的心情像被压在五指山下一样沉重。然而最难的还是产品的局部电镀。
不走寻常路
为了体现高端设计感提升视觉效果,客户要求对产品的指定部位进行局部电镀,但产品设计采用的是一体化结构,怎样做到无痕分界是一个大难题。张光辉和项目组反复沟通,迅速制定了电镀方案,对无须电镀的部位设计了遮挡防护。然而在打样过程中,虽然实现了遮挡部位没有镀层,但电镀液会顺着遮挡物渗入零件缝隙处并积存,在零件表面留下明显的印痕,严重影响外观质量且无法后期消除。
张光辉陆续改进了几版方案,样件状态仍不理想。时间一天天过去,距离样件交付节点越来越近,张光辉陷入了极度焦虑之中。在一个寂静的夜晚,感到山穷水尽的张光辉离开电脑看向窗外,想休息一下疲惫的双眼。面对天际的一轮孤月,他的心中突然灵光乍现:既然局部电镀无法做到完美无瑕,那改变产品的设计结构是否可行呢?他兴奋地拿起电话,马上联系了电镀专家、模具专家……
经过多方评估,产品的一体化结构最终被改成了可拆卸模式,需要电镀的部件单独电镀后再与其他部件进行组装,产品的各个部位互不影响,外观完全达到用户要求并顺利提交,张光辉的脸上露出了难得的笑容。
经得住检验
“张师傅,这么漂亮的Logo怎么到你这就是‘见光死’”呢!”一个工人见张光辉又拿着放大镜在聚光灯下反复检查产品的Logo,稍带怨气地说。“你看这个角度,是不是有波纹?用放大镜看,表面是不是有拉丝?这个边界看起来不够顺滑……”张光辉耐心地解释,“不是我要吹毛求疵,你不知道,样件交验时客户每换一次角度,我就捏一把汗,虽然方案改过无数遍,但在三方客户的眼中仍有问题呀!”
面对一款合格率仅有百分之二十几的产品,张光辉陷入了沉思:合格率低不能只靠工艺和检验,必须从产品的设计源头找问题。客户对Logo的要求是流畅、镜面、高端,原设计采用嵌入铝合金片、黑色树脂填充Logo线条的方案。但金属无法避免表面拉丝、填充会有表面不平整现象,要彻底解决这些问题,必须更改设计方案!
张光辉不厌其烦地奔波在供应商和客户之间,不断尝试新方法找寻新材料,历时两个月做了无数试验,终于完成了新材料、新工艺的完美搭配:采用PC透明壳,从背面印制后装配,既能保证表面的光滑度,还可以对Logo起到整体保护作用。最重要的是合格率,可以提升至90%以上,大大提高了生产效率,降低了检验难度!这一方案提交后,经受住了客户“放大镜、多角度、多光源”的检验,客户非常满意,项目顺利进入量产阶段。
批产后的产品,“苛刻”的外观需要尽善尽美的生产流程来保障。张光辉编制了详尽可行的外观检验规范,以及多达16页涉及27条的图文示例。他还设计了专用吸塑盒,从源头上消除影响产品外观的因素。每个环节每个细节,张光辉都考虑了一遍又一遍。他秉持着“不将设计问题传到生产,不设计不能管控产品”的原则,对自己主管的设计方案“吹毛求疵”、精益求精,从2022年底产品定点到2023年10月产品量产,经受住了“零缺陷”的挑战,充分展示了中航光电设计人员的卓越风采,让中航光电“专业、可靠、高端”的品牌形象熠熠生辉。
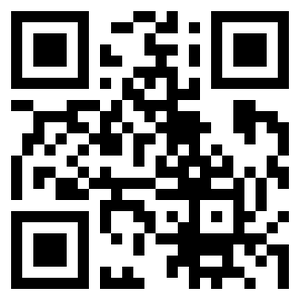
VIP课程推荐
APP专享直播
热门推荐
收起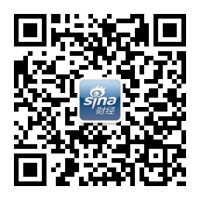
24小时滚动播报最新的财经资讯和视频,更多粉丝福利扫描二维码关注(sinafinance)